Si hay un material que se identifica con lo novedoso, deportivo y exclusivo, sin duda es la fibra de carbono. Sabemos que se utiliza, sobre todo, en los vehículos de altas prestaciones, pero ¿por qué? ¿Hay más de un tipo? ¿Se puede utilizar para cualquier componente? ¿Será un material muy utilizado en el futuro? ¿Se puede reciclar? Vamos a analizar estas preguntas con ejemplos tomados de la producción de vehículos.
Para empezar, denominamos al todo por una de sus partes. Decimos fibra de carbono cuando queremos decir compuesto de fibra de carbono. Para diferenciar el producto compuesto de su materia prima, les llamaré fibra de carbono y fibras de carbono, respectivamente.
La primera vez que se utilizaron las fibras de carbono fue en 1879 para realizar filamentos para bombillas incandescentes, Edison carbonizó fibras de algodón y de bambú para obtenerlas. El propósito de esas fibras era el de soportar las altas temperaturas de la corriente eléctrica a su paso, pero nada relacionado con las propiedades mecánicas. Las fibras de carbono sintéticas fueron descubiertas por Roger Bacon en 1958, mientras experimentaba con carbón para obtener su punto triple, que es cuando puede coexistir el carbón en estado sólido, líquido y gaseoso. Después de muchos experimentos, aparecieron unas finas estalagmitas de carbono. Comprobó después que, si bien se presentaron en forma de hilos, realmente se comportaban como si fueran cristales de carbono alineados. Ya se observó que eran muy duras, elásticas y resistentes, aunque no eran prácticas para la producción, pues su precio era desorbitado.
Al descubrirse sus características, se siguió investigando para producir las fibras de carbono de la manera más económica y perfecta posible. El proceso más usual que se sigue hoy en día -inventado a principios de los 60- es basándose en el acrinolito, como ya indicó Pablo Mayo en un artículo sobre la plataforma para eléctricos Audi-Porsche. Con este proceso se obtienen fibras con un 93-95 % de carbono en las fibras. Pasamos a explicar de forma muy resumida el proceso de obtención de fibras y de la fabricación de los compuestos.
Producción de las fibras
La producción de las fibras de carbono es muy costosa. Consta de hasta cuatro pasos básicos:
- Polimerización del acrinolito en poliacrinolito, pasa de un monómero a un polímero en forma de filamentos
- Oxidación de las fibras, de 180 ºC a 300 ºC, estabilización de las fibras
- Carbonización, de 300 ºC a 1.700 ºC, eliminamos el hidrógeno
- Grafitización, de 1.500 ºC a 2.800 ºC, se elimina el nitrógeno y se forman planos de grafito. Si se carboniza de 1.500 ºC a 2.000 ºC, producimos fibras con una resistencia a la rotura más alta. Si se carboniza de 2.500 ºC a 3.000 ºC, producimos fibras muy elásticas
En este proceso, hemos pasado de fibras frágiles y altamente inflamables con las que nos podríamos hacer un jersey acrílico, a fibras robustas, que prácticamente lo aguantan todo. Después de esto, las fibras se agrupan y se enrollan en bobinas. Lo más habitual es fabricar un tejido con ellas, aunque también se pueden utilizar directamente para fabricar cuerpos de revolución de manera automática. Los tejidos pueden ser unidireccionales, bidireccionales -los más habituales-, tridireccionales y hasta cuatridireccionales, dependiendo de la cantidad de direcciones de las hebras en el tejido. Se utilizan unas u otras para que el producto final sea muy rígido en un sentido y elástico en otro o lo más rígido posible en todos. Estos tejidos pueden ser impregnados en resina para facilitar la elaboración del compuesto, como veremos más adelante.
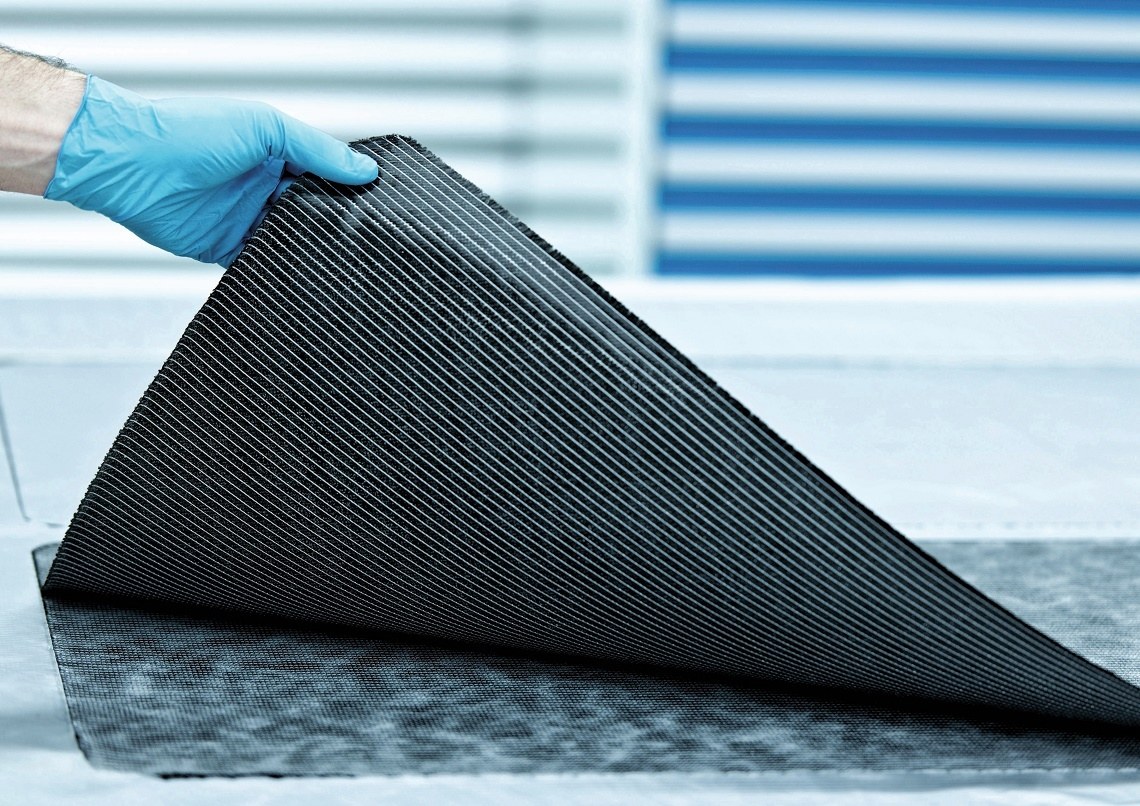
Materiales compuestos, donde 1+1 > 2
El origen de los materiales compuestos es tan antiguo como la civilización, el adobe fue probablemente el primero de ellos. La idea es unir dos materiales diferentes de manera que se complementen y tengan mejores propiedades juntos que los dos por separado. Otros ejemplos son el hormigón armado, la clásica estopa con yeso, la fibra de vidrio, y el caso de hoy, el compuesto de fibra de carbono. En este caso, las fibras son las que aportan la resistencia y la resina las agrupa para que mantengan su posición. Dicho en otras palabras, las fibras resisten la tracción, la resina las deformaciones y todos juntos la compresión.
