A medida que van apareciendo nuevos modelos de automóviles, los fabricantes nos informan que son más ligeros, más rígidos y más seguros que la generación anterior, todo esto sin grandes aumentos de precio. ¿Cómo se puede conseguir? ¿Es posible conseguirlo todo a la vez? Vamos a dar un pequeño paseo por las técnicas y materiales actuales en la metalurgia de los automóviles, describiendo primero los procesos clásicos.
Fundición tradicional
La fundición tradicional consiste en verter metal fundido en el interior de un molde para que tome la forma del interior. Cuando el vaciado -así se llama a la copia obtenida del molde- se encuentra sólido, ya se pueden mecanizar las partes necesarias por extracción de viruta, taladrando, fresando o roscando. En algunos casos, la pieza obtenida se vuelve a calentar o se forja, para que el metal obtenga mejores propiedades de elasticidad o dureza.
En la fundición tradicional, tenemos un molde de un solo uso construido en una arena especial. El molde se puede formar en esta arena con un modelo igual a pieza que queremos hacer, sólo necesitamos que es modelo sea rígido, no importa el material. Este modelo debe ser un poco mayor a la pieza deseada pues la colada disminuye de volumen a medida que se enfría. Podemos hacer un vaciado de prácticamente cualquier pieza que inventemos, con tamaños desde centímetros a varios metros. Si deseamos una pieza más exacta podemos recurrir al moldeo en cera perdida. En este antiquísimo proceso tenemos un paso más. Realmente generamos un modelo en cera, o en otro material que se pueda descomponer fácilmente, tan exacto como necesitemos. Ese modelo puede ser hecho directamente como una escultura o bien con otro molde.
El objetivo es que este modelo intermedio sea lo más fiel posible al producto final. Una vez que tenemos hecho este modelo en cera, sirve de base para generar un molde de un solo uso, pero en arcilla en vez de arena. El motivo de construirlo en arcilla es porque su grano es mucho más fino que la arena y el vaciado será también más exacto. Una vez construido el nuevo molde de arcilla se elimina la cera simplemente calentándolo. Así queda el molde con el vacío correspondiente al modelo de cera que hicimos, una vez limpio y seco se le puede verter la colada.
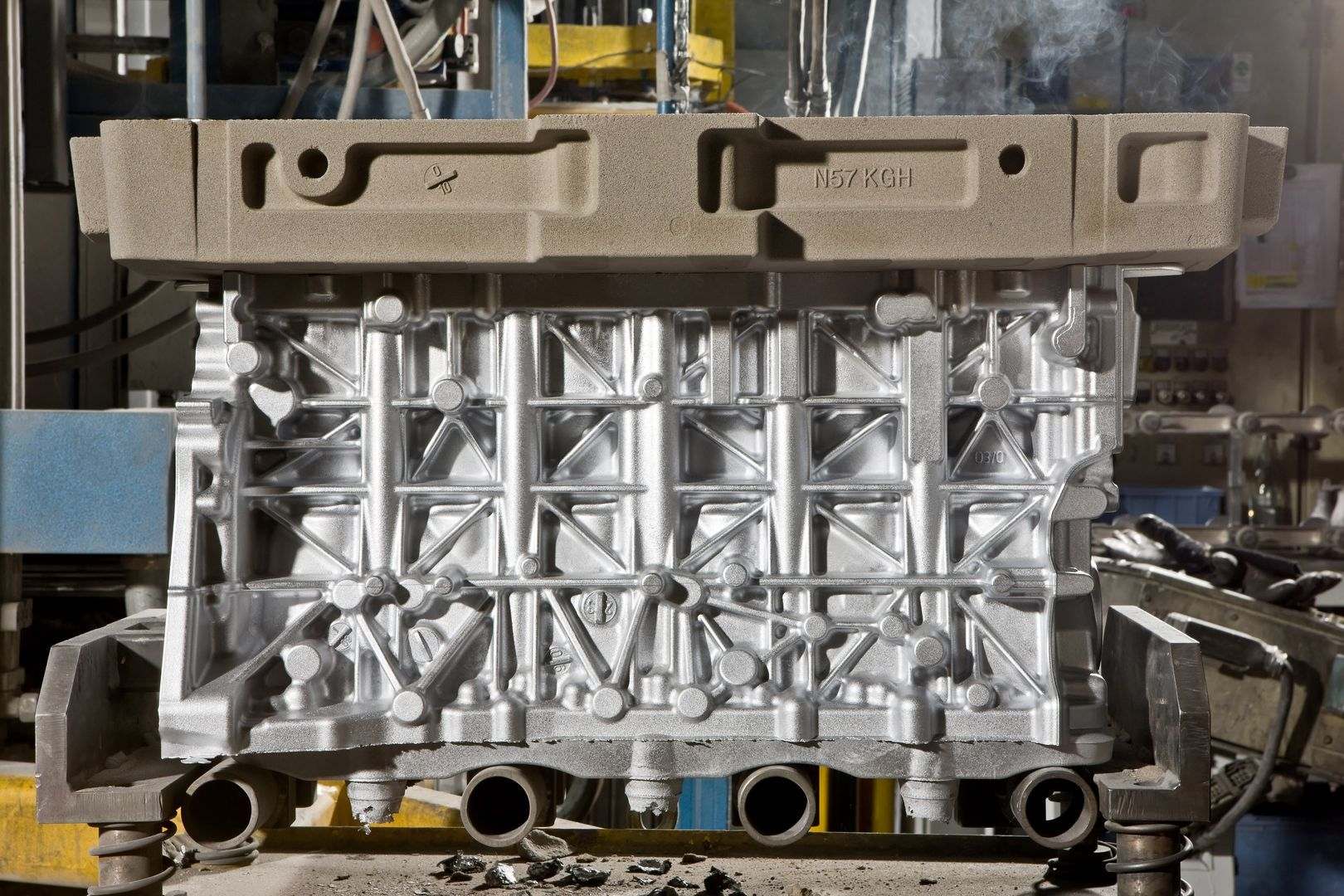
Cuando la pieza es muy compleja, como un bloque motor, se construye el molde con piezas fabricadas a su vez con otros moldes para que sea más preciso. El molde lo forman las paredes exteriores, que es fácil de entender, y las piezas que forman los huecos, principalmente los cilindros y los pasos de la refrigeración. Para estos pasos se colocan unas piezas de arena con la forma de los huecos. En el caso de la culata, las piezas que forman los pasos para la entrada y salida de gases tienen la curiosa forma de cuernos. Las piezas que forman el molde son diseñadas para que encajen fácilmente.
Una vez ensambladas se les vierte el metal fundido. Cuando se enfría la colada, se desmoldea por vibración. Este tipo de arena suele ser reutilizable. Las principales ventajas de la fundición tradicional es que se pueden fundir piezas de cualquier tamaño y es relativamente fácil su técnica. Los inconvenientes de esta técnica son que se trabaja a muy altas temperaturas -1500 ºC en caso del acero- una tolerancia en la geometría bastante alta (prácticamente siempre debemos mecanizarlos para asegurarnos de sus cotas), los moldes son de un solo uso y un tiempo de ciclo elevado al ser enfriado a temperatura ambiente.
Fundición de aluminio a presión
Son varias las diferencias con la fundición tradicional. En este caso el molde es reutilizable, construido en un material que debe soportar la temperatura de trabajo. El aluminio se inyecta a presión con un tornillo sin fin dentro del molde -muy similar a la inyección de plástico- en vez de caer por gravedad. El molde se enfría con ayuda de un circuito cerrado de agua, pero sin que se pierda la presión del fluido -en vez de a temperatura ambiente. Cuando el líquido se ha solidificado, se abre el molde y unos extractores se encargan de desencajarlo, en ese momento se puede extraer el vaciado.
