Seguimos con la construcción del automóvil de nuestros sueños. Ha sido diseñado, hemos construido su chasis en fibra de carbono, aluminio o mixto, lo hemos pintado y hemos construido su grupo propulsor. Ahora los vamos a unir. De nuevo encontramos clases entre el superlujo, pues hay una gran diferencia entre producción en serie y serie limitada.
Un Porsche 911 es un automóvil de serie, aunque de serie muy corta y un Porsche 918 es un serie limitada. La diferencia es que se fabrican tantos 911 como se pidan y el 918 se fabricaron 918 unidades, ni una más. El Porche 911 se fabrica de una manera muy similar a un automóvil de producción en masa y un 918 se fabrica artesanalmente, unidad por unidad y todo a mano las unidades comprometidas. Después de eso ya no hay más, no importa el dinero que estemos dispuestos a pagar.
Vayamos a la planta de Stuttgart-Zuffenhausen y observaremos más detenidamente las diferencias.
Línea de producción del Porsche 911
Retomando los pasos anteriores de la producción hemos construido el chasis, lo hemos tratado y lo hemos pintado. Por otro lado hemos construido el motor, la caja de cambios y los hemos unido a la transmisión y suspensiones. El primer paso de la línea de producción se desmonta la carrocería. ¿Por qué primero se monta todo y luego se desmonta? Se monta todo para pintarlo todo junto para que el tono de pintura sea uniforme. Al inicio de la línea se desmontan las puertas.
Estas puertas se llevan a otra línea más pequeña en la que se colocan en paralelo los guarnecidos y todos sus elementos, como elevalunas, cierres, altavoces y demás. También añadimos a la carrocería unos protectores a los paneles laterales para que no sean rayados durante los procesos. Estos primeros pasos la carrocería está sobre un banco que puede ser elevado para facilitar el trabajo a los técnicos.
Pasamos de estación y ahora sí comenzamos a añadir componentes por el interior del habitáculo, comenzando por la instalación eléctrica y los cinturones de seguridad. Es el momento de pasar los mazos de cables de la preinstalación eléctrica por los huecos previstos. Una vez que están listos todos los mazos de cables se le colocan las lunas frontal y trasera.
En un vehículo de producción en masa sería colocado por un robot, que toma el parabrisas, lo lleva al dispensador de cola para colocar sobre su borde y lo coloca después de haber medido la posición exacta del automóvil. En el caso del Porsche 911 no sale rentable que un robot coloque sus cristales. Los cristales son colocados por dos operarios, que utilizan un manipulador con ventosas. Con este manipulador toman con ventosas al vacío al parabrisas ya encolado y lo colocan en su sitio.
La cola es de curado lento para poder rectificar la posición si no está el parabrisas en su sitio. Los operarios disponen de galgas graduadas para asegurarse de que el parabrisas está perfecto. En estaciones siguientes se colocan los faros, guarnecidos del maletero y aquellos elementos mecánicos que no van en el vano del motor, como los radiadores delanteros y las tuberías de los líquidos.
También se utiliza este momento para colocar el salpicadero, que es mucho más fác,il ahora que no hay puertas ni otros elementos que entorpezcan el trabajo. Otra de las piezas que se colocan en esta parte del montaje es el escudo de Porsche sobre su capó. Ahora sí, nuestra carrocería está lista para el matrimonio, por lo que sacaremos nuestra carrocería del sistema de carros bajos.
Después de esto llevamos la carrocería a un elevador, que la tomará y la llevará en alto desde ahora. Este elevador además permite voltear longitudinalmente la carrocería, de manera que el operario pueda trabajar en la parte baja del vehículo en una postura cómoda. Desde otra parte de la línea habíamos introducido el grupo propulsor formado por el motor, la caja de cambios, transmisiones y suspensiones.
Todos estos elementos vienen en un carro autoguiado que se coloca debajo de nuestra carrocería; por fin llega el momento de la unión
La carrocería se descuelga hasta unirse al grupo propulsor. Se baja poco a poco, para que los técnicos puedan comprobar que todo llega a su sitio. Cuando está todo en su sitio se atornillan todos los anclajes: amortiguadores, motor, suspensiones, etc.