El producto obtenido es muy duro para su peso, no se deforma con el calor, es resistente a agresiones químicas y es conductor de electricidad y calor. Es fascinante sostener un paño de fibras de carbono, que es una tela basta de tacto frío y luego sostener un trozo de compuesto. Éste último, pese a su apariencia plástica, tiene un tacto muy metálico, si la golpeas con los nudillos suena como la chapa metálica. Realmente es un producto muy resistente para el peso que tiene. Para obtener una pieza con resistencia equivalente al acero, la fibra de carbono ocupa sólo un 5 % más y pesa menos de la cuarta parte que el acero, aunque es seis veces más cara.
La tabla que mostramos a continuación muestra la dureza específica de varios compuestos, esto es, el cociente entre dureza y densidad. Dicho de otra manera, decimos que la seda de araña tiene mejor dureza específica que el titanio, pues teniendo más o menos la misma dureza, la densidad de esta seda de es un tercio del titanio. Por lo anterior decimos que la dureza específica de la seda de araña es el triple de la del titanio.
Material | Dureza específica (kN·m/kg o KYuri) |
---|---|
Hormigón | 5 |
Goma | 16 |
Cobre | 25 |
Polipropileno | 28 |
Acero inoxidable (304) | 63 |
Bronce | 68 |
Nilon | 69 |
Roble | 115 |
Aleación de magnesio | 158 |
Aleación de aluminio (7075-T6) | 204 |
Titanio | 288 |
Balsa | 521 |
Compuesto Carbon-epoxy | 785 |
Seda de araña | 1.069 |
Fibra de carburo de silicio | 1.088 |
Fibra de vidrio | 1.307 |
Fibra de basalto | 1.790 |
Vectran | 2.071 |
Fibra de carbono (AS4) | 2.457 |
Kevlar | 2.514 |
Zylon | 3.766 |
Grafeno | 130.000 |
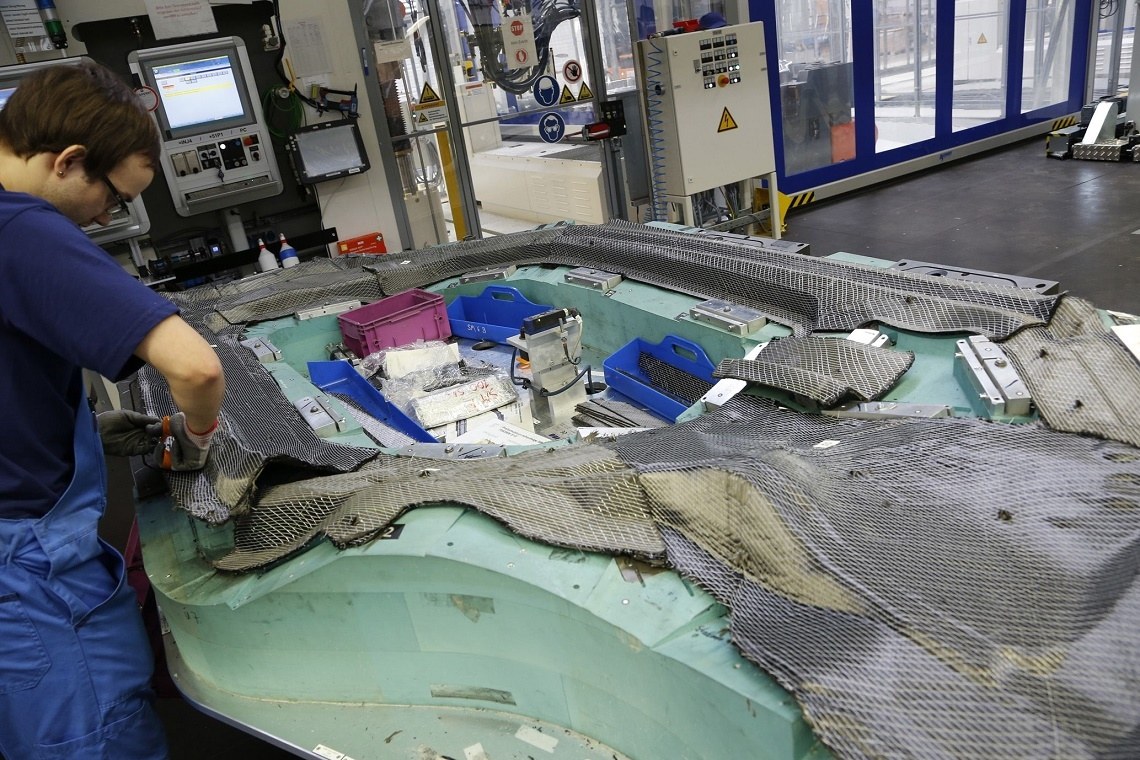
Fabricación manual de compuestos
Para fabricar un compuesto, colocamos lienzos precortados sobre un molde, entre lienzo y lienzo añadimos una capa de resina y presionamos sobre ella para eliminar burbujas. Los lienzos suelen ser precortados dado su precio, de esta manera optimizamos el tejido para desechar lo mínimo posible. La primera capa es la que se pone con más cuidado para que quede perfectamente estirada y con la trama perfecta. Este cuidado con la primera capa no es funcional, sino para cuidar la apariencia del compuesto, porque seguramente esa parte quedará a la vista.
El resto de los lienzos se suelen colocar rotando la trama en cada capa, para que tenga fuerza en todos los sentidos, también hay que recortar el sobrante del material. Después de colocar todas las capas, se embolsa y se le hace vacío, para que le de forma y elimine cualquier posible burbuja. Cuando el vacío es completo, se introduce en un horno a presión que llamamos autoclave. Después de un tiempo, el material está fraguado y sin burbujas. Sólo queda sacarlo del molde. Una nota importante es que, una vez hecha la pieza en carbono, ya no hay ajuste que valga. Si la pieza no sale bien, no es posible ajustarla a martillazos como se haría con el metal, tampoco calentándolo, como algunos plásticos.
Esto último es una de las características de la fibra de carbono: o absorbe la energía sin deformarse o se rompe, no hay término medio. Para facilitar el trabajo del moldeado, se pueden utilizar lienzos de fibras impregnados en resina desde fábrica, con lo que nos ahorramos ese paso manualmente, sólo debemos aplicar presión. Estas fibras preimpregnadas deben guardarse refrigeradas para que no reaccione la resina. La pega está en que hay sacarlas antes de su uso y esta resina tiene fecha de caducidad. El proceso comentado es para piezas planas, cuando las piezas a fabricar tienen forma de tubo, como los pilares, se utilizan núcleos de un material ligero a los que se les van rodeando con capas de fibras.
Resumen de su utilización
La primera aplicación de la fibra de carbono fue en la tecnología aeroespacial. Es un producto ideal para la construcción de fuselajes y elementos aerodinámicos resistentes y muy ligeros. También se empleó en la construcción de las aspas de un turborreactor Rolls-Royce en 1968, aunque pronto fue retirado debido a que los impactos de los pájaros las acababan destrozando. Es como decíamos antes, la fibra de carbono no cede, o aguanta o se parte. Se sigue utilizando en la fabricación de fuselajes y alas de aviones.
El primer automóvil que utilizó la fibra de carbono fue el McLaren de F1 MP4/1 en 1980, desde entonces, McLaren sólo ha construido chasis con este material. Por supuesto, al MP4/1 le siguieron el resto de monoplazas, con lo que ha llegado a ser el material símbolo de la F1. Poco a poco, la fibra de carbono ha ido pasando a todas las disciplinas deportivas en las que prima la ligereza y el presupuesto es amable. En cuanto a la carretera, tanto el Ferrari F40 de 1987 y el Lamborghini Countach 25 Aniversario de 1988 tenían piezas de fibra de carbono en sus chasis. En ese año, el responsable de compuestos de Lamborghini, Horacio Pagani, pidió un autoclave para producir piezas más grandes para futuros modelos. Ante la negativa de la dirección a invertir en materiales compuestos, a los que no le veían una utilidad clara, Horacio creó su propia empresa de ingeniería en fibra de carbono. Años más tarde se convertiría en un especialista en ese nuevo campo y llegaría a fundar su propia marca de automóviles y a patentar un nuevo compuesto, como veremos más tarde.