En comparación con la fundición normal, las piezas pueden producirse con geometría más precisa. La tolerancia de este proceso está en torno a décimas, las paredes mínimas pueden ser de 0,75 mm. Esta precisión hace que se reduzcan, e incluso eliminen, posteriores mecanizados. Además, al forzar el enfriado, podemos hacer más piezas por hora. Otra ventaja es que puede tener elementos móviles dentro del molde, por ejemplo, podemos poner pasadores cruzados que luego se convertirán en agujeros o no y podremos hacer dos piezas con el mismo molde.
El gran inconveniente es que esta tecnología es mucho más compleja, o sea más cara, con lo que sólo se aplica si la tirada es muy larga, al contrario que la fundición tradicional, con la que podemos hacer un solo molde para sólo una vez.
Con esta técnica se fabrican piezas de aluminio inyectado para unir el chasis con otras piezas. Las más de las veces se utilizan para unir el chasis con la suspensión. En esta infografía del nuevo Honda/Acura NSX se aprecia en amarillo dónde van colocadas las piezas de aluminio fundido. Estas piezas son de fundición de aluminio, aunque su técnica es diferente, no son por moldeo a presión. Para estas piezas, el molde es de arena y, una vez vertido el aluminio, ésta se elimina mediante chorro de agua, a la vez que enfría el material.
Este chorro de agua también erosiona la capa externa del material. Por este proceso se endurece el material para darle consistencia a la estructura y una alta rigidez en caso de accidente. Por ser de aluminio pesa menos que el equivalente en acero y, al ser moldeado, tiene la forma precisa evitando mecanizados posteriores.
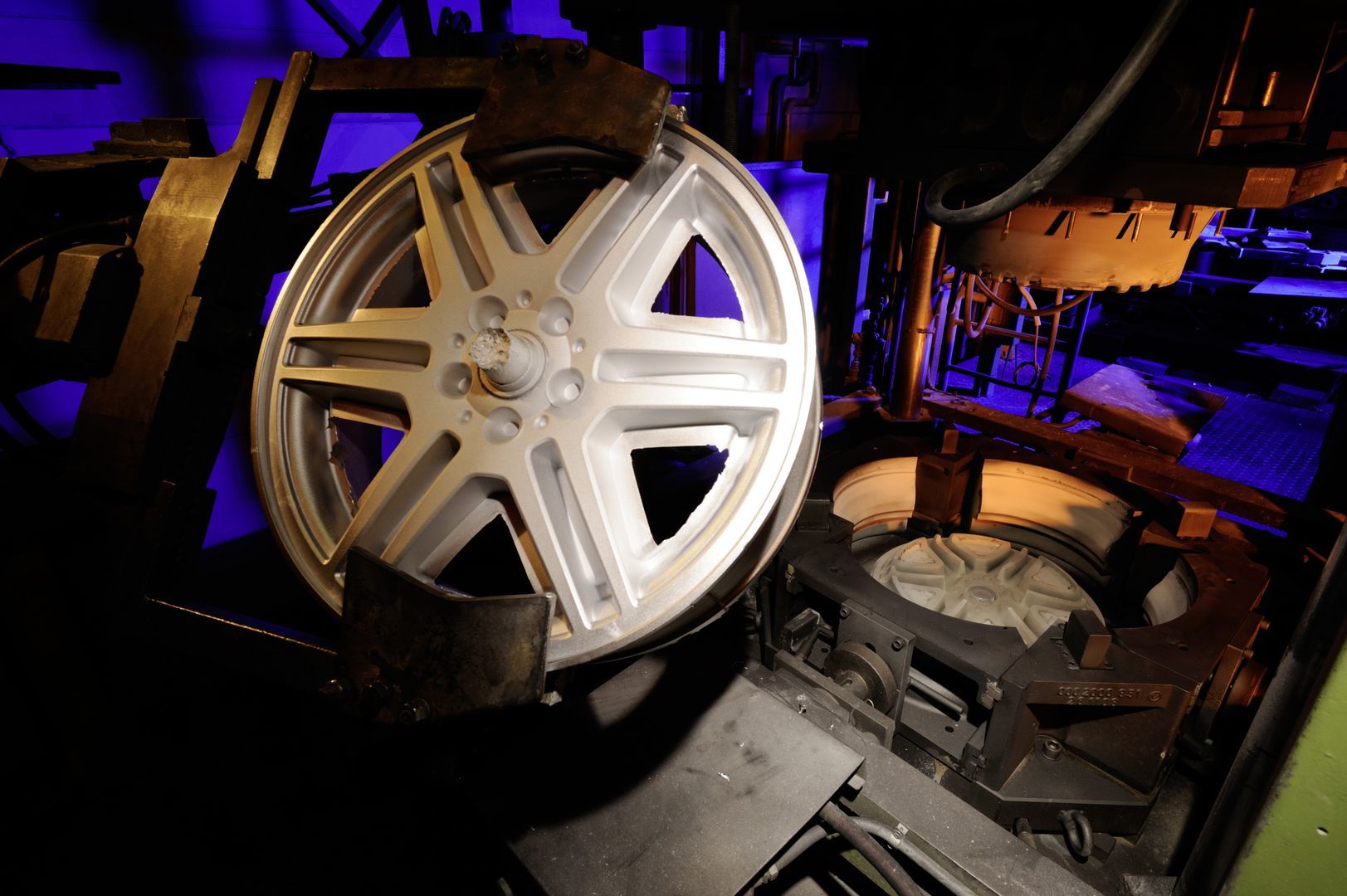
Ejemplo real: cómo se hacen unas llantas de Mercedes-Benz
Las indicaciones que estamos dando para estos procesos están simplificadas al máximo, realmente hay mucha técnica detrás de estos procesos, sencillos en apariencia. En cuanto a materiales no sólo hay muchas aleaciones, sino también muchos tipos de arena y desmoldeantes. Las temperaturas de trabajo, de secado y tiempos de los procesos también son cruciales. También hay muchas maneras de extraer las piezas. A continuación, veremos un resumen de la construcción de llantas de aleación ligera de aluminio para turismos Mercedes.
El primer paso es crear una preforma de la rueda por el proceso de moldeado de aluminio, en este caso a baja presión. El aluminio se calienta a 775 ºC y se inyecta al molde. El punto de la inyección está en la parte inferior del molde, para que lo rellene completamente desde abajo hacia arriba. El exceso de material sale por el centro del cubo hacia el exterior. Después del correspondiente tiempo de solidificación, el molde se abre en varias partes para poder extraer correctamente la pieza. En este paso, la preforma de la rueda es estrecha y gruesa, más parecida a la rueda de una carretilla que a la de un turismo deportivo, enseguida veremos por qué.
Después del desmoldeado, todas las piezas son inspeccionadas por rayos X para comprobar que no tienen ninguna fisura ni burbuja en su interior, eso que no hacen los fabricantes chinos de imitación por mucho menos precio. Después de esto, sigue un tratamiento para estabilización del aluminio. Dicho proceso consiste en calentarlas a 530 ºC, después mantenerlas varias horas a 150 ºC y el paso final es un baño de agua. Ya las tenemos listas para el paso siguiente, la laminación.
La laminación es el proceso por el que se transforma una lámina enrollada mediante la presión de unos rodillos, ya sea estirándola, compactándola o uniendo varias láminas entre sí. Como dijimos, la preforma era muy estrecha y gruesa, esto facilita el trabajo del moldeado. El siguiente paso es calentarla a 350 ºC, después la colocamos sobre un eje, la hacemos girar y le aplicamos más de 100 toneladas de fuerza en tres rodillos que la presionan contra el eje y la estiran. Este laminación es un poco especial, estiramos la pieza girándola sobre sí misma y presionándola con dos rodillos contra el eje sobre la que rota, casi podríamos decir que es un repujado. Con este proceso se consiguen dos cosas, darle la forma definitiva y, gracias al calor y a la presión, conseguir que se forje, dándole más dureza.