También se unen las conducciones de los líquidos, prinpalmente de frenos, radiadores, servodirección y gasolina. Y dejamos a nuestro Porsche 911 por hoy, de nuevo como ejemplo de automóvil de baja serie. Vamos a comprobarlo con su hermano más exclusivo Porsche 918, que es un serie limitada.
Línea de producción del Porsche 918
La primera diferencia que vemos es que la fábrica es más estética. La zona de fabricación del 918 se ubicaba en la planta 2 de Zuffenhausen, en la zona de pinturas especiales. Para darle prestancia y comodidad a los operarios, se pintó de gris y blanco con detalles en verde ácido por ser el color que emplea Porsche para identificar a sus vehículos híbridos.
Tampoco hay una línea que porta las carrocerías, en este caso son vehículos autoguiados que se van moviendo de estación a estación. Estos vehículos son totalmente autónomos, de manera que no hay ningún cable de por medio. Para facilitar el trabajo a los operarios, estos carros tienen un elevador por tijeras para colocar la carrocería en la posición deseada, además de poder ser volteada tanto de manera horizontal como vertical.
La historia del montaje de un 918 comienza con el monocasco de fibra de carbono en la primera estación, de un total de 18 en una línea que forma una “L”. Por la parte izquierda vendrán las piezas premontadas para colocar en nuestro biplaza.
La pieza más importante es el grupo propulsor. El grupo comienza con el motor de combustión interna, que es un V8 con unos 140 kg de peso, que previamente a montado un solo técnico en 20 horas siguiendo la norma de “un hombre, un motor”. Una vez colocado el motor, se le añade la caja de velocidades, el conjunto de la transmisión y el motor eléctrico.
