En esta serie de artículos estamos detallando cómo se fabrican los automóviles de baja producción. Vimos cómo se diseñan, se fabrican sus chasis y motores. A mitad de montaje saltamos al Reino Unido, un país con una gran cultura del automóvil y especialista en automóviles especiales, tanto en lujo como en deportividad, para hacer una parada y ver cómo trabajan.
En el artículo anterior vimos cómo se fabrican las berlinas más lujosas por excelencia, Bentley y Rolls-Royce, dos marcas diferentes que ponen un mimo extremos en sus acabados. En este artículo veremos cómo son fabricados los grandes turismos, deportivos supertecnológicos y superclásicos en el Reino Unido.Pongámonos nuestro mejor frac, unos zapatos Crockett & Jones, nuestro Rolex en la muñeca izquierda y la Walther PPK la dejamos en casa, hoy no trabajamos, vamos a Gaydon a recoger nuestro nuevo coche de agente especial del MI6.
Línea de ensamblado de Aston Martin
En el artículo segundo de esta serie vemos que Aston Martin fabrica el DB11 con piezas de aluminio que encola y une por remaches. También vimos que la carrocería es pintada y pulida a espejo. En toda esta parte de la línea de producción tiene tres robots, después de ese punto no tiene ninguno más. La artesanía forma parte del ADN de Aston Martin y la empresa es consciente de ello.
La línea de montaje está en una sala brillante, diáfana y limpia para que los técnicos puedan trabajar concentrados en su labor. Para fabricar un DB11 se emplean un total de 200 horas, quizás pensáis que es poco porque en una gran berlina se tarda el doble, pero pensad que es un cupé y que un turismo normal se puede montar en unas 13 horas.
De nuevo recuperamos nuestra carrocería y nuestro grupo propulsor que nos esperaban en Gaydon. Tanto para entrar a las oficinas como para entrar a la línea de montaje existen dos puertas, una para empleados y visitantes y otra reservada para los clientes, o sea, nosotros.
Colocamos la carrocería en la línea y con mucho cuidado separamos las puertas y capó para montarles los guarnecidos en otra parte. A la carrocería se le añaden los cables, sistemas de seguridad, tuberías y servofreno. En paralelo se han fabricado sillones y salpicadero, el acabado de la piel es tan importante en un Aston Martin como el motor o el pulido de su pintura.
El salpicadero se coloca mientras no hay puertas ni asientos. Esta operación se suele hacer a mano incluso en los automóviles de gran tirada, debido a que es muy compleja la colocación de aislantes térmicos, los conectores eléctricos, climatización y dirección. En un automóvil de serie corta y con elementos de piel tienen mucho menos sentido.
Se realiza a mano, pero no a pulso. Para facilitar los trabajos a los técnicos se usan herramientas manipuladores ingrávidos, esto es, manipuladores que tienen un resorte tarado a la misma fuerza que el peso del salpicadero para poder moverlo cómodamente. También se colocan los parabrisas, a mano, por supuesto, y el techo practicable si lo hemos elegido. Lo habitual en los coches de larga tirada es que los parabrisas sean colocados por un robot que coge el vidrio, lo lleva al dispensador de cola, se acerque al robot, mida su posición exacta y entonces lo plante.
La carrocería viaja en alto con unos transportes mientras se acaba de unir el motor con el tren rodante en otra estación. Después la carrocería se acerca al banco donde tenemos el grupo propulsor y los unimos. Después de asegurarnos que ambas partes están firmes seguimos con cableados y tuberías. Las puertas y los capós regresan a la carrocería de la que fueron separados. La línea de montaje acaba en un túnel de luz para comprobar que la carrocería está perfecta y tiene el brillo adecuado.
Todos y cada uno de los Aston Martin es sometido a una inspección rigurosa de todos sus componentes para asegurar que se ha conseguido la máxima calidad en todos los aspectos. En el primer artículo de esta serie prometimos hablar de los vehículos de muy baja tirada y muy especiales. ¿Cuál es el Aston Martin más especial de todos los que se fabrican?
