Con este artículo cerramos las producciones fuera de serie de dos de las marcas más exóticas del mercado, Lamborghini y Bugatti. Ambas pertenecen al grupo VAG y ambos fabrican superdeportivos con motores de combustión interna, hasta ahí los parecidos.
Los primeros modelos de Lamborghini eran GT al estilo de Ferrari, todo esto cambió con la aparición del Miura, primer turismo a la venta con motor central (poco antes apareció el Ferrari 250 LM, modelo de competición homologado para carretera). Este modelo revolucionó el mercado, pues era un automóvil muy rápido y muy potente, pero no pensado para competir. El modelo que le sucedió, el Countach, era todavía más rápido, más potente y más impactante por su forma. Este modelo funda un estilo en el que ha permanecido la marca pese a todos los cambios de propietarios.
Bugatti es una de las marcas pioneras de la industria automotriz en general y del lujo y deportividad en particular. Ettore Bugatti fue a la vez diseñador, ingeniero y empresario. Sus modelos son legendarios tanto por sus éxitos deportivos (el tipo 35 acumula unas 2.000 carreras ganadas tanto en circuito como en carretera) como por su lujo (el Bugatti Royale fue concebido para la realeza, uno de sus modelos no se le vendió al rey Zog de Albania por sus modales en la mesa, pese a que solo se vendieron tres de los seis fabricados cuando se pensaba vender 25).
Después de los éxitos de los años 30, Bugatti no pudo contra Alfa Romeo, Maserati y Mercedes en carretera y después de la Segunda Guerra Mundial la marca perdió toda su chispa. En 1947 falleció su fundador y la empresa no duró mucho más. En 1998 la empresa fue adquirida por el Grupo VAG para reflotarla después del paréntesis del EB110. Siguiendo una de las máximas de Ettore: “si es comparable, no es un Bugatti”. Ciertamante ni siquiera un Lamborghini es comparable a un Bugatti, ni en el grupo propulsor ni en el lujo.
En artículos anteriores hemos fabricado sus chasis y sus motores, ahora veremos cómo se terminan de fabricar estos vehículos.
Línea de producción de Lamborghini
En Sant’Agata Bolognese existen tres líneas de producción: la V12 inaugurada por el Miura, la V10 inaugurada por el Gallardo y la SUV inaugurada por el Urus, de esta última han salido más de 10.000 unidades.
Hemos hablado muy poco de los SUV, en esta serie nos hemos centrado en superdeportivos y limusinas de representación. Esto es, nos hemos centrado en automóviles que apenas sirven para una cosa, que es para ir muy rápido de la manera más elegante posible. De la línea del Urus destacamos que se ha incorporado la inteligencia artificial y los robot colaborativos. La inteligencia artificial se utiliza para mover las carrocerías. En la factoría del Urus no existe una línea de producción física.
Las carrocerías se mueven en vehículos autoguiados (AGV) que también podríamos llamarlos robots. Dada la cantidad de opciones de color y de acabados, no todas las carrocerías deben hacer los mismos movimientos. Aquí entra la IA que predice los movimientos de las mismas y se anticipa dando las órdenes adecuadas a los AGV basándose en los tiempos de procesos anteriores.
Por otro lado, los robots colaborativos son un tipo especial de robot que tiene sensores ultrasensibles y que detectan cualquier alteración imprevista de su trayectoria. En otras palabras, se detienen rápidamente si detectan un pequeño golpe, es fácil pararlos con la mano.
Un robot clásico necesita estar dentro de una zona protegida y si entra un operario debe pararse inmediatamente. Los robots clásicos se detienen en caso de colisión, pero podría ser fatal para un operario, pensad que un robot industrial puede manejar cargas desde unos 7 a 1.200 kg, los que podemos ver soldando manejan cargas en torno a 150 kg.