Todo el equipo eléctrico viene totalmente descargado para eliminar el riesgo de electrocución a los técnicos. Ahora sí tenemos el grupo preparado para el matrimonio. Para unir el grupo propulsor al monocasco se utiliza un carro con un elevador especial que alinea ambas partes. Una vez alineadas, se unen mediante tornillos. ¿Cuántos tornillos pensáis que son necesarios para unir a un habitáculo un grupo propulsor de 887 CV capaz de llegar a 200 km/h en menos de 6 segundos?
Suena increíble, pero el grupo propulsor del Porsche 918 es unido al chasis con solo seis tornillos. Ahora bien, para asegurar que todos los tornillos son apretados correctamente, los técnicos de Porsche utilizan unos atornilladores inalámbricos dinamométricos con Bluetooth.
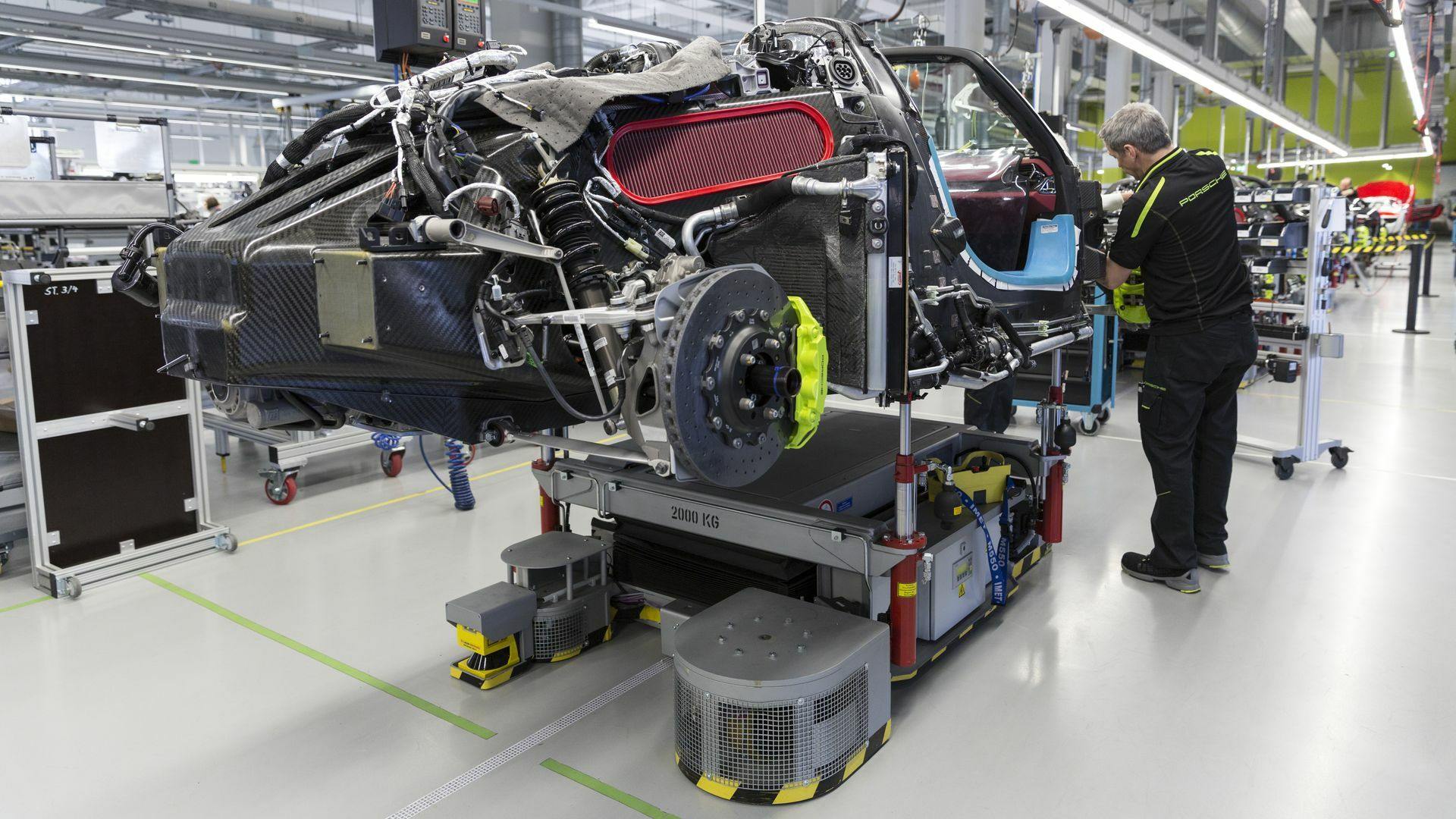
Con estas herramientas conseguimos varias cosas. En primer lugar no están conectados a cables o tubos, por lo que son más fáciles de usar. Llevan el sensor dinamométrico incorporado, por lo que apretaremos todos los tornillos con el par adecuado.
Por ser Bluetooth conseguimos dos cosas; en primer lugar, transferimos de manera inalámbrica el par de apriete correcto. En segundo lugar, el par final queda grabado, de manera que podemos recurrir a él si surge algún problema con una unidad o si queremos volver a apretarlo igual si ha habido un cambio de piezas.
Dejamos la fábrica de Porsche con nuestros cupés a mitad de montaje y nos dirigimos al sur.
Línea de producción de Bugatti Chiron
Vamos a Molsheim, a ver cómo se fabrica la joya de la corona del grupo VAG. Si impresionan los casi 900 caballos del 918, ahora construiremos un vehículo que eroga 1.500. Ettore Bugatti decía que “si es comparable no es Bugatti”, por lo que veremos varios procesos sin igual en el montaje del Chiron.
La línea de montaje se encuentra muy cerca del castillo de la marca, en un edificio nuevo con la misma forma ovalada de su logotipo. Este edificio está rodeado de cristaleras de manera que entra la luz natural desde todas partes. El interior por su parte es blanco con suelo epoxy pulido y le da más aspecto de laboratorio que de taller.