Podréis pensar que el hiperdeportivo Valhalla es el más especial, pero sus 500 unidades le hacen algo “vulgar”. ¿Tal vez el Valkyrie? Bueno, es muy especial, 150 unidades vendidas de un hiperdeportivo desarrollado en cooperación con Adrian Newe.
Vamos a ver ¿cuál es el automóvil más famoso de Aston Martin? Por supuesto el DB5, que fue catapultado a la fama por su conductor, ni más ni menos que Bond, James Bond. Por el éxito de los DB4 construidos en 2017 por Aston Martin Continuations se ha lanzado el proyecto DB5 Goldfinger con el propósito de construir 25 unidades del modelo que vimos en las películas.
No solo porque se va a construir con la misma carrocería, color y motor como una de las 898 unidades que se fabricaron de 1963 a 1965, si no que se va a construir como la de las películas de 007. Estas unidades se van a construir con el permiso de Su Majestad y de EON Productions, propietaria de los derechos intelectuales de la saga. Estas 25 unidades se construirán con todos los gadgets vistos en las películas.
Las opciones que se están probando para llevarlas a estos vehículos son:
Exterior
- Cortina de camuflaje de humo
- Eyección de aceite resbaladizo (simulado)
- Matrículas intercambiables con mando, tres placas
- Armas de fuego en parte delantera, detrás de las luces (simuladas)
- Pantalla metálica trasera antibalas
- Arietes delanteros y traseros en los paragolpes
- Cuchillas en las ruedas para neumáticos (simuladas)
- Panel de techo del copiloto extraíble (opcional)
Interior
- Pantalla de radar en salpicadero (simulada)
- Teléfono en puerta de conductor
- Pomo de caja de velocidades con pulsador
- Interruptores varios en reposabrazos central
- Armero oculto bajo asiento
- Control remoto para gadgets
Lo que no parece que sea opcional es la pintura, que será plateado abedul. Esta vez no ha sido el agente Q el encargado de los artilugios, si no Chris Corbould, técnico especialista en efectos especiales, participante en 11 películas de Bond y ganador de un Oscar.
Estas unidades se fabricarán en las mismas instalaciones que los DB5 originales, en Newport Pagnell. En estos momentos es el centro de restauración de Aston Martin por excelencia. La manera de fabricar estas unidades será como realizar restauraciones completas de todos los componentes de 25 unidades.
Serán totalmente fieles, incluido su motor, un seis en línea de 4 litros y 294 CV, alimentado por tres carburadores SU. Mantendrá las cinco velocidades, frenos hidráulicos y esquemas de suspensión y no añadirá la servodirección. Ese artilugio no es necesario para el agente más duro del MI6.
El Aston Martin DB5 está construido con la técnica patentada por Touring Superleggera. Esto es, un chasis formado por tubos de pequeña sección y tramos rectos en la parte baja. Los paneles son colocados sobre los tubos y simplemente cierran la carrocería. Este tipo de construcción era típica de los deportivos de mitad del siglo pasado.
Era muy práctico para aligerar el peso, además permitía variar los paneles fácilmente, de manera que con el cambio de los paneles y poco más, podíamos tener un nuevo modelo. Por contra, una chasis de este tipo no soporta la normativa anticolisión actual. Otro problema es que los tubos interiores estaban fabricados en acero y los paneles en aluminio.
Cuando se unen dos metales diferentes se genera una pequeña corriente eléctrica entre ambos que genera electrólisis y acaba corroyendo los paneles. La fabricación actual es básicamente la misma que la original, aunque la química ha mejorado mucho y los paneles están mucho mejor preparados contra la corrosión por electrólisis.
Para la construcción del chasis se cortan los tubos, se curvan y se unen por soldadura eléctrica. A estos tubos se les añaden los tramos rectos de la parte inferior. Todo este trabajo no es nada comparado con lo que hay que hacer para la elaboración de los paneles exteriores. Este tipo de construcción se realizaba para las producciones muy cortas y muy manuales. Cuando se diseñaba el automóvil se generaba un armazón de madera con la forma deseada.