Nadie quiere saber cómo es una “caricia” de un robot que puede con 1.200 kg
Gracias a su sensibilidad, un robot colaborativo no necesita estar dentro de un entorno protegido, digamos que es inofensivo. Bueno, es inofensivo si la herramienta que porta también lo es, de nada sirve que nuestro robot sea colaborativo si maneja un cuchillo o piezas a 800 grados recién fundidas.
Si tan seguros son los robots colaborativos, ¿por qué no son todos así? En primer lugar no pueden manejar cargas elevadas, de momento hasta unos 20 kg, por lo que no sirven para todos los trabajos. En segundo lugar, no son tan rápidos como los clásicos.
Estos dos inconvenientes hacen que, por el momento, sean muy pocos los robots colaborativos que se encuentran en las plantas de fabricación. De nuevo ponemos como comparativa la planta de SEAT en Martorell, de los más de 2.000 robots que tienen en planta, a la fecha de la escritura de este artículo solo uno es colaborativo.
Los robots colaborativos empleados en la planta del Lamborghini Urus son tres. El primero de ellos se emplea en el matrimonio. Una vez unido el grupo propulsor al chasis, es necesaria su fijación con tornillos. Aquí es donde entra el robot colaborativo ayuda en el atornillado del grupo propulsor en el matrimonio.
A baja velocidad va apretando los tornillos para unir ambas partes. Este robot no va más rápido que un operario, las ventajas son que no se va a dejar ningún tornillo por apretar y los técnicos pueden trabajar a su lado.
El segundo de ellos es el que se encarga de encolar el parabrisas, con un visible color verde. Los operarios toman un parabrisas con ventosas y lo llevan al robot. Este se encarga de depositar la cantidad adecuada en el sitio adecuado. Este robot está sin protección y dado que el proceso es lento, es muy adecuado para el trabajo.
El tercer robot no tiene forma de brazo. Es un carro autoguiado que lleva las ruedas al operario. Las descarga de otro carro donde se encuentra el juego de cada Urus y las eleva para facilitar el trabajo al operario.
Sigamos con los cupés. Dejamos a nuestro Huracán en la línea de producción después de colocar el grupo propulsor. Después de eso se colocan todos los cables y tuberías. Se una vez que está todo el grupo acabado, se sigue con el interior.
Nos quedan los asientos, las puertas y los parabrisas. Una de las características que más llaman la atención de la línea de producción del Huracán es el colorido de sus modelos. No solo es que sean diferentes entre sí, si no que además son diferentes a los colores habituales. Es normal ver colores ácidos al lado de pastel y otros con acabado mate. Algo así ocurre con la piel del interior del vehículo.
Si queremos un Huracán morado con asientos fucsia solo debemos pedirlo; y si no existe ese color, tampoco debéis preocuparos, se crea. Como siempre, la línea de producción acaba en un túnel iluminado para comprobar que todo es perfecto.
Nada debe quedar al azar, la unidad debe ser probada para certificar que su motor es perfecto. Primero se hace una prueba en la penúltima estación, más tarde se hará una prueba en carretera abierta para saber que todo está como debe ser. Después de esa prueba, túnel de luz para comprobar que todo es perfecto.
La línea que nos falta ver es la de V12, donde se fabrica el Aventador y otras series limitadas, como el Lamborghini Sián. Es una serie limitada basada en el Aventador al que se mejora su grupo propulsor perfeccionando el motor de combustión y añadiéndole supercondesadores para hibridarlo, haciendo el Lamborghini de calle más rápido y más potente.
Estos supercondensadores son de carga y descarga rápida y están desarrollados en conjunto con la sede italiana del Instituto de Tecnología de Massachusetts (MIT-Italia). Estos supercondesadores hacen de batería para el motor eléctrico que tiene acoplado en la caja de cambios.
Es la primera vez que se aplica esta tecnología en un automóvil de calle y de momento solo proporciona 34 CV de potencia extra. El propósito de utilizar este tipo de almacén de energía eléctrica es que puede llegar a almacenar el triple de energía por unidad de peso que una batería de ión litio. Además, la energía absorbida y emitida es prácticamente la misma, por lo que también es más eficaz.