El siguiente paso es el mecanizado o maquinado. Este paso le proporciona las medidas definitivas a la forma, además de mecanizar todos los puntos necesarios: el cubo, alojamientos de tuercas, el alojamiento de la válvula neumática, etc. Estamos insistiendo mucho en el mecanizado porque una de las preocupaciones de la industria metalúrgica es reducirlo al mínimo, por motivos muy evidentes y por otros no tanto. Los más evidentes es que si queremos hacer una pieza por el proceso del mecanizado, necesitaríamos partir de una pieza más grande, en este caso el vaciado debería ser mayor, por lo que necesitaríamos fundir más material y más calor para empezar.
Luego tenemos el tiempo de trabajo y el desgaste de las herramientas de corte y maquinaria. El motivo menos evidente es que a más mecanizado, más contaminación. Las virutas no son tan reciclables como otra chatarra pues están contaminadas con el lubricante de corte que protegen a las herramientas. Cuando la pieza es un prototipo o la tirada es muy corta se suele mecanizar mucho, cuando la tirada es larga se buscan otras técnicas para reducirlo.
Después del mecanizado quedan los tratamientos de protección, pintura y barnizado. Como dato curioso, las partes con alto brillo son zonas que se pulen y luego se protegen. Sólo nos queda poner los neumáticos e hincharlos y ya tenemos las ruedas listas para colocar a nuestro coche.
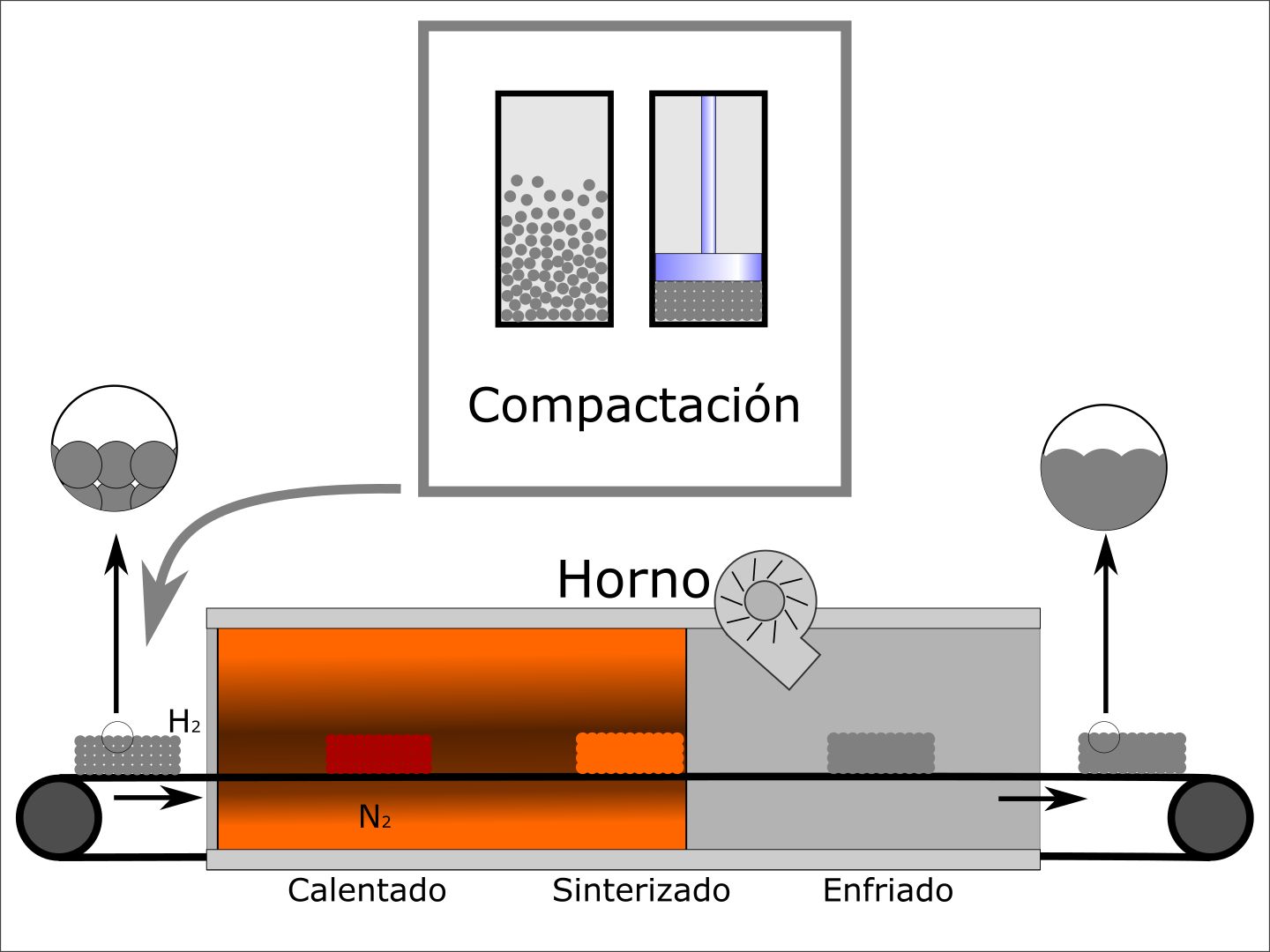
Sinterizado
Es un proceso de fundido de componentes, pueden ser tanto metálicos como cerámicos, alternativo a la fundición clásica. La materia prima está en forma de polvo. El proceso se basa en que la temperatura de sinterizado de dicho material en polvo es inferior a la de su fusión. En el caso del acero, la temperatura para la fundición es de 1500 ºC, la temperatura del sinterizado es de 850 ºC, considerablemente inferior.
El procedimiento es como sigue. Se llena el interior del molde con el metal en polvo. Este metal contiene un poco de lubricante para ayudar al moldeo y desmoldeo. El metal es compactado en el interior del molde gracias a la fuerza de la prensa. Después, la pieza ya compactada es expulsada de la matriz y llevada al horno. Esta pieza es denominada “verde” y es muy parecida a un polvorón apretado. La pieza tiene aspecto de acabada, aunque sólo está compactada y es muy frágil; si una pieza verde se cae al suelo o se le aplica algo de fuerza se puede quebrar. Este tipo de pieza no se almacena dado su fragilidad, una vez extraída va directa al horno.
El paso de llevar la pieza verde al horno suele estar automatizado cuando ésta tiene forma irregular o es demasiado frágil, siendo el encargado un brazo mecánico o un robot. El horno tiene una cortina de hidrógeno y una atmósfera protectora de nitrógeno para evitar que entre oxígeno o cualquier impureza. Las piezas entran al horno y a medida que se van calentando sus moléculas se expanden y se ablandan, desapareciendo los huecos existentes y fundiéndose entre ellas. Finalmente, todas las moléculas se unen manteniendo la forma de la pieza compactada. La segunda cámara del horno se encarga de enfriar las piezas para que mantengan su forma. En la descarga, la pieza ya es muy dura, se puede sacar por procedimientos automatizados o directamente a granel.
Aquí dejo un vídeo del proceso:
Después de este proceso, las piezas son tratadas como cualquier pieza de fundición. Se les aplica tratamientos calóricos o compresivos para fortalecerlas o se mecanizan si las queremos más precisas, algunas piezas sencillas no necesitan ningún tratamiento.
¿Cuáles son las ventajas de este proceso? Pues la verdad es que tiene muchas. En primer lugar, no necesitamos fundir la materia prima antes de moldear, con lo que el molde trabaja a temperatura a menos de 100 ºC. La temperatura se genera por la energía perdida durante la compactación. Dicho molde puede ser de acero de alta dureza simplemente, sin necesidad de refrigeración externa. La temperatura de sinterizado es de unos 850 ºC para el acero como hemos dicho, por esto los hornos son más sencillos y consumen menos. Por el contrario, las prensas que compactan las preformas suelen ser complejas, aunque tienen la ventaja de que los moldes son más sencillos a la larga, ya que son reutilizables y más fáciles de modificar.