Sobre este armazón se colocaba la chapa cortada y se les daba forma con un martillo y mucha paciencia. Años después se comenzó a utilizar maquinaria automática que es la que aporta la energía y el técnico la pericia. Antes de llegar a la paneladora las chapas han sido recortadas siguiendo la forma de los patrones.
Con mucha paciencia se curvan los paneles hasta obtener la forma deseada. No siempre se puede recurrir a la bateador automática. A veces es necesario recurrir al martillo y otras veces el yunque es la mano. No solo es complejo darle forma, pensad que el vehículo debe ser simétrico, por lo que ambos lados deben se iguales a espejo.
Cuando la forma es muy compleja y tiene superficies cóncavas y convexas a la vez es necesario unir varias piezas. En este caso las piezas son de aluminio, por lo que son soldadas con la técnica TIG (por varilla de tungsteno con gas inerte, argón 100 % en este caso). Después de soldar las uniones, se lijan y repasan hasta que desaparecen y el panel aparenta ser una única pieza.
Después de esto se le añade la imprimación, se protegen los bajos con poliuretano y se le da el color gris plateado abedul. El grupo propulsor se construye aparte y se unen en la línea de producción. En un vehículo normal se empezaría con cables y tubos, pero estamos fabricando el coche de James Bond, por lo que dedicaremos mucho tiempo a los distintos artilugios antes de colocar el motor, el salpicadero y los asientos.
¿Os parece mucho trabajo? Comparado con las horas dedicadas a un Bentley Mulsanne o un Rolls-Royce Phantom, ¿pensáis que se tarda más o menos? Pues se tarda mucho más, para fabricar un Aston Martin DB5 Goldfinger se necesitan unas 4.500 horas según su fabricante.
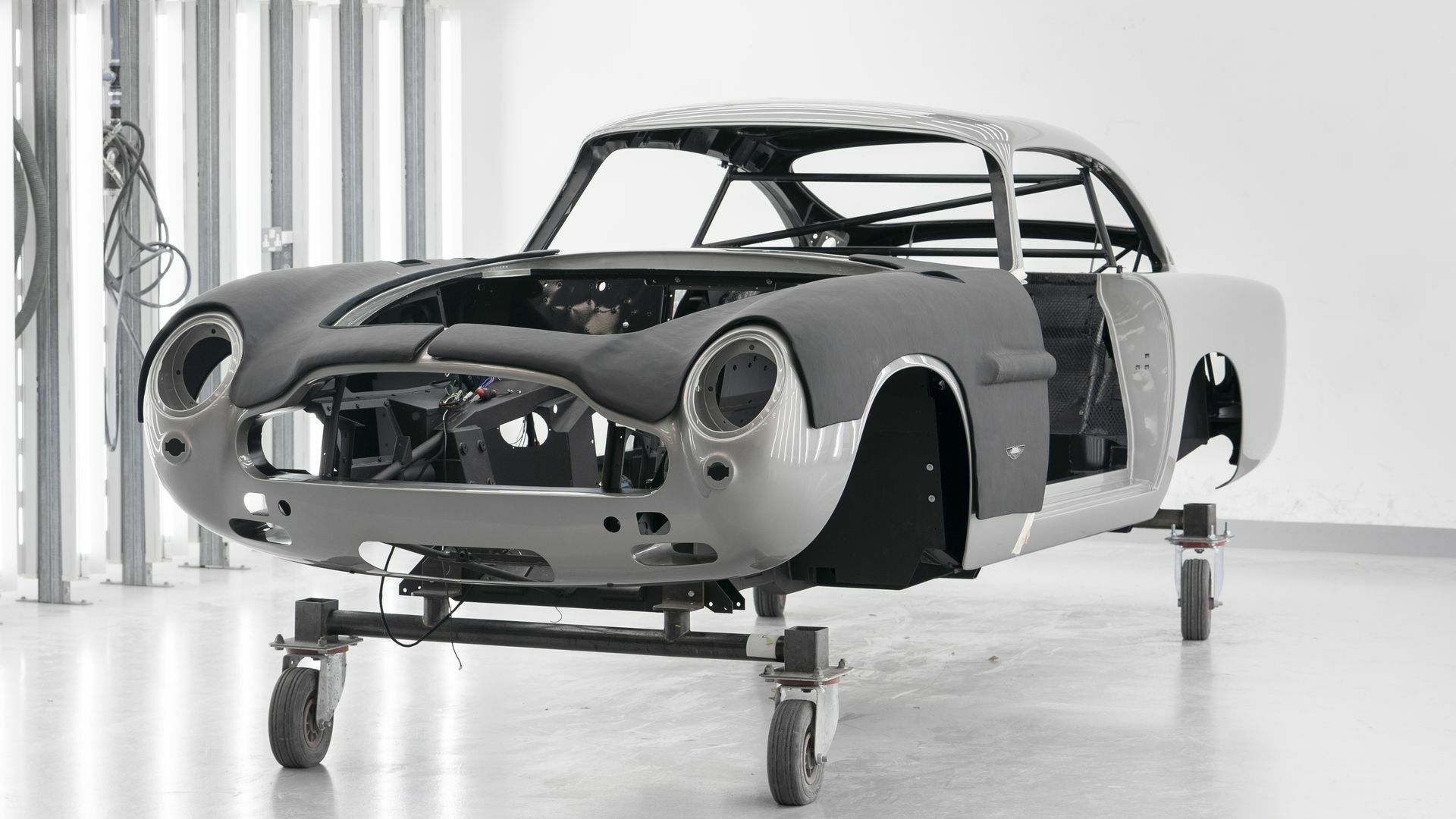