Por el momento se obtienen 34 CV con 34 kg de masa en baterías, pero se espera que sea el doble de potencia en próximas versiones para el mismo peso. El grupo de baterías se encuentra a mitad del habitáculo, justo detrás de los asientos.
Esta serie limitada de 63 unidades no solo presume de tecnología, se espera que todas las unidades sean personalizadas y todas sean diferentes. Como ejemplo de cómo puede ser personalizada cada unidad, la presentada en el Salón de Frankfurt de 2019 tenía la pintura dorada. Más que dorada, de oro, la pintura contenía copos y cristales de este metal. Este mismo mes se ha presentado el Sián Roadster, versión descapotada de este modelo, con la misma tecnología y solo 19 unidades a unos 2 millones de euros.
Lo siento mucho si os gusta y queréis uno, ya están todos vendidos
Volviendo a la línea de producción, la línea tiene muy pocas estaciones y cada parada dura más de 40 minutos. Los técnicos son especialistas de toda la línea no solo de un puesto, cada tres meses cambian de estación para conocerlas todas.
Al trabajar en todos los puesto del ensamblado, los técnicos interpretan mejor si ha habido un fallo en la estación anterior, pueden ayudar a corregirlo y evitan fallos que puedan ser problemáticos en la estación siguiente.
Cada punto que se encuentra es marcado con cinta azul, pero no penséis que los Lamborghini tienen muchos fallos en su producción. La gran mayoría de esos puntos marcan fallos que son imperceptibles a ojos de alguien no entrenado.
Poco a poco se va completando el automóvil con la mecánica, fluidos e interior. No debemos perder de vista que además de tener un motor muy avanzado y complejo, y un control de la tracción muy elaborado, los V12 de Lamborghini son altamente configurables.
Esto hace que su construcción también sea compleja, por la gran cantidad de opciones disponibles. Sea cuales sea las opciones elegidas, después de montar el automóvil se prueba en carretera abierta y a la vuelta se comprueba que todo está bien en el túnel de luz. Recogemos nuestro cupé, nos despedimos de Sant’Agata y tomamos rumbo a Francia.
Línea de montaje de Bugatti
Regresamos a Molsheim, para ver cómo se acaba de construir nuestro hiperdeportivo franco-alemán. Dejamos a nuestra joya unida, recordad que el matrimonio de este cupé se realiza por la unión en horizontal del subchasis trasero con el habitáculo.
Recordamos que la línea de montaje parece más un laboratorio que un taller. En él unos 20 operarios revisan una por una las 1.800 piezas de las que consta un Chiron. Después son montadas totalmente a mano y son unidas por 3.800 tornillos.
Después del matrimonio, con veinte tornillos se unen las cuatro ruedas a los bujes y se envía la carrocería, ya automóvil, a la siguiente estación, la de fluidos.
En esta estación se rellenan todos los fluidos: aceite de motor y transmisión, líquido de frenos, aceite para los circuitos hidráulicos y refrigerante. El refrigerante se rellena y se hace vacío en el circuito para comprobar que no hay ninguna fuga. Un motor de combustión cuando eroga 1.500 CV de potencia emite casi un millón de kilocalorías por hora, por lo que es muy importante su refrigeración.
En el montaje del motor se giró en vacío para comprobar que todo iba bien, en esta misma estación es donde se arranca esta bestia por vez primera, un momento siempre delicado. El siguiente paso es comprobar que todo el conjunto funciona bien, para ello se utiliza un banco de potencia adaptado a los 1.500 CV. Este banco de potencia puede generar hasta 1.200 amperios de electricidad. El exceso producido es volcado a la red eléctrica local.
Para probar el grupo propulsor de un Chiron se dispone de una sala acondicionada donde el automóvil está refrigerado y su ambiente controlado para no contaminar. El motor será probado a toda potencia y hasta un equivalente de 200 km/h. El automóvil es fijado para evitar que se mueva y genere un accidente durante las pruebas.