Por ejemplo, si estamos haciendo piñones y queremos cambiar el eje redondo por uno cuadrado, sólo tenemos que cambiar el punzón central y el taladro del contramolde. Otro ejemplo, si estamos haciendo una polea y queremos que tenga ocho taladros, sólo tenemos que añadir dichos taladros con su medida y posición al molde. Hacer esto último en la fundición clásica sería muy problemático para taladros muy pequeños, habría que recurrir al mecanizado pues dicha fundición no es muy precisa y su diámetro tampoco sería muy exacto. Otra ventaja es que podemos controlar la materia prima al 100 %, no hay contaminación por escoria. También podemos hacer cualquier aleación, simplemente tendremos que mezclar el polvo antes de la compactación.
El acabado de las piezas es mucho mejor que en la fundición clásica, además, su mecanizado es más fácil e incluso a veces no es necesario. En la fundición clásica se utilizan moldes de dos piezas y siempre se escapa algo de material entre estas dos mitades. Ese material forma rebabas que hay que eliminar con algún abrasivo. En el sinterizado apenas se forman. En algunos casos se pueden eliminar por un proceso automático. Las piezas se colocan en un contenedor con un vibrador y se les añade pequeñas piezas de un material más duro, cerámico normalmente. El choque constante de las piezas entre sí y con los abrasivos consigue eliminar las asperezas.
Los inconvenientes son tres. El primero es que no es válido para piezas muy grandes, no se suelen hacer piezas por este método más allá de 30 cm de longitud. Para este tamaño, la prensa debería ser muy potente para compactar tanto material, también sería muy complejo extraerla bien y que no se rompiera de camino al horno. La otra pega es que no se pueden hacer espesores muy finos, pues las paredes de la pieza se derrumbarían muy fácilmente, los puntos más estrechos suelen ser de unos 4 mm. Esto se soluciona fabricando la preforma más gruesa y luego mecanizarla a la medida requerida. Finalmente, la altura de la pieza suele variar, ya que dependemos de la cantidad de polvo que entre y de otras condiciones, como su humedad, temperatura, etc. Esto se soluciona con un mecanizado posterior. Si bien la pieza generada por este procedimiento no es más ligera o resistente que en la fundición clásica, su coste energético sí es mucho mejor así como su pureza.
Hidroconformado
Esta técnica se utiliza para moldear tubos mediante agua a presión. El material a conformar puede ser prácticamente cualquier metal, incluso acero de alta dureza. El proceso es como sigue: el tubo, recto o ya doblado previamente, se introduce dentro de un molde, después se inyecta el agua a presión de manera que lo hincha dentro del molde para que tome la forma requerida. Después se recorta o abren los taladros necesarios. Con este proceso se pueden hacer escapes de motores a explosión sin ninguna soldadura. De esta manera conseguimos que sea más rápido de fabricar, menos piezas, menos procesos, menos interferencias para los gases de escape en su interior y más estéticos.
Al tener menos piezas conseguimos también ahorrar peso. El fabricante de prensas alemán Schuler AG afirma que el arco formado por los pilares A de la versión cabrio del Serie 3 E46 de BMW, consigue pasar de siete piezas soldadas a tres con esta técnica. Además, informa de que este arco es capaz de sostener el peso de cuatro vehículos. Otro punto a favor de este sistema es el eliminar las soldaduras, además de simplificar el proceso y materiales, el producto acabado es más homogéneo y no tiene puntos de tensión debidos a la alta temperatura del proceso.
Otro uso de esta técnica muy original es para construir árboles de levas. Tradicionalmente, los árboles de levas se construyen con un cilindro macizo al que se le tornea la forma de las levas. Para reducir su peso se puede vaciar. Sin embargo, en un cilindro tan delgado no se podría hacer por el sistema del torneado. Si fuera proporcionalmente más corto o más ancho se podría introducir una broca del tamaño adecuado para traspasarlo.
Sin embargo, el mecanizado aquí calentaría tanto la pieza y generaría tanto par que no podría hacerse de una manera práctica. Con el sistema del hidroconformado, podemos colocar el tubo y soplar dentro del molde y listo. Al parecer en este caso también se moldean las pistas de las levas a la vez.
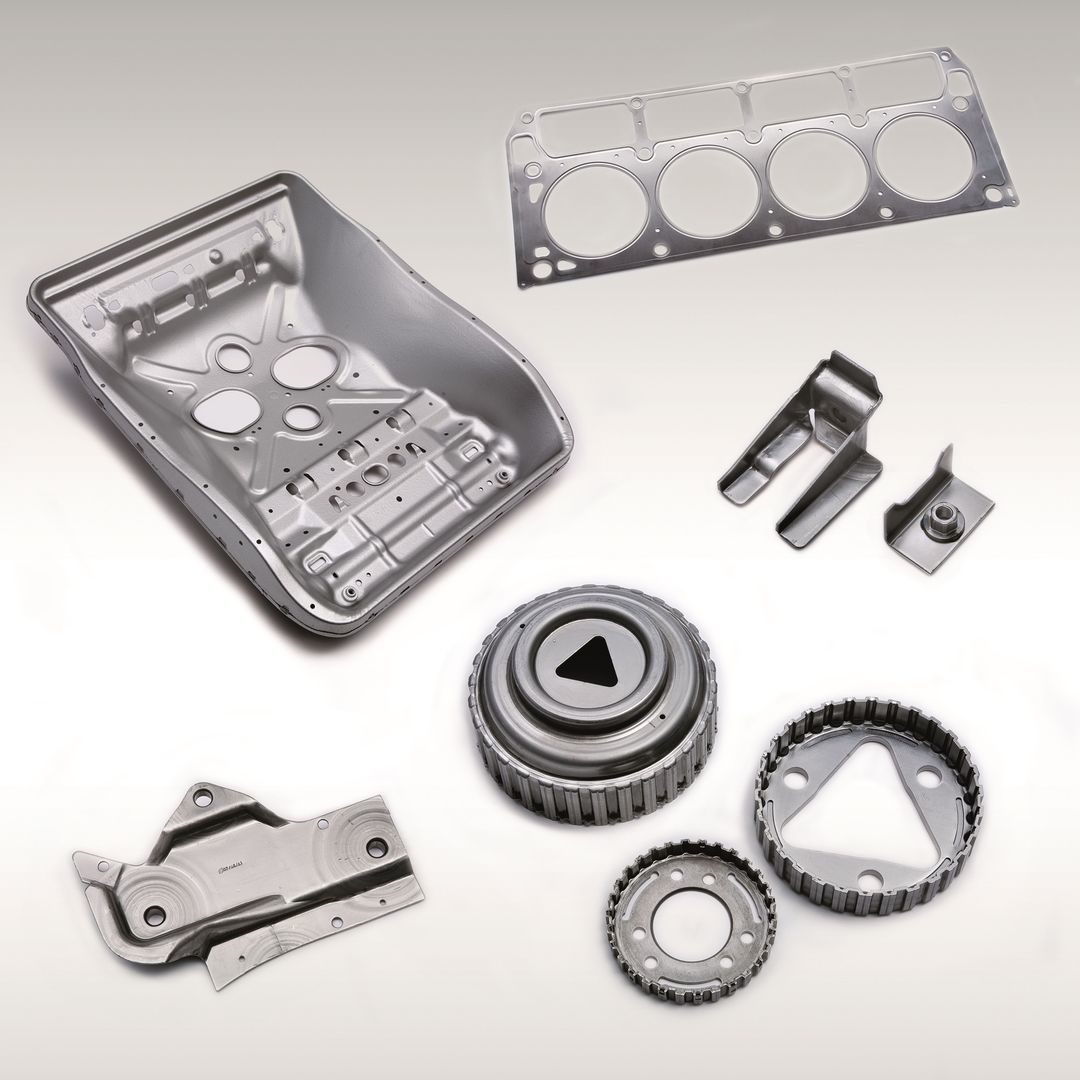
Estampación
La estampación consiste en dar forma y recortar una lámina de metal por el método de prensado. En el procedimiento clásico podríamos decir que en una fábrica de carrocerías entran bobinas por una puerta y salen carrocerías acabadas por otra. Realmente ha sido así durante muchos años, ahora se están aplicando más técnicas y materiales para la construcción de una carrocería.