Comprendiendo esto ya no es de extrañar que adquirir uno salga por más de 3 millones de euros antes de impuestos. Parece caro, pero de los dos DB5 que se utilizaron para grabar las películas de Bond uno de ellos se quedaba en esa cantidad más o menos y el otro la duplicaba. Además del precio, otro hándicap de este modelo es que el fabricante avisa de que este modelo no está adaptado para su uso en carretera.
Si bien el DB5 era un automóvil homologado en 1963, las normas han cambiado mucho, tanto que el fabricante avisa de que la posible homologación dependerá del país donde se intente matricular. Los impedimentos para la homologación no son solo los gadgets incorporados, aunque sean falsos, la normativa anticolisión y antipolución tampoco permitirían homologar un automóvil a carburador con un chasis sin zonas de deformación programadas, barras anti intrusión en las puertas, airbag o ABS.
En España se puede intentar homologar como vehículo de colección o muy baja tirada, como si fuese histórico
Quizás es más fácil homologarlo como vehículo militar, tampoco creo que suponga mucho problema para los futuros propietarios. Quien esté dispuesto a pagar más de 3 millones de euros por un automóvil así, probablemente tenga una finca del tamaño de un condado o una isla privada. Puestos a soñar, ¿qué os apetece más, ser el propietario de un Valkyrie o de un DB5 Goldfinger? Yo no lo tengo nada claro, creo que me quedo con los dos.
Producción artesanal de Jaguar
Como os decía, el Reino Unido es un país muy importante para la industria automotriz de élite. No aparece en las listas de los grandes fabricantes en masa, pero sí en tiradas cortas. En el caso de Jaguar, pocas marcas han mantenido unido durante tanto tiempo el concepto de lujo y deportividad.
Nos saltamos la producción de los modelos actuales, pues es muy similar a lo que ya hemos visto, y saltamos a las series especiales. En 1963 se lanzó una producción de Jaguar E-Type Lightweight de 18 unidades, de los que solo se fabricaron 12. En 2014 se decidió completar esta serie con las seis unidades faltantes.