Un miembro del equipo está detrás del volante durante toda la prueba y comprueba, entre otras cosas: la configuración del motor, comunicación entre motor y transmisión, ajuste del caudalímetro, embrague, ESC, ABS y otros programas. La prueba dura entre dos y tres horas y el automóvil recorre un equivalente a 60 km.
Solo cuando estamos seguros de que el motor funciona perfectamente lo llevamos a la siguiente estación, donde se colocan los paneles exteriores que fueron pintados con tanto mimo. El paso siguiente después de que todo esté colocado es una prueba del monzón durante media hora. Si no ha habido ninguna pérdida de agua en el habitáculo, pasamos a colocar el interior. Dos técnicos se encargan de ello durante unos tres días. Ahora que está todo acabado queda la prueba completa.
Antes de sacar un Chiron a la carretera se cubre totalmente con plástico para evitar que se dañe. Se emplea un día solo con este recubrimiento. Por cierto, el fondo plano y las ruedas todavía no son las definitivas, se colocarán después de la prueba en carretera.
La prueba de un Chiron consiste en conducirlo unos 300 km y llevarlo a más de 250 km/h en el aeropuerto de Colmar. El viaje de regreso se realiza por la Autobahn algo más relajados para que el motor se pueda enfriar. Si el probador da su visto bueno, todos los aceites son reemplazados, se coloca su fondo plano y las ruedas finales. De nuevo se realiza una prueba para comprobar que todo está bien; esta vez es corta, de unos 50 km.
De nuevo, si se supera este otro hito, pasamos a la fase siguiente, que son los retoques. El automóvil se lleva de nuevo al taller de pintura, donde se le quitará la hoja protectora, se limpia y se pule. Para realizar esto se emplean otros dos días, después de los cuales se lleva al túnel de luz.
En dicho túnel se verifica todo durante unas 6 horas. Si todo es perfecto ya se puede entregar, si hay algún fallo que retocar se devuelve a la sección de pintura. Si se debe hacer un retoque se puede tardar de tres horas a tres semanas. Tres horas si solo hay que pulir alguna parte y tres semanas si hay que repetir una pieza personalizada.
De nuevo se devuelve al túnel de luz para comprobar que todo es perfecto. Si es así, se da aviso al director Chritophe Piochon que se reúne con los jefes de ventas, Calidad y Servicio al Cliente que revisan de nuevo el estado del automóvil; solo si están satisfechos, el Chiron será entregado a su cliente final.
El tiempo total de construcción de un Bugatti Chiron es de seis meses, solamente el montaje son dos meses. Como hemos dicho varias veces, el tiempo aquí es muy relativo, lo importante es que el producto sea único e incomparable. Ahora que ya somos expertos en cómo se fabrican las joyas de Alsacia, salimos de Molsheim de vuelta a casa.
En esta serie hemos visto cómo se construyen los superdeportivos y otros vehículos de muy baja tirada. Hemos visto marcas clásicas y marcas modernas, vehículos rápidos, muy rápidos y los más rápidos de todos. Hemos visto cómo se construyen las berlinas más lujosas del mundo, que también son de las más rápidas. También hemos visto que el lujo puede pasar de los 300 km/h con mucha facilidad.
También hemos visto que el mercado ha acabado dándole la razón a Ettore Bugatti cuando dijo que no hay nada demasiado bello ni demasiado caro.
