En la serie de artículos anteriores vimos cómo crear un chasis a partir de unas bobinas de metal. Después de construirlo, lo protegimos, le dimos color y lo barnizamos. Ya tenemos nuestro chasis preparado para entrar en la línea de montaje.
En esta nueva etapa la presencia de robots es mucho menor, tomando mucha más relevancia el factor humano. Antes de seguir con el montaje de nuestro automóvil, permitidme hacer un inciso.
En este artículo veremos tres puntos con la intención de aclarar dudas de los próximos artículos. Estos temas serán las principales las ventajas e inconvenientes de realizar el montaje de un automóvil a robot o a mano, un apunte sobre el sistema eléctrico y un nuevo tipo de dispositivo: el vehículo autoguiado.
¿Es mejor la persona o el robot?
En los procesos anteriores hemos visto aparecer más robots que personas. Esto es debido a que las piezas a manejar son grandes y con bordes afilados, mientras por otro lado los procesos desprenden gases y otras partículas nocivas para la salud del operario. En los procesos que vamos a ver no suele haber sustancias tóxicas y, si bien se mueven cargas pesadas, disponemos de sistemas de ayuda a mover pesos llamados manipuladores “ingrávidos”.
Estos manipuladores están compensados con la carga que van a llevar, de manera que el operario no tiene que hacer un esfuerzo para levantarlos o mantenerlos. Este trabajo lo podría hacer un robot sin necesidad de otro manipulador, digamos que un robot es un manipulador inteligente.
Encajado de piezas
Los puntos más críticos para un robot en el montaje son dos: el encajado y la cantidad de piezas diferentes. Hasta ahora hemos manejado piezas metálicas, que son fuertes y repetitivas; en esta sección empezamos a ver piezas de plástico, esto es, que contienen carbono, es decir, orgánicas o sea que estas piezas tendrán variaciones. Si después de cada paso teníamos un control de calidad para ver si las piezas metálicas conformadas en una prensa y soldadas dentro de un molde, porque puede haber variación, ¿qué será de las piezas plásticas donde la variación es segura?
Las piezas plásticas se hacen por inyección, básicamente se inyecta plástico fundido en el interior de un molde, se le da un tiempo de formación, se enfría, se abre el molde y se extrae.
Aunque siempre sea el mismo molde, pequeños cambios en los componentes de la materia prima o en las temperaturas afectan al tamaño y la forma de la pieza acabada. Esto es, cuando hablamos de piezas plásticas damos por hecho que no van a ser iguales. Las daremos por buenas cuando estén dentro de tolerancia, que no quiere decir que sean exactamente iguales.
El punto crítico es el encajado de las piezas plásticas. Las piezas metálicas se unen a base de aplicar fuerza cuando soldamos, roscamos o remachamos. En las piezas plásticas debemos actuar de otra manera pues no les podemos aplicar tanta fuerza o las romperemos.
Os pongo un ejemplo con un objeto cotidiano. Supongo que habéis tenido un rotulador permanente en las manos ¿habéis leído que pone press to click? El rotulador indica que estará totalmente cerrado cuando oigamos ese sonido. Ese movimiento para encajado, que lo hacemos tan fácilmente, es muy complejo hacerlo con un robot de los que hemos visto hasta ahora. Es más, si es un rotulador sin tope que haga clic es todavía peor, sería tan fácil dejarlo abierto sin presión como reventarlo por presión excesiva.
Si todas las puntas y capuchas de nuestros rotuladores fueran exactos, sería muy sencillo programar un movimiento hasta la cota necesaria, pero no podemos confiar en que todas las piezas sean exactas. Está claro que no necesitamos un robot para cerrar rotuladores, pero podemos extrapolar nuestra experiencia a piezas más grandes.
Si bien la visión artificial es muy operativa, con el tacto aun estamos en pañales. Pensad que con nuestras manos asimos con la fuerza necesaria para que no se nos escape un objeto y a la vez lo sopesamos, equilibramos, analizamos su textura, maleabilidad y temperatura, entre otros; no está nada mal. Sobre estas líneas podéis ver un prototipo de robot de Toyota que mantiene una copa de vino sin derramar ni una gota aunque le golpeemos en el codo.
No es importante la forma que tiene, la innovación está en la pieza electrónica que vemos a su lado. Es una minibáscula que informa al controlador del reparto de fuerzas sobre su superficie. Esta pequeña báscula indica al controlador el par mecánico que estamos realizando, este sería el camino a seguir, muy complejo por el momento.
Polivalencia de la mano humana
El otro inconveniente es la multitud de piezas que hay que manejar. Imaginaos la cantidad de conectores que tiene un salpicadero actual (más adelante lo veremos), tendríamos que trabajar con robots con pinzas preparadas para cada uno de esos conectores, además de atornillador y otras herramientas.