En 1992 se crea el primer turismo, o debería decir deportivo matriculable, con el chasis completo en fibra de carbono, el McLaren F1. A partir de este modelo, el chasis monocasco en fibra de carbono se normalizó en supercoches. Pasado el tiempo, se empezó a utilizar en los apéndices aerodinámicos y paneles de la carrocería en deportivos premium de algún escalón inferior. A medida que se ha dado a conocer, se usa cada vez más en lugares visibles, aunque no sean tan lógicos, por ejemplo, en colectores de admisión, protecciones en el vano motor, levas tras el volante y cualquier embellecedor que nos imaginemos.
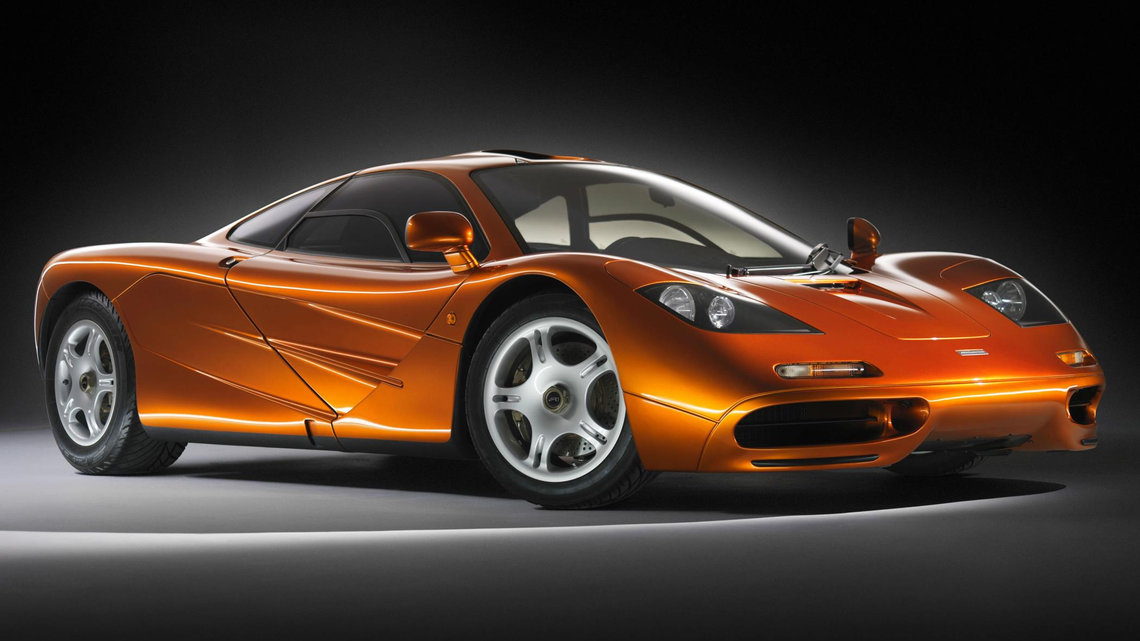
Los elementos anteriores se podrían construir en plástico inyectado, mucho más barato y con la dureza necesaria para su uso. Por otro lado, la fibra de carbono es tan reconocida que siempre se deja a la vista una parte ella, de manera que se vea el típico entramado. Resumiendo, un buen deportivo de hoy en día no sólo debe llevar carbono, también debe mostrarlo. Una opción de decoración actual suele ser llamada “carbono”, en la que se emplean embellecedores de fibra de carbono vista, pero si lo que se busca con el carbono es ahorrar peso, lo lógico es no poner un embellecedor. Es tan conocido este material compuesto que se ha desplazado el uso de la fibra de carbono del chasis a la decoración, esto es, hay automóviles con opción de decoración en carbono sin opción en elementos del chasis.
A medida que se ha reducido su precio, se ha ido utilizando la fibra de carbono en coches menos exclusivos, el Alfa Romeo 4C con monocasco en fibra y un precio de salida de 62.000 euros es un ejemplo, no es barato, pero no es como comprar un hiperdeportivo. La marca menos exclusiva que está introduciendo la fibra de carbono en su gama es BMW. Empezó con algunos detalles en el interior y en sus apéndices aerodinámicos, con el tiempo construyó el M3 con techo en fibra de carbono vista. Desde que apareció este modelo, parece que cualquier BMW blanco con el techo negro correrá mucho más. Otro ejemplo de BMW es el i3, como sabéis es un vehículo eléctrico 100 % con el chasis construido en aluminio y fibra de carbono. En el punto siguiente explicamos cómo se construye sus piezas en compuesto.
La evolución del uso de la fibra de carbono sigue el camino típico de las innovaciones tecnológicas: tecnología aeroespacial, competición de alto nivel, competición general y automóviles premium. Si llega al segmento B, podremos decir que se ha generalizado. Por el momento, el uso de los compuestos basados en fibra de carbono sigue estando en categorías premium, eso sí, cada vez con más usos. De los primeros usos para apéndices aerodinámicos y piezas de chasis hemos pasado a retrovisores, túneles y ejes de transmisión, asientos, volante, levas de transmisión, llantas y prácticamente cualquier pieza rígida que se os ocurra.
Hasta aquí hemos relatado la parte más convencional de la fibra de carbono, tanto en componentes como en procedimientos, pasemos a ver la actualidad de estos compuestos.
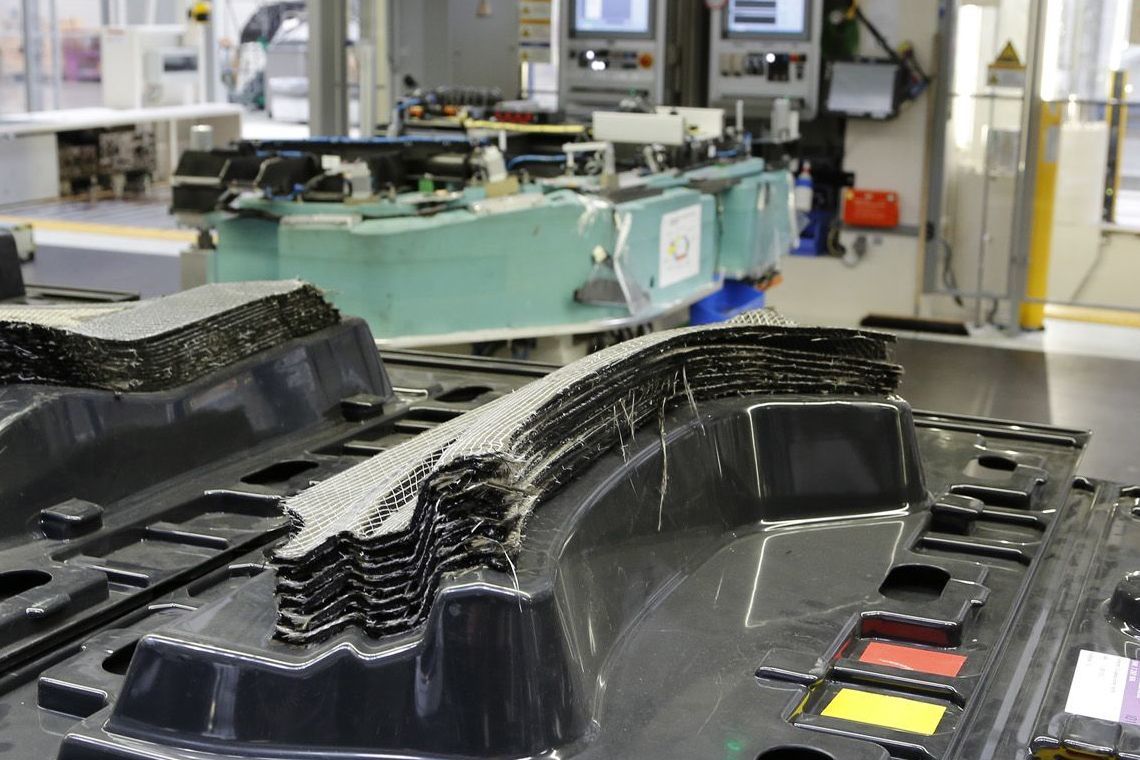
Automatización
Para reducir el precio de un proceso es imprescindible su producción masiva, para abaratar costes en producción y en materia prima por economías de escala. Según un estudio realizado por Jaguar, realizar un vehículo en aluminio en vez de en acero aligera el producto en un 40 % y dobla su precio. Pasar ese chasis de aluminio a fibra de carbono reduce el peso en un 30 %, pero lo encarece 10 veces más. Dicho de otra manera, pasar un automóvil a su equivalente en fibra de carbono reduce su masa un 60 %, pero lo encarece 20 veces más. Como veis, es muchísimo dinero.