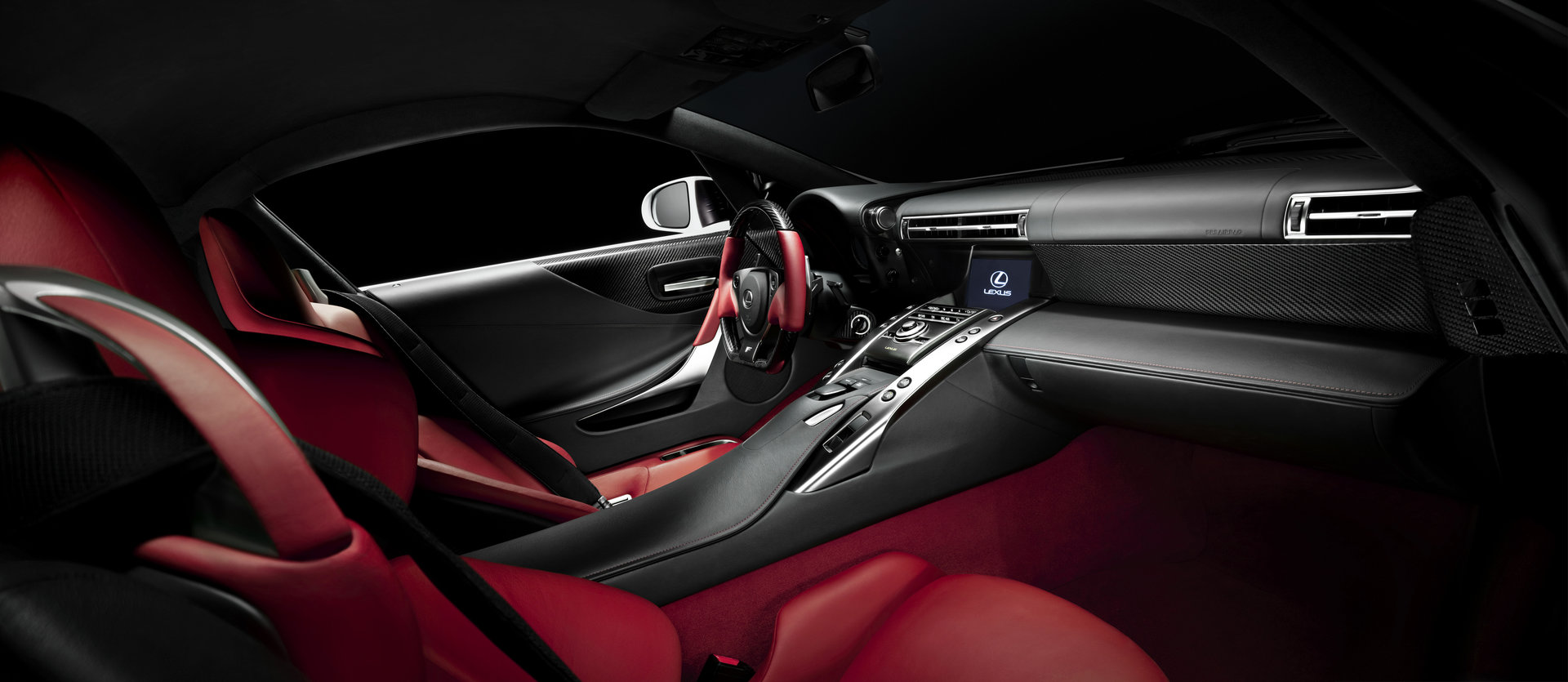
Nos queda un artículo más de esta serie donde hablaremos de cómo se fabrican los automóviles exclusivos en Estados Unidos y en Japón.
En espíritu RACER | Cómo se fabrica un automóvil de serie limitada – Vuelve a leer la parte IX | Lee la parte XI
Este reportaje ha sido realizado gracias a las aportaciones de los miembros de nuestra comunidad a través de Patreon. Así podemos seguir realizando periodismo de motor de calidad sin depender de los ingresos publicitarios. Puedes ayudarnos a partir de 1 euro al mes.
J.J. López
Portador del contagioso virus de los coches desde los once años. Ingeniero en informática, programador de robots y visión artificial que lo piensa todo en coches. Amante del arte, técnica y tecnología en movimiento, esto es, apasionado incondicional del automóvil.COMENTARIOS