Si queremos que un robot manipule todas estas piezas debemos crear una pinza supercompleja para que las coja todas, una pinza que pueda coger cualquier cosa sin estar optimizada para ninguna o intercambiar la pinza para cada una de las piezas que necesite manipular.
Como os habéis dado cuenta, la mano humana es un gran invento que aun no ha sido superado en polivalencia. Ya os lo dije al principio de esta serie: la segunda máquina que mejor se adapta es el robot, la persona es la primera.
El principal problema humano
Nos despistamos con facilidad, sobre todo en esa franja horaria que va del lunes por la mañana al viernes por la tarde; si trabajamos a turnos ese tiempo se amplía. Ninguna persona es infalible, por lo que hay que idear sistemas para prevenir de los errores humanos.
El primer fabricante que ideó un sistema metódico para prevenir estos errores fue Toyota y forma parte de su sistema (Toyota Production System). En Toyota tenían un problema con una pieza que se montaba con dos muelles. El operario cogía un par de muelles del cajón, donde había cientos, los colocaba dentro de la pieza y luego la cerraba con su tapa correspondiente. Si el operario dudaba si había puesto los dos muelles, no podía averiguarlo de un simple vistazo, pues ni se podía ver a través de la pieza ni podíamos saber si nos faltaban un par de muelles de los cientos que quedaban en el cajón.
La solución de Toyota fue añadir una bandeja intermedia en la que el operario depositaba todos los componentes necesarios antes de montarlos. Cuando una nueva pieza se posicionaba delante de él colocaba los muelles y las tapas que previamente colocó en la bandeja intermedia. Si acaso dudaba de si había puesto los muelles o no lo podía comprobar en la bandeja, pues no debía quedar ninguno. Al alejarse la pieza montada volvía a colocar componentes nuevos en la bandeja. Este sistema es llamado poka-yoke y significa “a prueba de errores”.
Un ejemplo de poka-yoke lo tenemos en algunas impresoras de casa: si no queda tinta nos avisa, los cartuchos de tinta sólo se pueden colocar de una manera concreta y si no son del tipo adecuado nuestra máquina dará un error y no podremos imprimir. Otros ejemplos los tenemos en los conectores USB y tarjetas de memoria, que sólo nos permiten ponerlos de una manera.
En la imagen superior vemos cómo un operario de FCA en Sterling Heights monta diferentes piezas que van a ser soldadas. Si os fijáis en la pieza superior se puede apreciar que se centra con un cono que hay en el molde. Este componente es el que garantiza que la pieza está en su sitio.
La manera de trabajar sería mas o menos como sigue. Una vez que están todas las piezas montadas pulsará un botón y se cerrarán los cepos neumáticos. Si después de esta maniobra el sistema detecta que están todas las piezas y todos los cepos cerrados correctamente, todas las balizas de la parte inferior se pondrán en verde indicando que está todo bien. Si faltase alguna o no estuviera bien puesta, se encenderá el color rojo. De esta manera nos dice que no está bien montado y qué pieza falta.
Todos los fabricantes utilizan sistemas similares en todas las operaciones. Si la pieza en cuestión es subcontratada, se exige que se utilice su sistema a prueba de fallos, no toman como bueno “mis operarios nunca se equivocan”. Para que les quede claro, si se encuentra un chasis defectuoso por una pieza subcontratada, al externo no se le descuenta lo que el valor de esa pieza mal hecha, si no la reparación completa de ese chasis.