Esta vez disponemos de 12 estaciones y ningún robot, todo está elaborado a mano por tres operarios en cada una de las estaciones. Antes de la comenzar con el ensamblado, se deben construir el motor y la caja de cambios. Para ello se acaba de montar el propulsor que viene preensamblado. Una vez construido, es probado en un banco durante 8 horas. A la vez que se prepara el motor, la caja de velocidades sigue un proceso similar.
En la segunda estación se acomodan tanto el motor como la caja de velocidades a su subchasis de aluminio y carbono. Esto se realiza sobre una plataforma especial, de la que solo hay dos en la planta. No perdamos el punto de vista de que estamos construyendo un fuera de serie. Esta plataforma de montaje de chasis no se va a ir a diferentes pasos, todo el montaje se realizará en el mismo sitio. Además, este proceso dura una semana, aquí el tiempo es muy relativo.
Por otro lado, el subchasis delantero se acopla al monocasco de fibra de carbono. Una vez acoplado, se añaden los mazos de cables y los circuitos de líquidos. Si la refrigeración es esencial para cualquier automóvil, en un Chiron lo es mucho más. Es tanto el calor que puede generar su motor que su circuito de refrigeración dispone de tres bombas de agua. La principal bomba, la del bloque del motor, tiene un tamaño y caudal similares a la bomba que podemos encontrar en un camión de bomberos.
Como en el caso del Porsche 918, se utiliza un atornillador inalámbrico Bluetooth dinamométrico para atornillar. De los más de 1.800 tornillos que contiene un Bugatti Chiron, 1.068 son supervisados por esta herramienta y grabado su resultado en el sistema informático.
Cuando están el monocasco y el sector frontal unidos y el motor en su subchasis, se le da paso al matrimonio. De nuevo tenemos características muy diferentes con la construcción en serie. En primer lugar el matrimonio es horizontal, no introducimos el motor en la carrocería, si no que está en la mitad trasera.
En segundo lugar, el taller de Bugatti (atelier) carece de robots y de cintas transportadoras, por lo que las dos partes de un Bugatti Chiron son unidas gracias a la fuerza de los técnicos. Esta bella imagen atestigua esta unión en la que la fuerza humana une las dos partes de uno de los vehículos más potentes del mundo.
Las dos mitades unidas se fijan con catorce tornillos de titanio que solo pesan 34 gramos cada uno. Vuelve a sorprender que una bestia de 1.500 CV sea contenida con tan poco material
Después del matrimonio se unen el resto de elementos, como tubos y cableado. Una de las opciones que podemos pedir en un Bugatti es participar en su fabricación. Si podéis compraros uno de ellos podéis estar hasta un día colaborando con los técnicos para construir a vuestra joya alsaciana. Le colocamos una funda por encima y dejamos a nuestro Bugatti hasta que volvamos a Molsheim.
Línea de producción de Ferrari
Cruzamos los Alpes para volver a Italia. De nuevo vemos que hay grandes diferencias entre sus líneas de producción de modelos serie (aunque corta) a los serie limitada. Veamos más detalles del segundo grupo.
En 2013 se presentó el Ferrari LaFerrari en una serie limitada de 499 unidades. Todas estas unidades ya estaban vendidas antes de su presentación. Pese a costar 1,5 millones de euros, 200 personas se quedaron sin su LaFerrari, aunque sí disponían del dinero. ¿Por qué Ferrari no produjo todas esas unidades de más si podría embolsar más dinero con la misma inversión?
En estas empresas es muy importante conservar el nivel de exclusividad para que el producto siga siendo deseado. Recurrimos a otra cita de Enzo Ferrari referida a la fabricación. Siempre decía que la cantidad ideal de fabricación es una menos de las que se pueden vender. Muy probablemente en Ferrari pensaban que iban a vender 500 unidades de su LaFerrari y por eso fabricaron 499.
Para mantener la exclusividad de sus modelos de serie limitada, una de las condiciones para la adquisición de los fuera de serie de Ferrari es no venderlo antes de dos años. Por ejemplo, la primera unidad de LaFerrari a la venta de segunda mano duplicó el precio de venta como nuevo, las lógica habitual no se aplica al mercado de superlujo.