Veamos primero la estampación tradicional. Se basa en láminas de acero que se colocan en el interior de un molde, accionado por una prensa. La hoja primero se embute, dándole forma, y luego se recortan las partes sobrantes. A veces todos estos pasos se hacen en un solo molde que actúa de manera progresiva. En un caso típico primero se le da forma, después se abren taladros y ventanas y en el último paso, se recorta el sobrante. Otras veces, la misma prensa tiene varios troqueles en serie, de manera que cada uno de ellos hace un paso de la estampación y es la pieza la que se va moviendo de estación a estación.
El tipo de pieza y su material son muy variables. En cuanto tamaño, se pueden estampar desde las grapas que sujetan los faros -unos 10mm- hasta laterales completos del vehículo. Un ejemplo de reutilización de matrices y prensas son las grapas que sujetan los faros del Audi Q7 de primera serie y del SEAT Ibiza coetáneo. Estas grapas se fabricaron con la misma prensa y matriz. El material para el Q7 era acero inoxidable de 1,2 mm de espesor y latón de 0,8 mm para el utilitario.
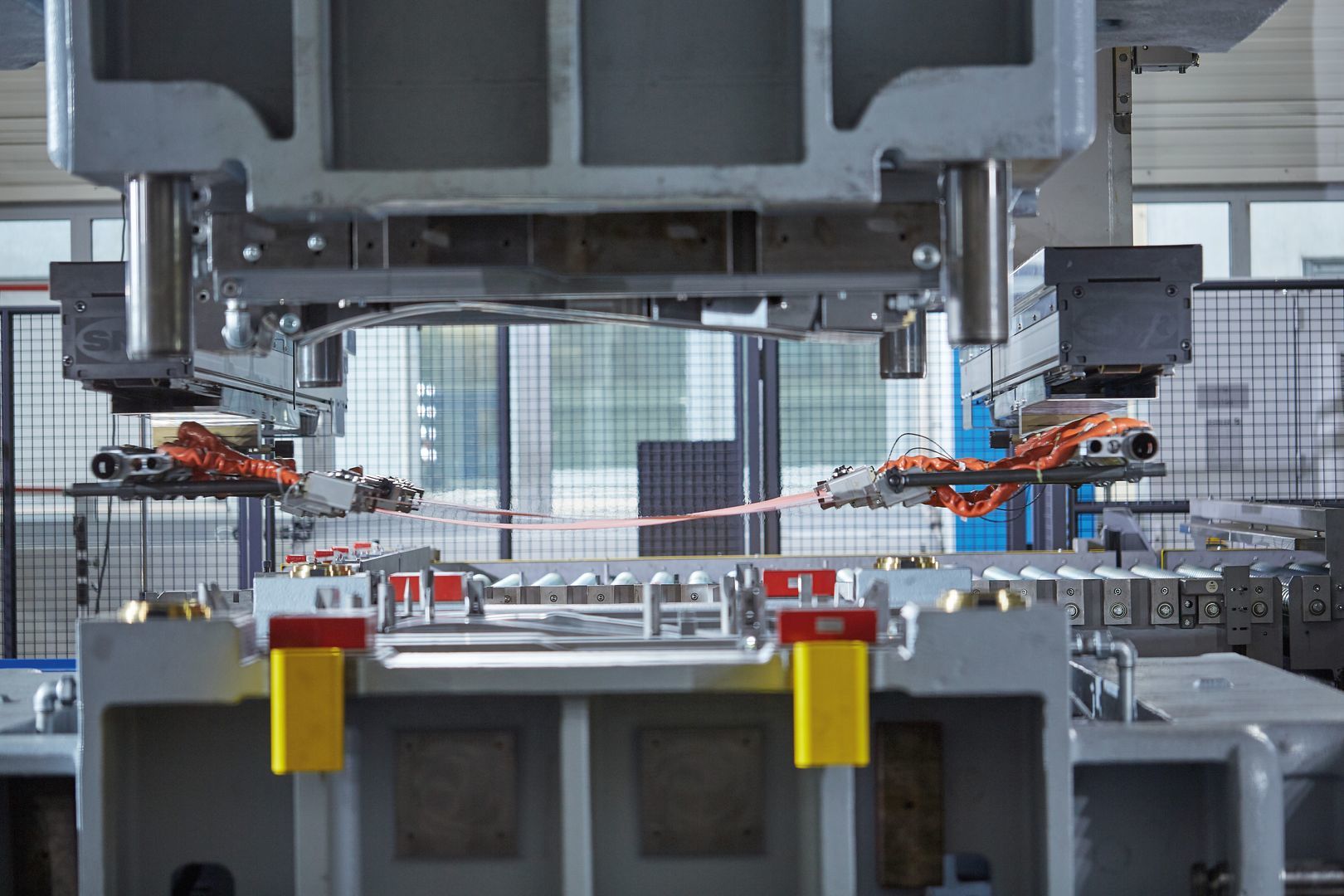
Normalmente, para piezas pequeñas, la chapa viene en forma de bobina. Para las piezas más grandes lo normal es utilizar láminas ya precortadas con el tamaño justo. Como siempre en industria, el tipo de máquina depende del número de piezas que se vayan a fabricar. Los moldes de las prensas siempre son intercambiables, así una misma prensa puede hacer varias piezas en su vida útil. En los automóviles, las piezas internas suelen tener una vida mucho más larga que la de las externas. Me explico, los elementos internos como bisagras, barras antiintrusión de puertas, anclajes de asientos, soportes, etc. son diseñados, calculados, probados y homologados para su uso.
Normalmente se homologan en industria y se utilizan durante mucho tiempo en varios modelos para amortizar el coste de su desarrollo. Si todo esto se cumple, la tirada de producción suele ser larga y el cambio de molde poco frecuente. En el exterior ocurre justo lo contrario, son modificadas mucho más a menudo. Por ejemplo, en cada restyling las piezas ocultas suelen ser las mismas, pero si cambia la forma de los faros delanteros, el capó también es diferente y debemos cambiar su molde. En el caso de ser vehículos de poca tirada o con muchas variaciones entre sus versiones, el cambio de moldes es muy corriente. Para facilitar ese paso, se construyen centros de prensado en línea con alimentación automática de moldes y paquetes de láminas, destacamos que el peso de esos moldes suele ser de varias toneladas.