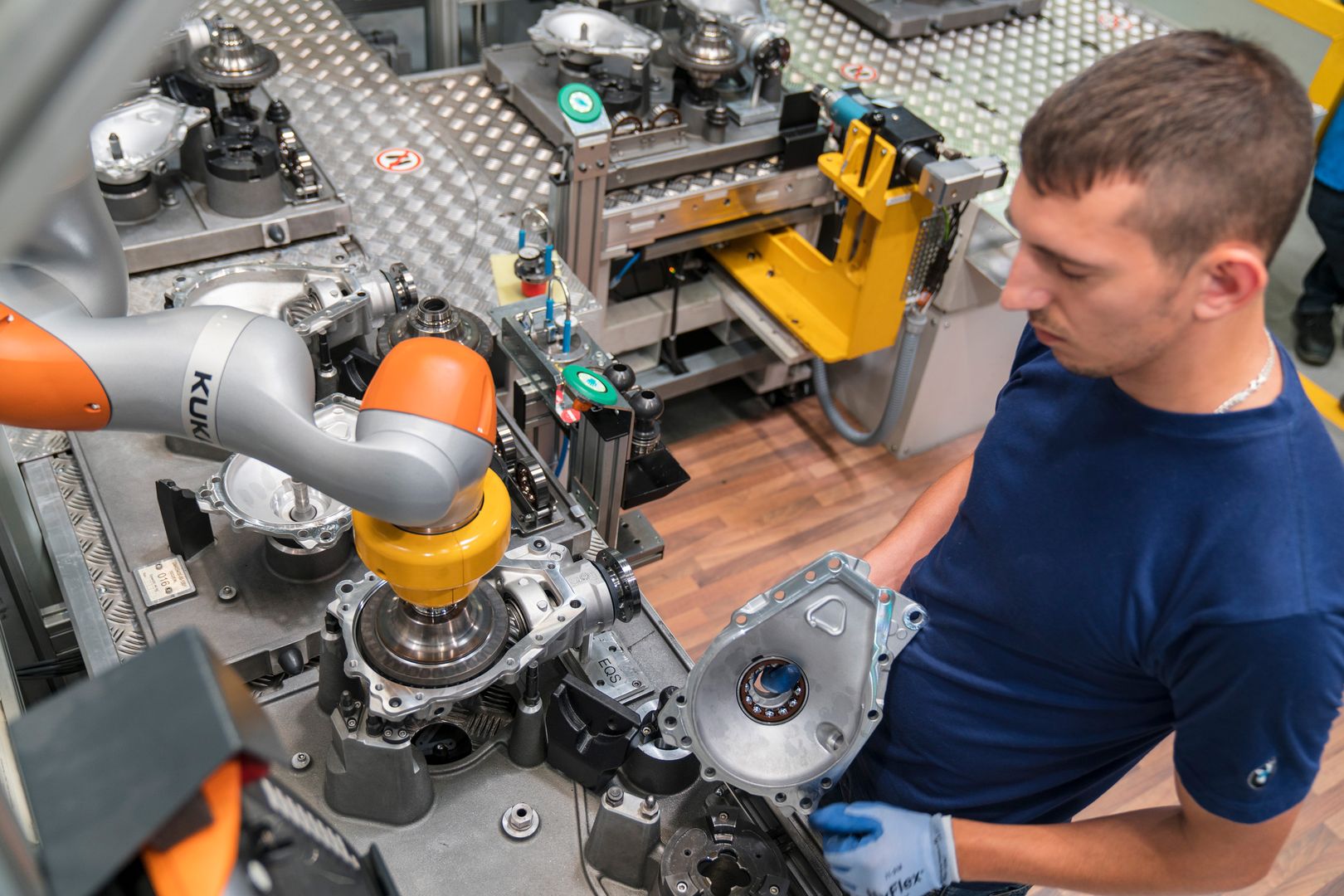
Robots colaborativos
Un nuevo tipo de robots ha surgido recientemente, son los llamado “colaborativos”, pues no necesitan barreras de seguridad y pueden trabajar al lado del operario. Se están introduciendo poco a poco, ya que de momento no son tan rápidos como los robots tradicionales.
En la imagen vemos a un robot de Kuka que ayuda a un operario a montar un diferencial de BMW sin barrera de por medio, ni física ni fotoeléctrica. En caso de que el robot detecte que hace un movimiento con más par de lo normal parará en seco, pues lo más probable es que haya un objeto extraño de por medio.
Observad que en la bandeja vienen todos los componentes para el montaje de la pieza: las dos mitades de la carcasa, el diferencial como tal y los dos rodamientos a colocar en las carcasas. Es otra representación del sistema poka-yoke, pues están todas las piezas necesarias y si alguna no la hemos colocado, quedará a la vista.
Hombre contra máquina
¿Qué trabajador es mejor entonces, el hombre o el robot? No hay una respuesta clara, como hemos visto los robots son mejores con cargas grandes, en entornos nocivos y con trabajos muy concretos. El hombre es mejor cuando hay muchas piezas diferentes, como control de calidad y en procesos muy delicados, como el pulido y el encajado de plásticos.
De esto se deduce que el mejor trabajador sería la unión de la fuerza de un robot con la pericia de una persona, parece ciencia ficción, pero no, es sólo ciencia. Ford ha dado el primer paso en “robotizar” a sus empleados. Después de probarlo en las plantas de Míchigan, Ford ofrece a sus operarios que trabajan por encima de su cabeza un exoesqueleto robotizado.
Este exoesqueleto se sujeta al torso y tiene dos brazos articulados que se sujetan a los del operario. Este exoesqueleto sigue la posición de los brazos, de manera que el operario no tiene que emplear toda su fuerza cuando trabaja hacia arriba.
Conclusión: ¿por qué elegir? Nos quedamos con los dos.