En la actualidad no hay una producción de vehículos en serie limitada al estilo de LaFerrari, en su lugar existe el proyecto Icona. Este proyecto retoma la inspiración de vehículos icónicos de la casa y los fabrica con la tecnología actual. En este caso toma la idea de los speedster Monza y utiliza la tecnología del 812 Superfast. Además de estos modelos también se fabrican algunos one-off al año.
Volvamos a la fábrica. Para la construcción de sus modelos, Ferrari dispone de tres líneas repartidas en dos plantas del mismo complejo. En la planta baja se fabrican los modelos V8, en la planta alta los V12 y series especiales. Las líneas V8 y V12 son similares a algunas que hemos visto. Se montan los motores y transmisiones a la vez que se construyen los chasis. Se desmantelan las puertas y se llevan a una línea paralela.
El chasis se coloca en un soporte aéreo que lo llevará por toda la planta y se puede girar para trabajar cómodamente en su parte baja. Como estamos construyendo automóviles de lujo tenemos una gran cantidad de opciones a tener en cuenta. A pesar de la baja producción de la marca (en 2019 batió todos sus récords produciendo poco más de 10.000 unidades sumando todos sus modelos) el número de referencias es muy elevado.
Para todos sus modelos, Ferrari utiliza 40.000 referencias de unos 750 proveedores. ¿Pensáis que es mucho o que no es para tanto? Por comparar, SEAT afirma que un modelo de automóvil utiliza unas 4.000 piezas de un centenar de proveedores. Vemos que sí, que construir un superdeportivo de lujo es algo complejo.
Para simplificar el trabajo a los operarios, a cada unidad se le asigna un carro con todos los componentes que ha elegido su propietario (sistema poka-yoke). Este carro sigue a la carrocería durante todo su trayecto dentro de la fábrica. Después de colocar los mazos de cableado, elementos de seguridad, tuberías y salpicadero se pasa a la estación donde se une al grupo propulsor. Este grupo viene en un carro que se coloca justo debajo de la carrocería a motorizar y se eleva hasta ponerlos a nivel.
Una vez unidos el motor y transmisión con la carrocería se unen firmemente. Esta manera de unir en vertical es común a las carrocerías de aluminio que están abiertas por debajo. Cuando Ferrari los fabrica en fibra de carbono el proceso se realiza en la tercera línea. Dejamos por un momento nuestros cupés para ver cómo lo hace la competencia.
Línea de producción de Lamborghini
Volvemos a la pequeña población cercana de Sant’Agata Bolognese, en la que veremos las diferentes maneras de fabricar. Iremos de la más reciente a la más clásica. La más reciente es la planta creada para fabricar el Urus. Una fábrica muy moderna donde se emplea la inteligencia artifical por primera vez en la construcción de automóviles.
La siguiente en modernidad es la línea para los V10, creada para el Gallardo. En ella se fabrica el Huracán actualmente. Recordamos que su carrocería está construida en aluminio con la parte central en fibra de carbono, al igual que su primo, el Audi R8 2020. Al igual que el resto de los vehículos que hemos visto se construyen carrocería y grupo propulsor por separado.
La carrocería entra en la línea de producción y se le colocan cableado, tubos, elementos de seguridad, parabrisas y salpicadero. El matrimonio aquí también es particular. En vez de subir el grupo propulsor a la carrocería, lo que se hace es bajar el motor y colocarla en el vano correspondiente. De nuevo se une el grupo propulsor a la carrocería para continuar con el montaje. Nosotros nos vamos a una pequeña línea que hay al lado, la línea de montaje V12.
Esta línea está desde el inicio, pues se creó para el Miura, desde ese modelo todos los V12 de la casa se han fabricado aquí. Apenas hay siete estaciones y la empresa presume de que el único robot que tienen para los V12 es un manipulador que gira la carrocería 90 grados para que el operario trabaje cómodamente. El proceso de montaje en cada parada es de unos 40 minutos. Los operarios cambian de estación cada tres meses para adquirir los conocimientos del montaje del vehículo completo. De esta manera pueden identificar y corregir posibles fallos de otros operarios.