El estudio continua diciendo que el importe de una estructura en fibra de carbono en unidades reducidas (menos de 1.000 al año) puede ser de unos 36.000 euros. Si se producen más de 1.000 anuales, ese importe se reduce a la mitad. Si pasamos a más de 10.000 anuales, el importe bajaría a unos 7.000 euros, aproximadamente la quinta parte del precio inicial. Según este estudio, el importe de un chasis de carbono en producción en serie frente a otro de aluminio es de sólo el doble, cuatro veces más que el acero. Estos número ya son más asumibles. Este es el motivo por el que el precio de un i3 está en sintonía con otros vehículos eléctricos similares. Pasamos a resumir la producción de paneles en fibra de carbono de este modelo.
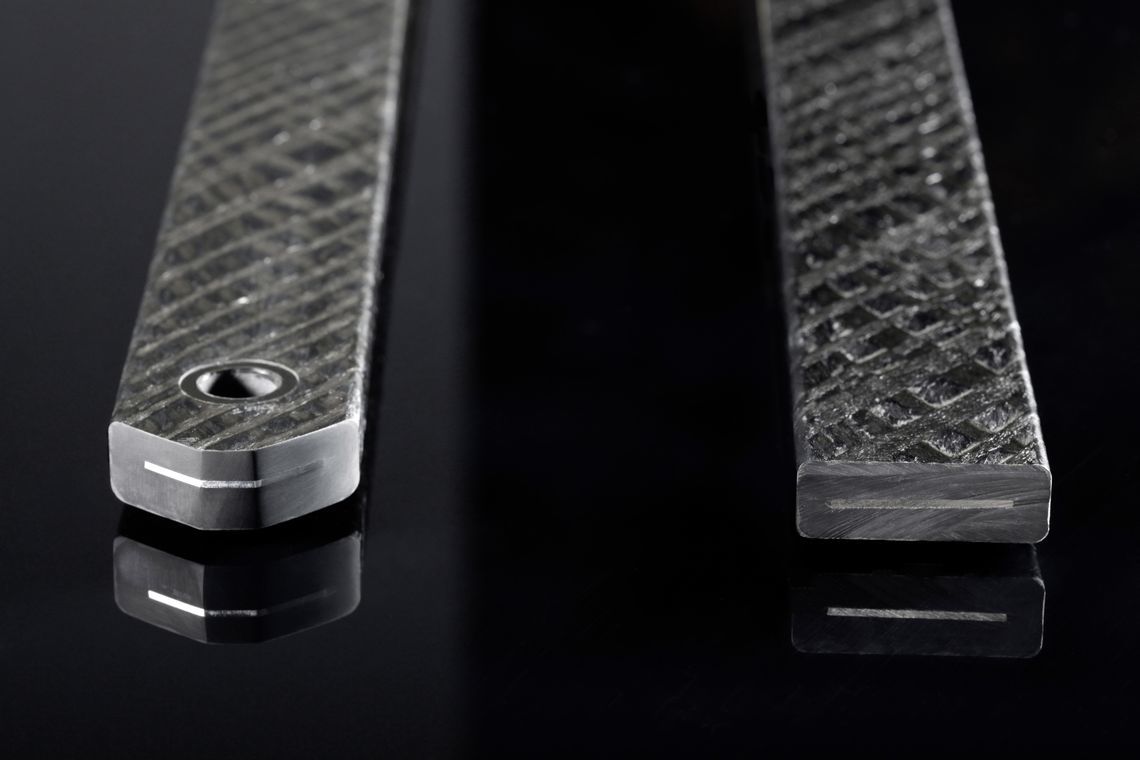
Siempre es complejo automatizar un proceso en el que los objetos a manipular son blandos, que es lo que pasa con los tejidos de fibra de carbono. La primera empresa automotriz que ha desarrollado un sistema automatizado para construir piezas moldeadas es BMW. Para ello, utiliza los mismos lienzos que se pueden utilizar a mano. Estos lienzos de fibra de carbono son llevados a moldes, una prensa hace la fuerza necesaria para que el lienzo tome la forma. Mientras está curándose en el molde, un robot corta el sobrante de la fibra de carbono, pues los lienzos utilizados son rectangulares. Estas piezas son subcomponentes del chasis, se colocan después todas ellas a mano en un molde más grande.
Este molde se lleva a una prensa mucho mayor, que es la que finaliza la pieza del chasis. Los sobrantes de fibra y resina son cortados al agua por dos robots. Así queda listo el panel de carbono, una vez acabados todos los paneles, se montan y unen al subchasis de aluminio, que contiene las baterías. Aquí podéis ver un vídeo de la producción completa del i3.
¿Qué inconveniente tiene este proceso? Según veo sólo uno, la estética. Si recordáis, cuando el compuesto se realiza a mano, la primera capa se coloca con mucho mimo, porque probablemente estará a la vista. Al realizarse de manera automática, este factor se pierde, y el coche no nos recibe de la misma elegancia. Podéis comparar las dos maneras tan diferentes de recibirnos un i3 y un 4C en las imágenes que nos acompañan.