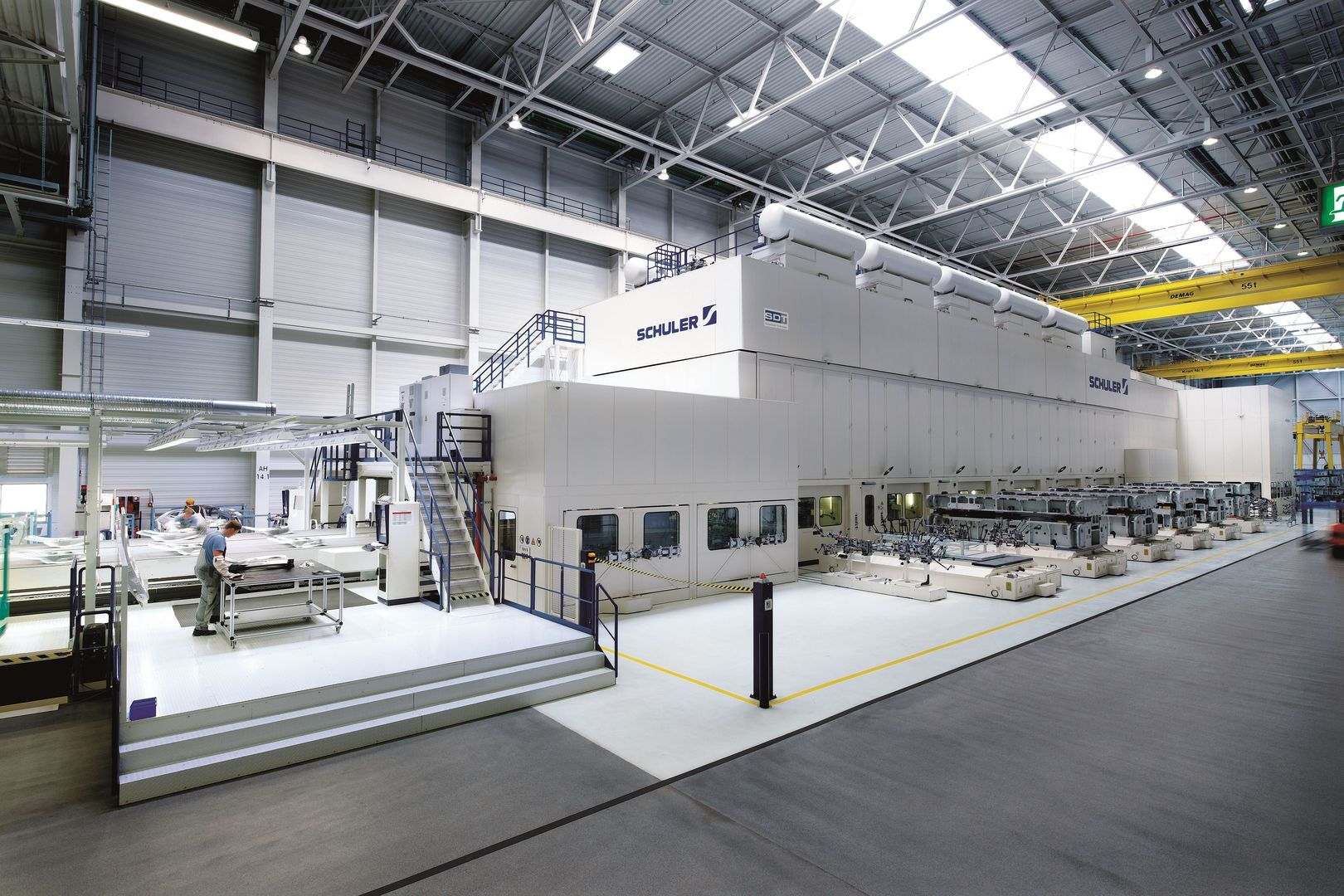
Este caso es el de BMW, tiene una prensa en línea que está totalmente automatizada. Por un lado, tiene robots que cargan y descargan las láminas y las piezas estampadas. Además, cuando cambia la pieza y los robots necesitan una herramienta diferente para cogerlas, ellos mismos se las cambian. Por otro lado, los paquetes de chapas se alimentan automáticamente. Para finalizar, los moldes van sobre carros automatizados que los colocan en las prensas correspondientes cuando ha finalizado un lote de producción y debemos pasar a una pieza diferente.
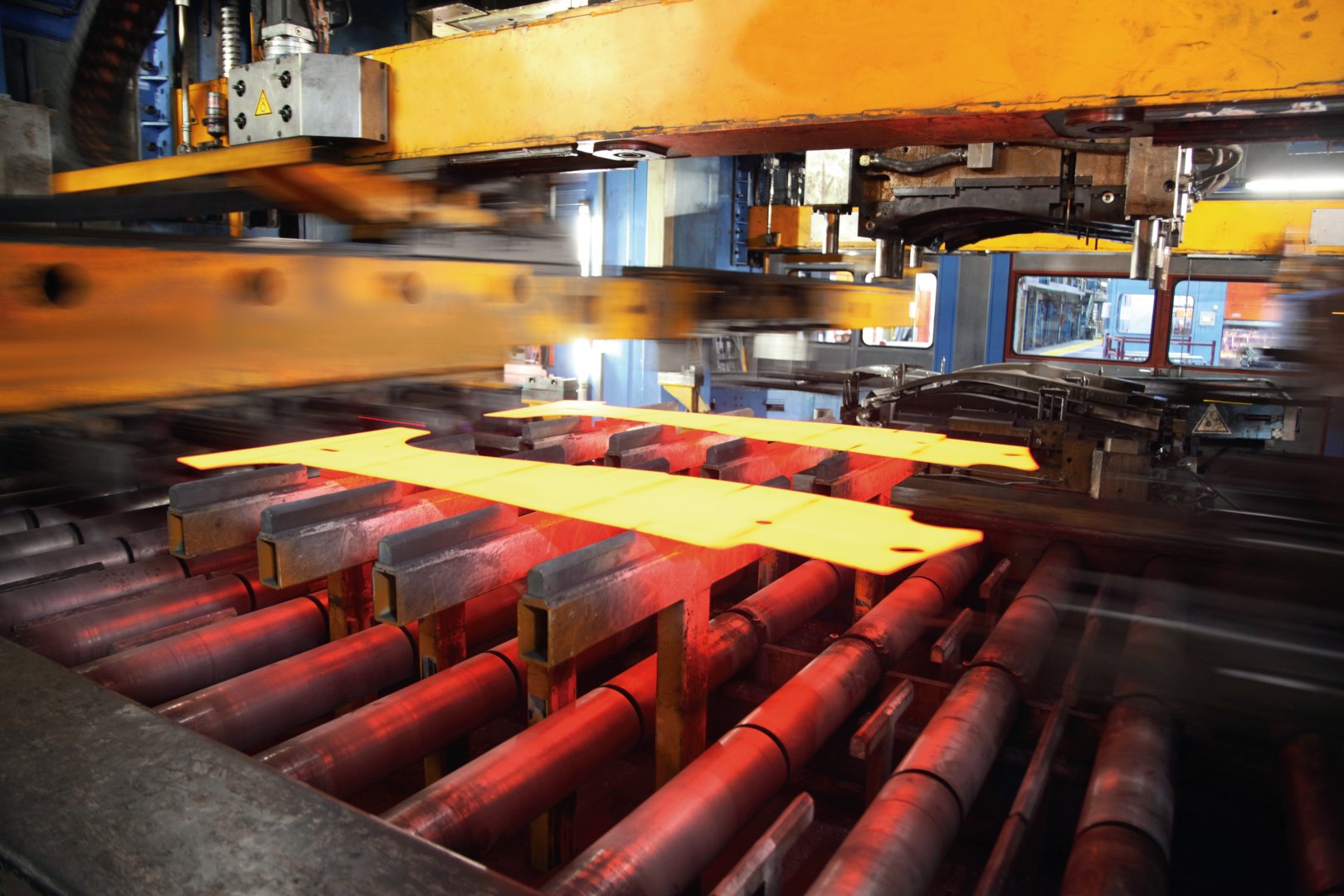
Nueva técnica, Hot Forming o conformado en caliente
Como decía al inicio, a medida que cambiamos de modelos son más rígidos, seguros y ligeros, vamos a ver una técnica que se encarga de esto. En la estampación clásica, entra una lámina de metal y sale una pieza, con otra forma, pero sin modificar su estructura interna. En el conformado en caliente, la chapa se corta a medida, se calienta en un horno a 950 ºC, se coloca dentro de la prensa y es moldeada y enfriada dentro de ella. En esta técnica se la aplican procesos térmicos y compresivos en el mismo paso.
Si lo vemos de otra manera, al presionar un metal caliente y enfriarlo de manera rápida, lo que hacemos es forjarlo, cambiamos su estructura molecular haciéndolo más rígido. Además, el material de las láminas es especial, es acero al boro, para que sea más fácil la alineación de sus moléculas. Con este proceso estamos endureciendo considerablemente las piezas, incluso si su grosor es menor.
Además, al estar la pieza en caliente, su conformado dentro del molde es mucho más preciso. En las piezas estampadas en frío es la propia matriz la que corta los sobrantes, en el Hot Forming es tan dura la pieza resultante que el molde no lo puede hacer, los sobrantes y los taladros necesarios son cortados por un láser.