Para la fabricación de estos modelos se recurrió a las técnicas más avanzadas de ingeniería inversa. Esto es, en vez de generar un modelo nuevo, nos basamos en algo que ya existe y lo copiamos, modificando sus puntos débiles.
En ese caso se escaneó completamente un vehículo original número 12 para digitalizar todas sus cotas con un error menor al milímetro. De esta manera se obtuvo las medidas y se pudo deducir el proceso de montaje de las 230 piezas que forman la carrocería de aluminio de un Lightweight, por cierto, peso ligero. Se decidió fabricar con las mismas técnicas originales para poder homologar estas unidades en competiciones de vehículos de época de la FIA.
Aproximadamente el 75 % de los paneles de aluminio que forman la carrocería se han desarrollado en el mismo departamento que construye los prototipos de la casa. El resto de paneles son los de mayores dimensiones y fueron suministrados por empresas externas que los fabrican con utillajes diseñados por Jaguar.
Se construyeron más de 75.000 unidades del E-Type, por lo que hay un excelente mercado para las piezas para su mantenimiento y restauración.
La formación de la carrocería se realiza en varias instalaciones. En primer lugar el monocaso se construye en Whitley. Esta carrocería se fija a un bastidor tubular auxiliar, reforzados igual que la unidad número 12, que fue la escaneada. Esta unidad fue la última en ser fabricada y por lo tanto más evolucionada. Después de ser construida se trata y se pinta en Gaydon. Una vez pintada se lleva a un área exclusiva de Jaguar Heritage, en Browns Lane, muy cerca de se fabricaron los primeros Lightweight.
En esta última instalación se montan el motor, suspensión, frenos, dirección, componentes eléctricos, salpicadero y revestimiento suave. En esta ocasión el montaje es más sencillo, pues al ser una unidad de circuito carece del equipamiento habitual en turismos. Estas unidades no tienen aire acondicionado, moqueta o dirección asistida, pensad que es un automóvil diseñado en 1963.
Ahora bien, como se fabricaron en 2014, se aplicaron los controles de calidad de ese año para comprobar que todo es perfecto. Resulta cuanto menos chocante ver que las medidas de un vehículo realizado enteramente a mano se comprueban con un brazo articulado, con control totalmente digital. El precio de estas unidades no ha trascendido, esto es debido a que se ofrecieron las mismas antes de ser fabricadas a clientes seleccionados, o sea, que iban a decir que sí sin importarles su importe.
Tal ha sido el éxito de este modelo que se ha repetido con el XKSS de 1957. Este modelo tuvo su origen en el Jaguar D-Type, construido de 1954 a 1956 y ganador de Le Mans. El XKSS era la versión para carretera del deportivo y se construyeron 16 unidades. Hasta ahí todo bien, el problema surgió en que las nueve unidades reservadas para el mercado estadounidense ardieron en Brown’s Lane.
De nuevo se recuperan estos números de serie y se repiten los modelos buscando que sean exactos a la serie original, como si nunca se hubiera interrumpido su fabricación.
De nuevo el chasis original es escaneado para obtener las medidas correctas y es construido con el mismo material que el original, en este caso magnesio. Después de tantos años se ha perdido el modelo en el que se basaban los paneles, por lo que se ha vuelto a fabricar.
Todos los paneles se fabricaron a mano mediante una rueda manual, como la que hemos visto en Aston Martin. En este caso no hay un mercado de piezas de restauración que fabricara alguna de las piezas, por lo que hubo que fabricarlas todas a mano.
Eso para la parte exterior, el chasis está formado por una jaula de tubos de perfil tubular. Es una locura de 531 tubos en varias secciones, cortados a medida y soldados a soplete por el departamento de clásicos de Jaguar, para ser lo más fieles posible al original. El motor es también el mismo que el de 1957, al igual que todos los detalles del interior. Solo se han permitido unos cuantos cambios en las unidades para la mejora de la seguridad de sus ocupantes.