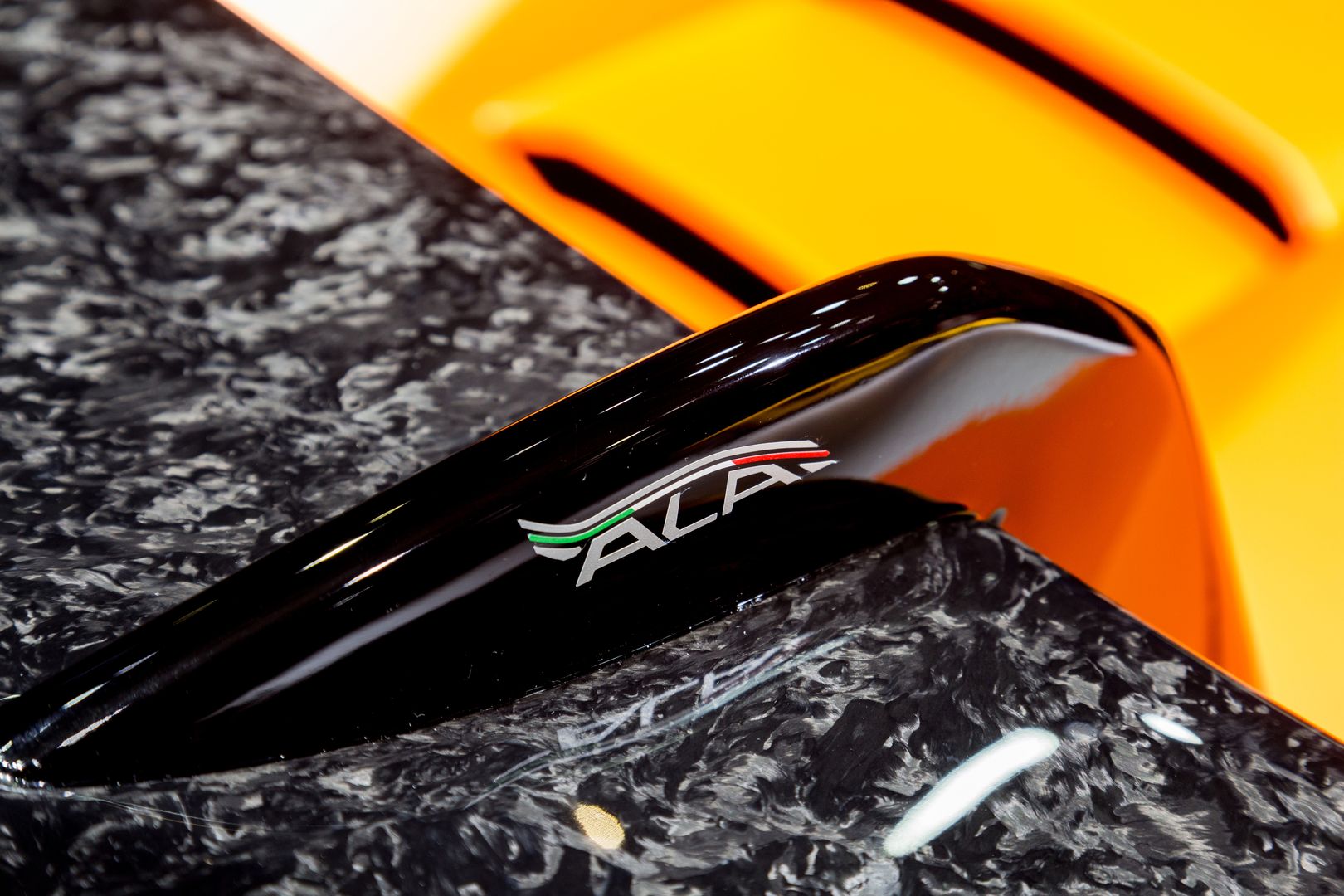
En Lamborghini idearon un sistema para reducir costes al que llaman Forged Composite. Este proceso se inventó en 2010 para el Sesto Elemento. Gracias a la utilización masiva de fibra de carbono en este modelo su peso total en vacío era de sólo 999 kg, permitiendo prestaciones de vértigo. La técnica es similar a la anterior: se colocan varias láminas de fibra de carbono sobre un molde. Una prensa lo comprime, lo mantiene un tiempo y finalmente lo libera. Este sistema es rápido y permite más libertad en la geometría de las piezas. Otro efecto es que su superficie es de clase A, esto es, acabado perfecto. Este sistema surgió para componentes estructurales y se está utilizando para piezas expuestas. Estas piezas tienen un aspecto peculiar entre cristalizado, nacarado o jaspeado.
Existe otro tipo de producción automatizada de compuestos llamado pultrusión, es básicamente una extrusión de material plástico y fibras en modo continuo. En este caso se hacen pasar por el mismo molde: un núcleo metálico, fibras de carbono y la resina que los une. Este proceso necesita menos energía y no tiene prácticamente pérdida de material. El inconveniente es que sólo se pueden hacer piezas extrusionadas, esto es, el mismo perfil alargado en un eje.
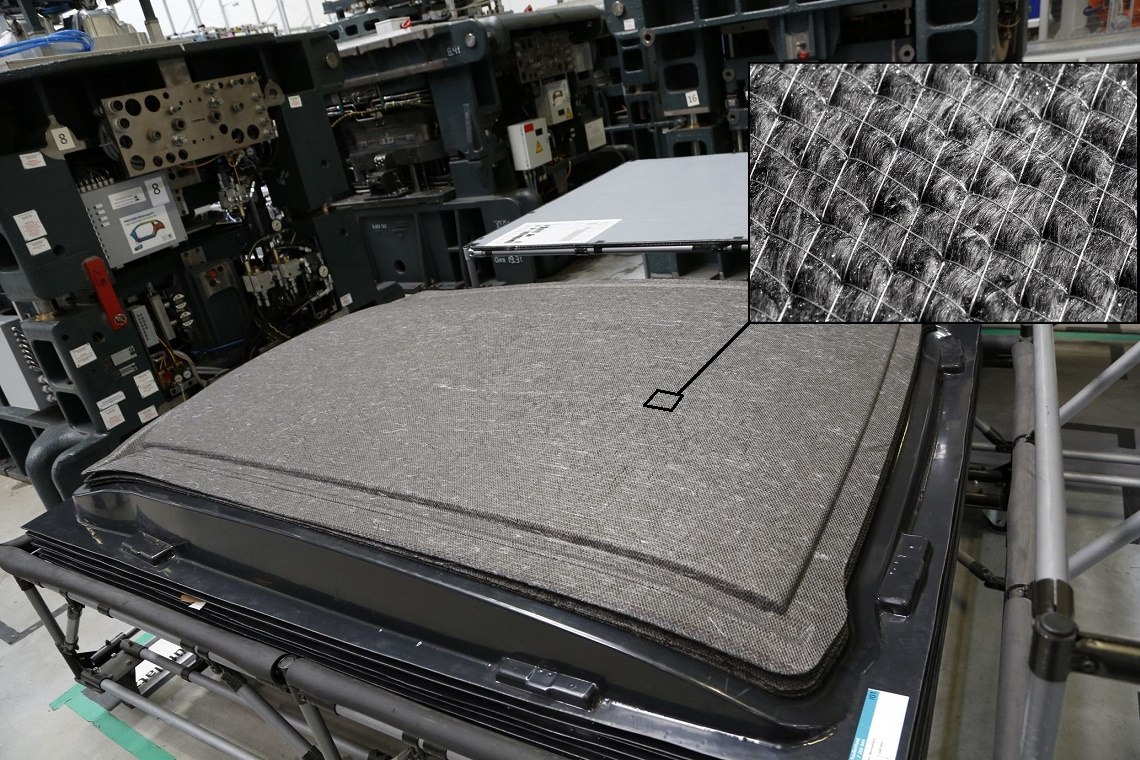
Reciclaje
Una de las preocupaciones actuales en la industria es cómo impactar lo mínimo posible en la naturaleza, además de reducir cualquier tipo de coste. En el caso de metales, como el acero o el aluminio, cualquier sobrante de la producción se envía a reciclar. Una vez acabada la vida útil de un automóvil también se reciclan sus metales. De esos metales de deshecho se pueden producir aleaciones de características iguales o incluso superiores a las originales, además, podemos reciclar de manera infinita.