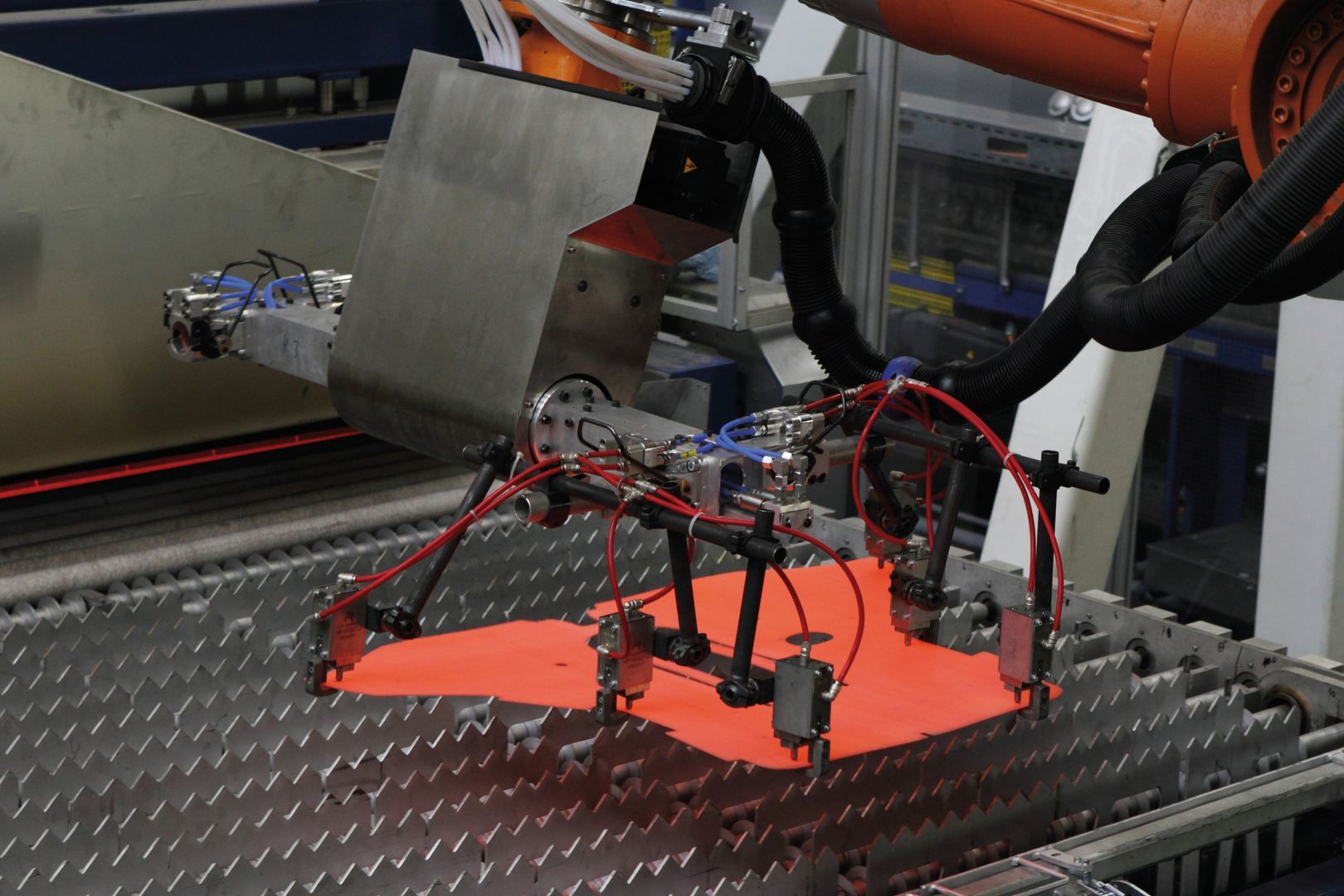
Como hemos dicho, la principal mejora de este proceso es la rigidez y el descenso de peso. En este caso damos un pleno en seguridad. Por un lado, la carrocería es más rígida, mejoramos la seguridad pasiva. Por otro lado, al reducir el peso, mejoramos la seguridad pasiva y la activa también. No hay que perder de vista que un coche ligero es más manejable que uno pesado y además frena antes en igualdad del resto de factores. Además, una vez producido el accidente, cuanto más ligero sea un vehículo menos inercia genera, por lo que es más fácil absorberla.
En cuanto a los inconvenientes son varios. En primer lugar, es más difícil producir estas piezas, necesitamos más energía, más maquinaria y más tiempo. Necesitamos precortar la pieza, calentar, prensar y luego recortar por láser. Sin embargo, estos factores se ven compensados por el aumento de dureza y reducción de peso, que aumentan la seguridad de los pasajeros y disminuyen la huella energética durante la vida del vehículo. Aquí un enlace a un vídeo de ejemplo.
Los pilares B
Esta técnica ya la utilizaba Mercedes en los pilares B de su Clase C desde 2007. Con esta técnica, dichos pilares pueden absorber mayores fuerzas y transferirlas a la estructura. En este caso, el pilar está formado de tres capas, una de ellas y el refuerzo están construidos en acero termoconformado.
En su nota de prensa del Golf VII, Volkswagen cuenta que decidió utilizar el conformado en caliente para aligerar peso y aumentar la rigidez sin recurrir al aluminio, ya que encarecería el producto. La novedad en este acero es que la chapa utilizada es laminada previamente de una manera muy especial, se le da un grosor variable en su longitud. Esto es, a base de la fuerza de unos rodillos se estira en las partes que no es necesario todo su grosor, lo que la hace más fina, y se deja más gruesa en las partes que sí. De esta manera se ajusta mucho más el peso. Según Volkswagen, este tipo de acero conformado en caliente es seis veces más resistente que el tradicional y cuatro más que el acero endurecido.
Aluminio
El aluminio es el eterno material del futuro. Si bien es muy utilizado en los vehículos de alta gama, sobre todo en deportivos que hay que aligerar, por el momento no ha llegado a las masas con éxito. El inicio en su uso en la industria automovilística es muy temprano, pero para modelos muy especiales, no para vehículos de masas. Curioso es el caso del Biscúter, microcoche construido enteramente en este material diseñado en Francia por Gabriel Voisin, de Avions Voisin en 1940 y fabricado en España en 1953. Pese a casos como éste, el aluminio sigue siendo un material exótico en los utilitarios. Se emplea en los bloques de algunos motores y en paneles de puertas y capós.El problema es que el precio sigue siendo elevado en comparación con el acero como para construir un utilitario totalmente en aluminio. También destacamos que el aluminio siempre se utiliza en aleación, puro es blando y poco resistente a la tracción -tampoco se utiliza el hierro, siempre se utiliza en aleación con carbono, a la que llamamos acero. La principal ventaja del aluminio es que pesa la tercera parte que el acero equivalente, lo que permite aligerar mucho el peso. En cuanto al precio hay una carrera constante entre productores de aluminio y productores de acero para que su producto sea el más competitivo.
Por el momento gana el acero por precio. Como uso en un automóvil diferente, se está utilizando el aluminio en el chasis del pickup Ford F-150, que aligera peso, pero con la pega de que su caja de carga se abolla sin remedio cuando dejamos caer ladrillos sobre ella. El otro gran problema del aluminio es que es más difícil de soldar, incluso hay aleaciones en la que no es posible. Es más, al igual que ocurre con el acero, el material del chasis de un vehículo no es el mismo en todos sus componentes, por lo que, al ser las aleaciones diferentes, aun es más complicada la soldadura.
Resumiendo, es un buen material, si estamos dispuestos a pagar por él y no vamos a echar ladrillos sobre él.
Entonces, ¿qué es mejor el acero o el aluminio?
Después de toda la discusión no llegamos a un acuerdo. Hemos visto el acero normal, el endurecido, el conformado en caliente, las aleaciones de aluminio y no sabemos cuál es el mejor. Tengamos en mente que los elementos que forman el habitáculo deben ser lo más rígidos posible, y los expuestos a las colisiones deben ser deformables de manera controlada, por lo que no necesitamos que todas las piezas estén formadas por el mismo material. La solución al problema es la que hemos visto en muchas de las imágenes anteriores, combinar materiales. Ya lo hemos visto en el pilar B de la imagen anterior que estaba compuesto de tres láminas y un refuerzo y sólo una de ellas y el refuerzo son termoconformados. En el caso del nuevo NSX, es todo de aluminio, pero hay de varios tipos según su uso.