De nuevo se construye el chasis y motor por separado y la carrocería se completa con cableado, tuberías, radiadores, salpicadero y parabrisas. El matrimonio del Aventador es de los más complejos del mercado. Esta carrocería de carbono está totalmente cerrada por debajo para crear un plano aerodinámico para que genere efecto suelo.
Por otro lado, el grupo propulsor es tan grande que no se puede colocar en vertical, pues la caja de velocidades queda a mitad de habitáculo. La solución es introducir el bloque propulsor en ángulo y poniéndolo en horizontal progresivamente en una maniobra muy compleja. Una vez colocado, se ancla el propulsor y continuamos con el ensamblaje; lo dejamos para otro día. Nos vamos al norte de Japón.
Fabricación del KODE57
Al principio de esta serie hablamos de series muy limitadas, quizás de una unidad. Hoy vamos a ver una producida en Japón por Ken Okuyama. Ken es el diseñador entre otros del Ferrari Enzo Ferrari, Maserati Quattroporte, Ferrari Rossa y Maserati Birdcage 75th. Ha montado su propia empresa de diseño y construcción de automóviles fuera de serie.
Este modelo está inspirado en el Ferrari 250 TR de 1957 fabricado por Scaglietti. Tiene el motor delantero, un morro largo, trasera muy corta, carece de techo, el parabrisas es muy bajo y los pasos de las ruedas están abiertos. El chasis tiene forma de caja y está fabricado en aluminio y fibra de carbono.
Ken no nos cuenta qué grupo propulsor utilizó para su vehículo, pero se piensa que es el de un Ferrari 599 GTB. Dada la baja tirada, no existe nada parecido a una línea de producción. La fabricación es totalmente artesanal. Esta planta tiene más de taller de chapista o de astillero que de fabricación de automóviles.
Cuando uno sabe que va a producir un gran número de unidades (a veces 100 unidades son muchas) se puede invertir en herramientas que nos ayudan a fabricar más rápidamente que a mano con la calidad adecuada. Cuando fabricamos una unidad o dos no es posible, comencemos a montar nuestro KODE57.
En primer lugar construimos el chasis y le colocamos el grupo propulsor. Como el chasis es independiente y abierto podemos construirlo completamente antes de colocarle los paneles externos. El interior es de fibra de carbono, también se añade a mano y se ajusta a base de lima y paciencia. Ya sabéis que el compuesto reforzado de fibra de carbono no admite ajuste una vez seco, o se hace bien a la primera o ya no se puede corregir.
Pensad que esta es la primera unidad, todo debería ir bien a la primera, pero casi nada lo hace. A veces es un soporte fuera de sitio, una puerta que no cierra bien o una pieza que no se encuentra. Algo así ocurre con los paneles, primero se fabrican, luego se ajustan a la carrocería y más tarde se pintan del color deseado. Una vez pintado se colocan a la carrocería.
El resultado final de este automóvil no transfiere la cantidad de trabajo que hay detrás, como el resto de joyas que hemos visto hoy. En el artículo siguiente nos iremos al Reino Unido, un país con una gran tradición en vehículos fuera de serie.
En espíritu RACER | Cómo se fabrica un automóvil de serie limitada – Vuelve a leer la parte V | Lee la parte VII
Este reportaje ha sido realizado gracias a las aportaciones de los miembros de nuestra comunidad a través de Patreon. Así podemos seguir realizando periodismo de motor de calidad sin depender de los ingresos publicitarios. Puedes ayudarnos a partir de 1 euro al mes.
J.J. López
Portador del contagioso virus de los coches desde los once años. Ingeniero en informática, programador de robots y visión artificial que lo piensa todo en coches. Amante del arte, técnica y tecnología en movimiento, esto es, apasionado incondicional del automóvil.COMENTARIOS