Desde 2015, el 95 % del peso de un vehículo fuera de uso tiene que ser reciclable, solo el 5 % puede ser simple residuo
En cuanto a los plásticos es un poco más complejo, pues hay muchos más tipos y no siempre se pueden producir plásticos de calidad similar al material del que proceden. En el caso de la fibra de carbono se complica más, es muy difícil separar las fibras de las resinas. Por otro lado, la cantidad de piezas fabricadas en este compuesto no es tan grande como para generar una industria específica de reciclaje.
Sin embargo, es más sencillo recuperar los sobrantes de fibras producidos en los recortes de los lienzos antes de moldearlos. Recordando la fabricación automática de compuestos del i3, dijimos que se recortaban los sobrantes de los lienzos que quedaban por fuera del molde. Estas fibras se recuperan y son cardadas en vez de tejidas, formando una especie de fieltro. En BMW se han comprometido a utilizar en sus coches un mínimo de fibras de carbono recicladas. En sus modelos son utilizadas, sobre todo, en el techo y el panel separador del maletero.
Zylon en la Fórmula 1
Ya comentamos que el primer automóvil en utilizar la fibra de carbono fue el McLaren MP4/1 en 1980, constituyéndose en un estándar de facto en la F1. Muchos años después, antes de la temporada de 2007, y por motivos de seguridad aparecieron normativas en cuanto al uso de estos materiales. La normativa dice que las estructuras del morro y la trasera del monoplaza deben ser deformables para la absorción de posibles impactos. Por otro lado, los laterales del chasis deben ser de 6 mm y estar cubiertos de una lámina antiintrusión de un material llamado zylon. Estas láminas se deben extender desde el fondo del cockpit hasta llegar al área de la cabeza del piloto.
Por otro lado, desde el 2011, la parte alta de las viseras de los cascos de F1 llevan una tira de 50 mm de alto, también de zylon, para evitar que entren objetos. Esta normativa surgió tras el impacto de un muelle al visor del casco de Felipe Massa en 2009. Esta tira apenas aumenta el peso del casco en 70 g, pero dobla la resistencia del visor. En la imagen de Nico, la tira de zylon está cubierta por publicidad de los patrocinadores. El zylon es conocido como la “fibra de carbono de la fibra de carbono”, veamos por qué.
El zylon, o PBO, es una fibra sintética creada por la compañía japonesa Toyobo en los 80 del siglo pasado. Esta fibra es muy difícil de crear, de ahí su elevado precio. Según sus creadores, el zylon es la fibra conocida con más resistencia a la tracción. Según nos informan, una hebra de 1 mm de diámetro es capaz de sostener un peso de 450 Kg, no está nada mal. Esta fibra tiene una resistencia específica superior a la de la fibra de carbono, ese motivo sería suficiente para utilizarla en F1, pero tiene otro que también es muy importante. Este segundo motivo es que soporta hasta 650 ºC antes de arder, manteniendo su forma y evitando los nocivos gases que desprende la fibra de carbono en su combustión.
Estas dos cualidades, resistencia a la intrusión y al fuego, hacen perfecto este material para los monoplazas y el exigente entorno de la competición. Basta recordar cómo salió Fernando Alonso con sólo una ligera cojera después de un vuelo rasante a 300 km/h.
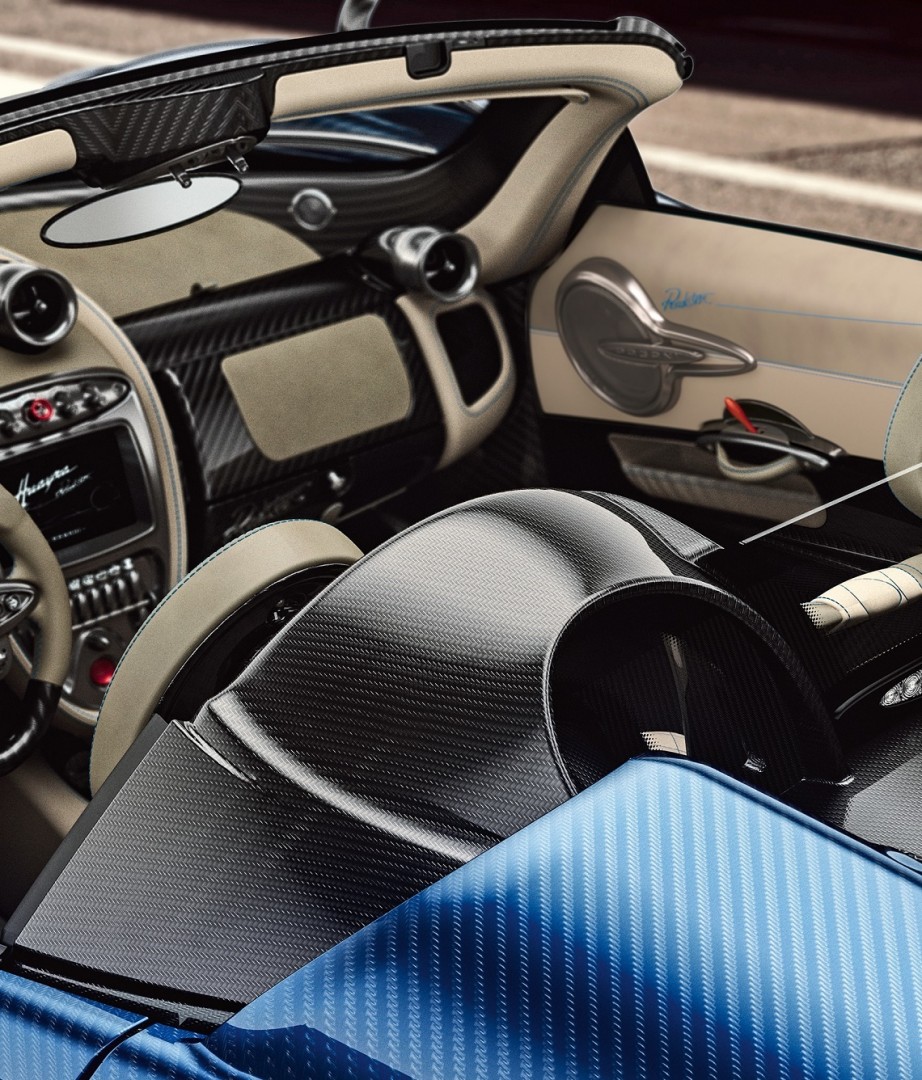
No sólo fibra de carbono, cuando tres o más no son multitud. Pagani con carbotanium
Como ya dijimos, Pagani fue uno de los pioneros en la utilización de los materiales compuestos. En el año 2009 utilizó por primera vez un nuevo compuesto en el Zonda R. A las fibras de carbono se les añadieron hebras de titanio. De esta manera, el compuesto resultante es más elástico y, en caso de accidente, no estalla en miles de astillas. Esto último es un posible problema que puede tener la fibra de carbono. Cuando un compuesto de fibra de carbono cede, lo hace partiéndose en una multitud de astillas. Si el tamaño de éstas es grande, no es preocupante, sólo debemos tener cuidado para no cortarnos con ellas, pues sus bordes suelen ser muy afilados; si su tamaño es muy pequeño podrían ser inhaladas al respirar. La versión actual del Huayra también utiliza este material, además de las ventajas de ligereza, fuerza y flexibilidad, el fabricante nos regala con una textura carbono-metal preciosa.