En esta infografía se muestra todos los materiales utilizados en un Audi TT de tercera generación. Las piezas termoconformadas se utilizan en la parte inferior del chasis formando una H en el habitáculo con dos travesaños y el túnel central, además de dos largueros en el maletero. El resto de la parte inferior está construido en acero convencional. Los paragolpes, las estriberas y el exterior del arco del pilar A hacia el techo están construidos en aluminio perfilado. La unión del pilar A con el vano del motor y el techo con los pilares C están fabricados con aluminio inyectado. El resto del chasis está formado por láminas de aluminio estampado.
Muy bien, una estructura ligera y resistente, pero ¿cómo se une? Como hemos dicho antes, éste es el principal problema de todos estos nuevos materiales. Cuando es todo acero, y además del mismo tipo, es muy fácil soldar. Ya hemos dicho que el aluminio no es fácil de ser soldado. El acero termoconformado también es más difícil de soldar que el acero clásico. Ahora se complica un poco más ¿y el acero con el aluminio? ¿Y el aluminio inyectado con el acero?
Son muchas las combinaciones que se pueden dar, muchas se pueden soldar, otras no. Para poder unir piezas metálicas sin soldar tenemos una solución tan clásica como la de un Bugatti de 1936: utilizar remaches. En el caso del TT utiliza un láser para soldar el aluminio perfilado con otro aluminio y utiliza cuatro remachados diferentes, según el tipo de unión.
A la soldadura y el remachado se le une el uso de materiales no metálicos. En algunos casos las piezas son unidas por cola, o por una combinación mixta de varios tipos de unión. En la construcción del automóvil estos problemas se han resuelto, pero los hereda nuestro chapista. Con el acero podemos hacer prácticamente cualquier cosa, cortar, soldar, mecanizar, volver a cortar y soldar, golpear, pulir, estirar. Con otros materiales es más complejo, como hemos visto. Esto hace que, tras un accidente muy importante, sea muy difícil la reconstrucción de nuestro automóvil. Es un peaje que debemos pagar por tener una estructura muy rígida y ligera.
Un modelo avanzado en el uso de combinación de materiales es el propuesto en el prototipo Multi Material Lightweight Vehicle en 2013 por Cosma, la filial metalúrgica de Magna. Basándose en la plataforma de un Ford Mondeo/Fusion prometían un aligeramiento del 28 % sólo en el chasis, pasando de 350 kg a 252 kg. El chasis del modelo de serie utiliza en bruto un 4 % de acero termoconformado y el resto de acero normal. En el prototipo MMLV utiliza un 7 % de acero termoconformado, un 64 % de aluminio y un 29 % de acero.
Poco a poco, el uso de estas técnicas y materiales van de los modelos Premium hasta los utilitarios, cuando el precio lo permite. Como ya comenté antes, el uso del aluminio en el 100 % del chasis queda un poco lejos del utilitario de hoy en día. Sin embargo, prácticamente todos los vehículos nuevos aparecen con multitud de materiales y de técnicas que ayudan a ser seguros y ligeros con un precio ajustado. Esta tendencia a utilizar múltiples técnicas para un mismo coche se va a mantener en los próximos años, incluso aparecerán otras nuevas que se irán añadiendo.
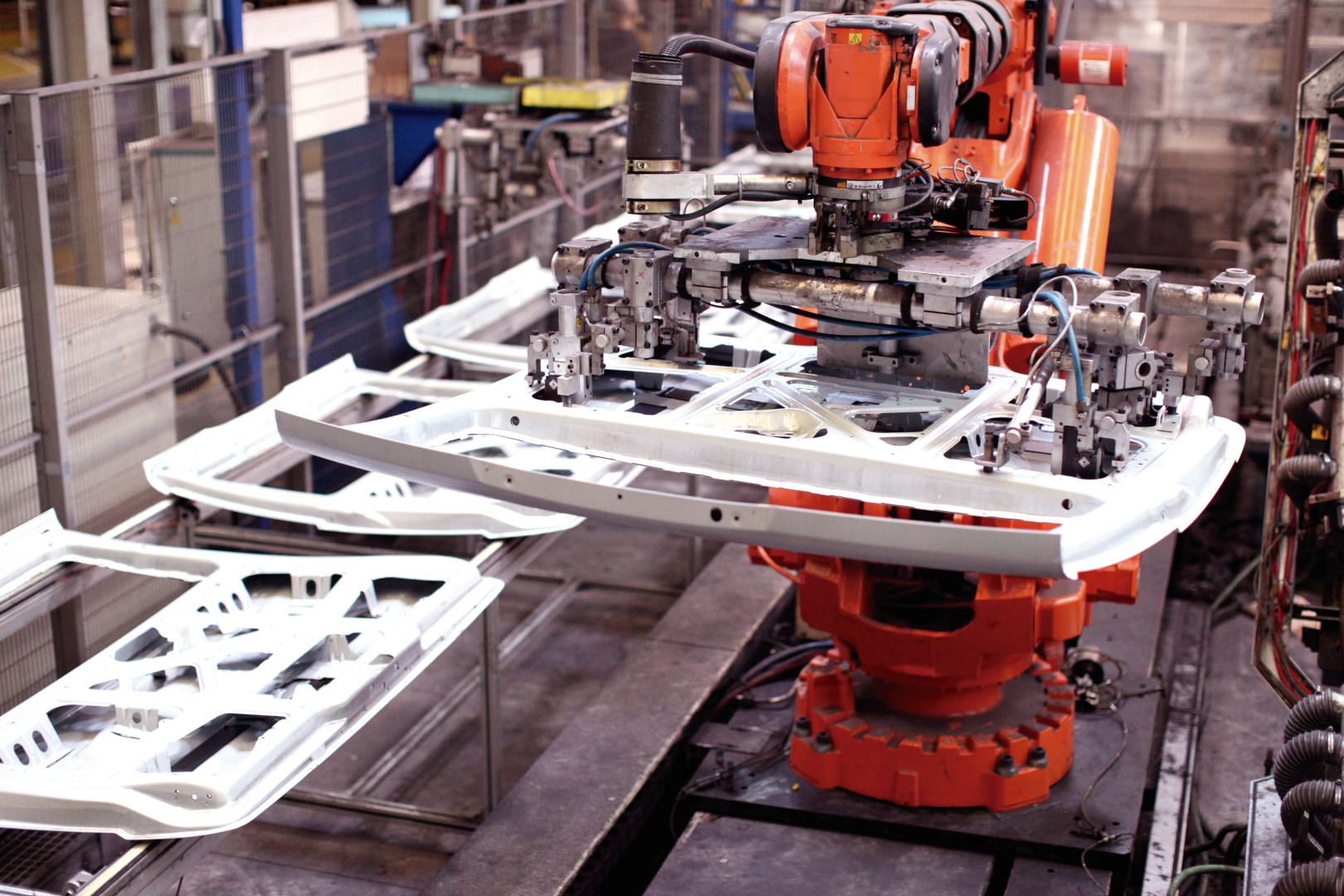
Esta obra, cuyo autor soy yo mismo, se publicó el 3 de diciembre de 2016 bajo una licencia de Reconocimiento 4.0 Internacional de Creative Commons.
J.J. López
Portador del contagioso virus de los coches desde los once años. Ingeniero en informática, programador de robots y visión artificial que lo piensa todo en coches. Amante del arte, técnica y tecnología en movimiento, esto es, apasionado incondicional del automóvil.Muy buen artículo, excelente en realidad! Un placer leerlo.
¡Impresionante artículo! Estoy admirado y lamento no haber conocido antes este sitio.
Nos alegramos de que te guste y esperamos que vengas más por aquí. Sé bienvenido.