El precio de esta joya de 2016 fue de más de un millón de euros, el tiempo estimado para la fabricación de cada unidad supera a todo lo que hemos visto: 10.000 horas. Después de ver la recuperación de los clásicos, vamos a la tecnología de vanguardia, saltamos a Woking.
Línea de montaje McLaren
Woking (Surrey, Inglaterra) suena tanto a superdeportivo como a Fórmula 1. Sus instalaciones denominadas McLaren Technology Center están diseñadas por el famoso y acreditado arquitecto Norman Foster. Esta instalación es un edificio ocupa una forma circular y parte de ella es un estanque. Tanto su exposición como su sala de ensamblaje podrían utilizarse como museo para exponer cualquier obra de arte.
La sala de producción es totalmente blanca, diáfana y muy luminosa. Solo este complejo costó 40 millones de libras. Desde el primer McLaren de carretera, el F1 de 1992, todos los vehículos son elaborados en compuestos reforzados en fibra de carbono.
La manera de fabricarlos es similar a las que ya hemos visto. Se construye el monocasco y los paneles externos. Se pintan todos a la vez para que tengan el mismo tono. Por otro lado se construye el grupo propulsor, asientos, salpicadero y todas las demás piezas.
Cuando los paneles están listos son pintados en varias capas, en el caso de un McLaren P1 el tiempo de pintura de todos sus paneles es de tres días. La línea de producción arranca con el monocasco al que se le van añadiendo los componentes y el subchasis delantero. En McLaren no hay una línea de producción como tal, los chasis se colocan en carros que se van pasando de estación en estación.
Las estaciones en las que los técnicos deben trabajar en el inferior del chasis, tienen un elevador para facilitar el trabajo. Dependiendo del modelo, el trabajo en las estaciones es más o menos largo.
Como ejemplo, el proceso para la construcción de un P1 era de 17 días. Este modelo de serie limitada tenía 10 estaciones en la línea de ensamblaje. En cada una trabajaban dos técnicos una jornada completa, cuando en un automóvil de producción en masa ese tiempo es unos pocos minutos. Este trabajo se realizaba en una línea a parte del MP4-12C, que era el otro modelo que se fabricaba.
Después de colocar los dos subchasis se instala el salpicadero, interior y asientos. Después se une el grupo propulsor al chasis. Una vez que esta unión es firme y se han conectado todos los cables y tuberías se colocan los paragolpes.
Ya al final de la línea, se colocan los cristales y paneles externos. Cuando ya está montado, nuestro McLaren se chequea completamente, incluso se le hace una prueba con agua a presión para averiguar si es totalmente estanco. Por supuesto se hacen pruebas en movimiento, hay que estar muy seguro de que se puede llegar a los 400 km/h sin problemas.
Una vez que se le da el visto bueno técnicamente, el último paso es una inspección visual en un túnel iluminado para comprobar que también está perfecto estéticamente.
Todavía nos quedan unas cuantas fábricas más para visitar: Lotus, Morgan, TVR y Ariel entre otros. Siempre hay que dejarse algo por ver para tener una excusa y volver, por lo que hoy acabamos aquí.
En el próximo artículo acabaremos a nuestros superdeportivos que nos dejamos a mitad de la línea de producción, justo en el matrimonio, donde chasis y grupo propulsor son unidos.
En espíritu RACER | Cómo se fabrica un automóvil de serie limitada – Vuelve a leer la parte VII | Lee la parte IX
Este reportaje ha sido realizado gracias a las aportaciones de los miembros de nuestra comunidad a través de Patreon. Así podemos seguir realizando periodismo de motor de calidad sin depender de los ingresos publicitarios. Puedes ayudarnos a partir de 1 euro al mes.
J.J. López
Portador del contagioso virus de los coches desde los once años. Ingeniero en informática, programador de robots y visión artificial que lo piensa todo en coches. Amante del arte, técnica y tecnología en movimiento, esto es, apasionado incondicional del automóvil.COMENTARIOS