Otras veces se han mezclado las fibras de carbono con otras de aramida, la más conocida es el kevlar. Estas fibras sintéticas son de la familia de las poliamidas, como el nailon. Su resistencia es menor que la fibra de carbono, aunque absorbe muy bien la energía de los golpes. Actualmente no se utiliza mucho, quizás se mantenga por motivos estéticos. Dado que se puede colorear al fabricarla, se utiliza para crear lienzos de un color diferente al negro. Como ya dijimos, la tendencia actual es la de mostrar la fibra, al contrario que al inicio, que estaba siempre oculto.
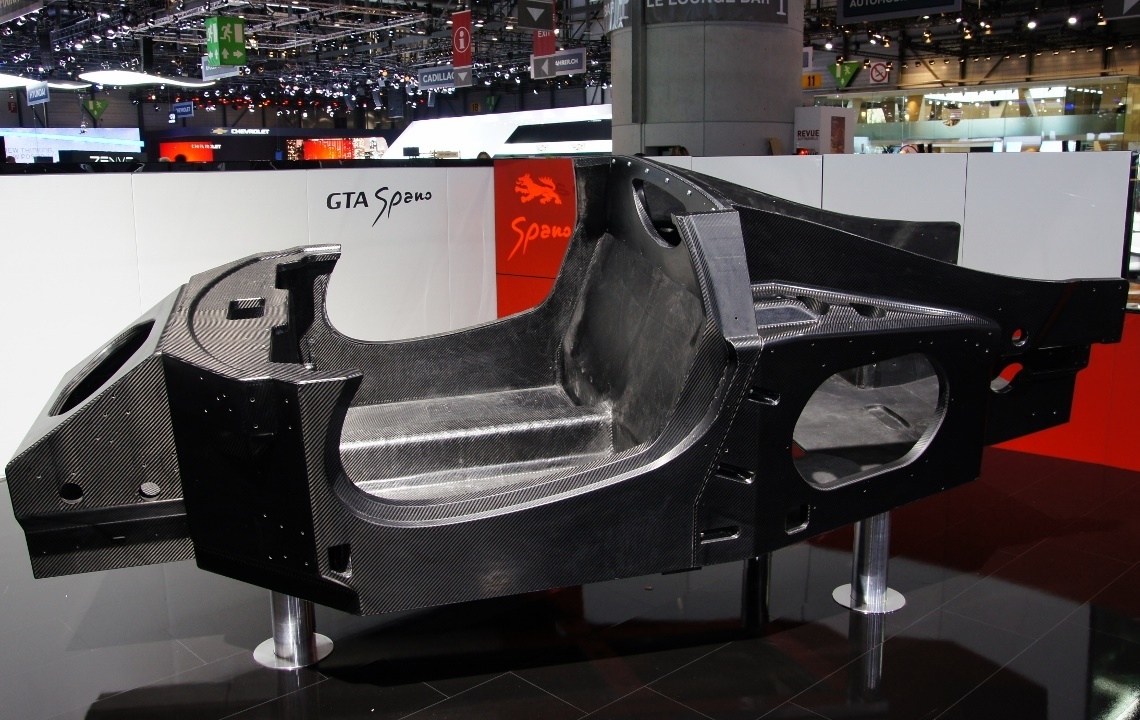
Grafeno con el GTA Spano
Muy bien, dando un repaso a las fibras compuestas utilizadas en la automoción, tanto las que hemos visto como las que no, y por orden de aparición serían éstas: fibra de vidrio, kevlar, fibra de carbono, zylon y carbotanium. ¿Ha parado ahí?, pues no, seguimos investigando. Si hay algún material sinónimo de futuro ahora mismo es el grafeno. Este material está compuesto enteramente de carbono, lo que le diferencia es la manera es su estructura molecular. Hasta ahora hemos hablado de polímeros sintéticos.
Los polímeros son macromoléculas de cadenas de monómeros repetidos. Estos monómeros son, a su vez, otras moléculas, capaces de unirse. En el caso del grafito, sólo contiene átomos de carbono en una estructura bidimensional en la que cada átomo de carbono está enlazado con otros tres equidistantes. Por este tipo de enlace surge una estructura que forma celdas hexagonales, similar a un panal de abejas. Decimos que es bidimensional porque el grafeno forma una sola capa de espesor un átomo, esto es, un átomo sólo se enlaza con los adyacentes laterales.
El resultado es una estructura muy resistente, pues forman un enlace perfecto. Por otro lado, cada átomo tiene un electrón libre en su última órbita, lo que hace que sea muy fácil su movimiento; dicho en otras palabras, es altamente conductor. La materia prima para este material es el grafito, de ahí su nombre. Os sonará porque es la materia de la que están hechas las minas de nuestros lápices, sólo cambia que el grafito está laminado y el grafeno es un continuo.
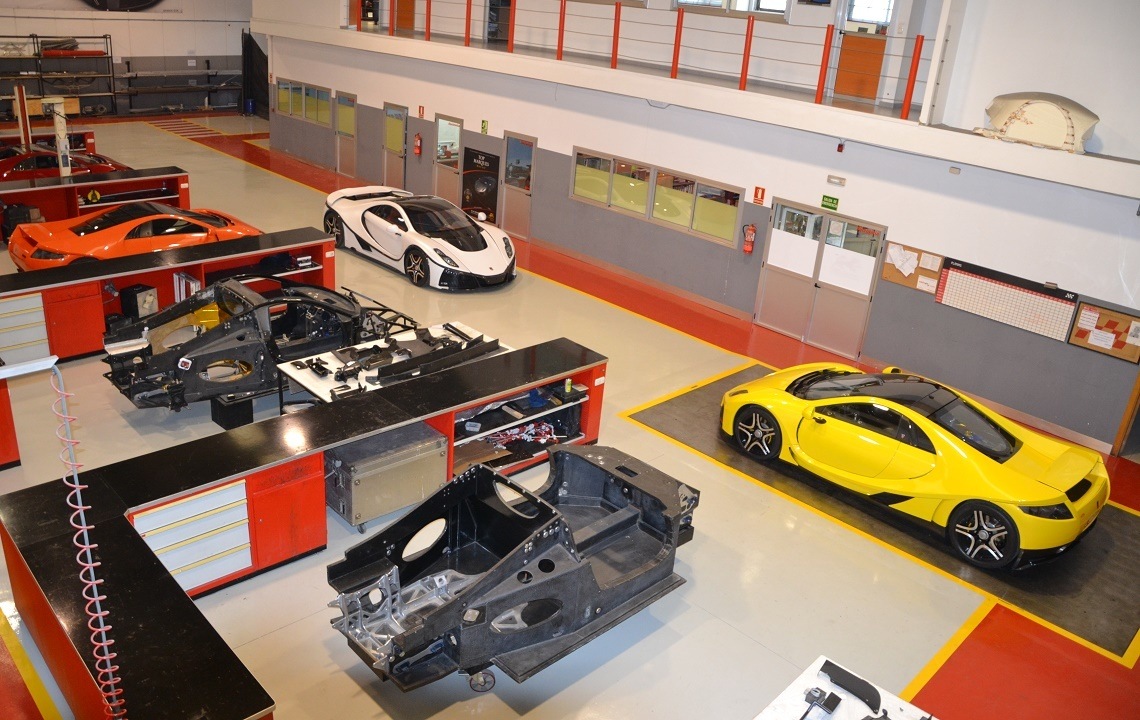
Parece un material muy novedoso, sin embargo su estructura se describió en 1916. Este material quedó en el cajón del olvido dado que se pensaba que iba a ser inestable y no se le encontró ninguna aplicación. Casi un siglo después, en 2004, el material fue “redescubierto” por Andréy Gueim y Konstantín Novosiólov, que recibieron el premio Nobel de Física en 2010 por “sus innovadores experimentos del material bidimensional grafeno”.
Por su construcción atómica, sus cualidades físicas son extremas en varios apartados. Por ejemplo, es el material más resistente que se conoce. Si os fijáis en el cuadro del principio, el grafeno está al final de la lista de la dureza específica. Si pudiésemos construir un lienzo de 1 m² de una sola capa de este material, podría soportar 4 kg, repito, una sola capa de espesor 1 átomo. Dicho en otras palabras, podríamos construir una hamaca en grafeno de 1 m² para un gato de 4 kg pesando sólamente 0,00077 g, menos que un bigote del mismo. Todavía se sigue investigando en este material para descubrir más características aplicables a la industria. El precio de momento es muy caro y no se ha aplicado mucho en la automoción. La primera vez que se ha utilizado el grafeno ha sido para la segunda serie del GTA Spano. Como ya sabréis, es un hiperdeportivo fabricado en Valencia.
En este vehículo se aplica el grafeno en tres tipos de componentes. El primer componente es el chasis, está construido en fibra de carbono y es reforzado con grafeno. Destacamos que el chasis de este vehículo está construido enteramente de fibra de carbono, cuando lo usual es que los subchasis que soportan las suspensiones y motor sean de aluminio. Además de esto, el núcleo de la fibra de carbono está formado por un exótico material aeroespacial: paneles huecos de aleación de titanio.
En el segundo tipo de componente que se utiliza son las pieles del interior del habitáculo, para fortalecerlas y así se pueden utilizar piezas más finas que puedan moldearse mejor. El último uso de los tres es por otra familia de cualidades del grafeno -en un futuro veremos que son tan importantes como su dureza-. Es utilizado en la construcción de sus baterías. Por la baja resistencia eléctrica del grafeno estas baterías son más pequeñas y más ligeras.
De momento es un material muy escaso por lo cara que es su fabricación, si se inventa un proceso más económico, puede convertirse realmente en el material del futuro, y si algo sobra en el planeta, es carbono
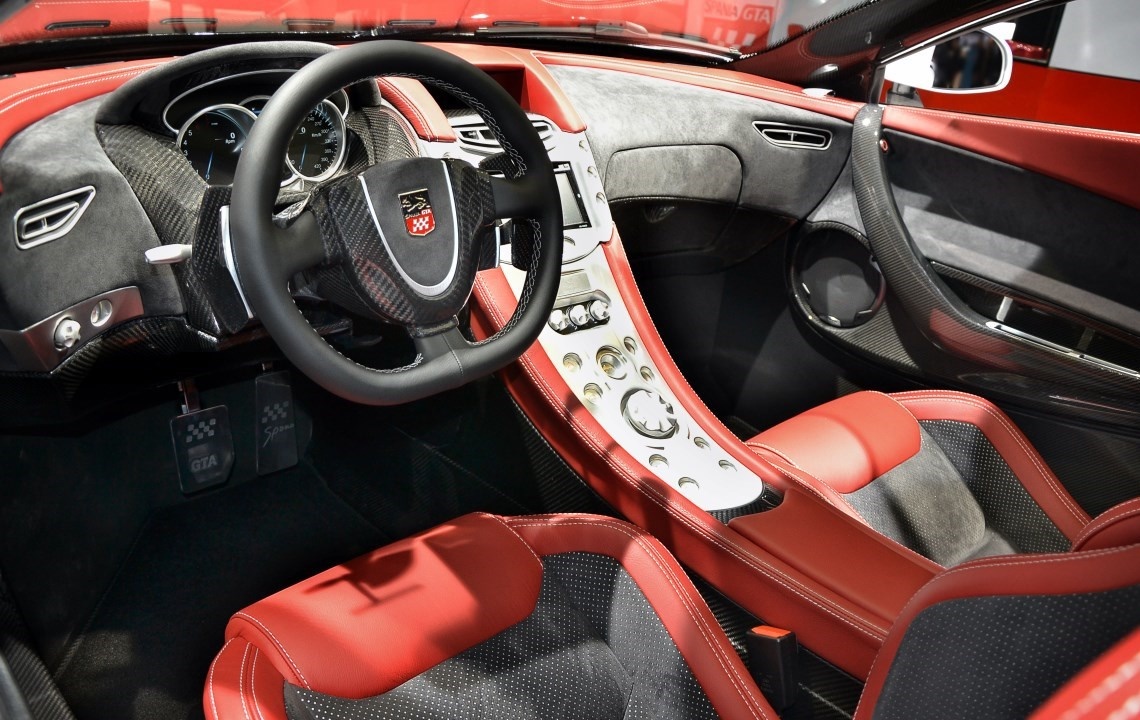
¿Cómo serán los próximos vehículos?
Como ya dijimos en el estudio de la metalurgia actual del automóvil, el presente y futuro de la automoción es seleccionar el material adecuado para cada componente. Esto es, para una zona de carga siempre será mejor el acero, que es el que mejor resiste los malos tratos, aunque el chasis sea de aluminio, solo hay que ver qué ha pasado con los pick-up F-150 de aluminio. La mayor parte de piezas que no necesiten mucha presión serán construidas en plástico inyectado, mirad el pedal del embrague de vuestro coche, probablemente será plástico. A medida que se produzcan más cantidad de materiales compuestos, su precio se abaratará y permitirá colocarlo en coches cada vez más económicos.
Esta obra, cuyo autor soy yo mismo, se publicó el 17 de junio de 2017 bajo una licencia de Reconocimiento 4.0 Internacional de Creative Commons.
J.J. López
Portador del contagioso virus de los coches desde los once años. Ingeniero en informática, programador de robots y visión artificial que lo piensa todo en coches. Amante del arte, técnica y tecnología en movimiento, esto es, apasionado incondicional del automóvil.Abran paso al “Carbino” cuando deje de ser inestable (me refiero al material) sin la ayuda de grafeno. Casi tan duro como la uña pulgar de Chuck Norris y rozando la flexibilidad de una hilera de ciclistas domingueros.
El universo de los materiales me apasiona (por ejemplo, al papel moneda de 500 euros le guardardo tal respeto, que mantengo siempre las distancias). Bromas aparte, olé por el artículo. Artículo de escándalo.
Excepcional articulo, sin duda.
Y aqui enlazamos con temas comerciales. No se si nos damos cuenta que al contrario que su competencia, Lambo y McLaren, Ferrari no emplea fibra en los chasis de los coches “de serie”. Si que emplea fibra en algunas piezas y paneles (siempre cobrada a cojón de mico), pero Ferrari es capaz de vender un coche de aluminio por 340 000 € ¿cuanto tiempo podra hacerlo?
Leo unas cuantas webs de tematica de coches deportivos y estos tipos de articulos no se leen todos los dias. Una lectura muy amena y un tema muy moderno y bien documentado.
Los animo a que sigan asi en el equipo y que nos ofrezcan articulos como este de buenos y diferentes, ademas tecnicamente en español no hay tamts cosas como nos gustaria y en ingles se hace la lectura mas dificil.
Animo y sigan asi.
No encuentro en los blogs que suelo frecuentar de coches (todos muy conocidos) articulos de este nivel.Enhorabuena y muchas gracias
Esto es lo que nos diferencia, tener ingenieros que escriben de maravilla como J.J.. Pásate por la sección de “Reportajes” https://espirituracer.com/reportajes/ y prepara las palomitas. Te agradecemos enormemente que nos sigas.
Muchísimas gracias, Paco. No me imagino mejor halago.