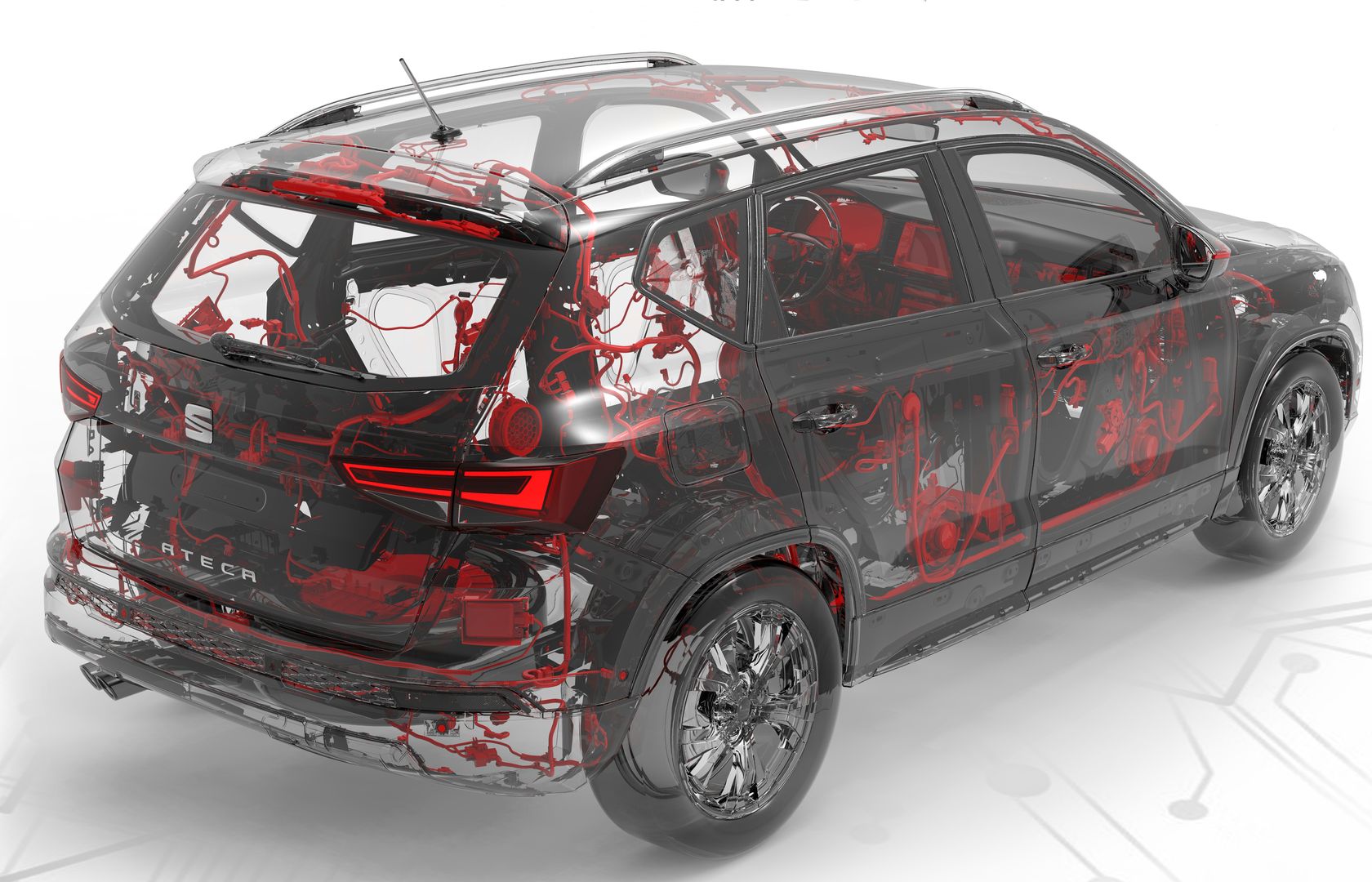
Montaje del sistema eléctrico
Ahora que ya tenemos claro que robots y operarios se complementan en el montaje de nuestro coche, vamos a ver los puntos más importantes del sistema eléctrico de nuestro vehículo a la hora de ser montado.
Los automóviles están cada vez más electrificados, y no sólo los híbridos o eléctricos, los vehículos actuales tiene cables por toda su estructura. Pensad que un volante de hoy en día tiene tanta electrónica como todo el salpicadero de algunos modelos de hace 15 años y más que todo el vehículo de hace 30.
Otro tanto ocurre con el retrovisor, al principio era solo un espejo, luego se le añadieron motores para ajustarlos desde el interior, más tarde calefacción para forzar el desempañado, después un sónar y una pequeña luz para indicar que hay algo en el ángulo muerto, finalmente una cámara para obtener una representación de 360 º de nuestro automóvil.
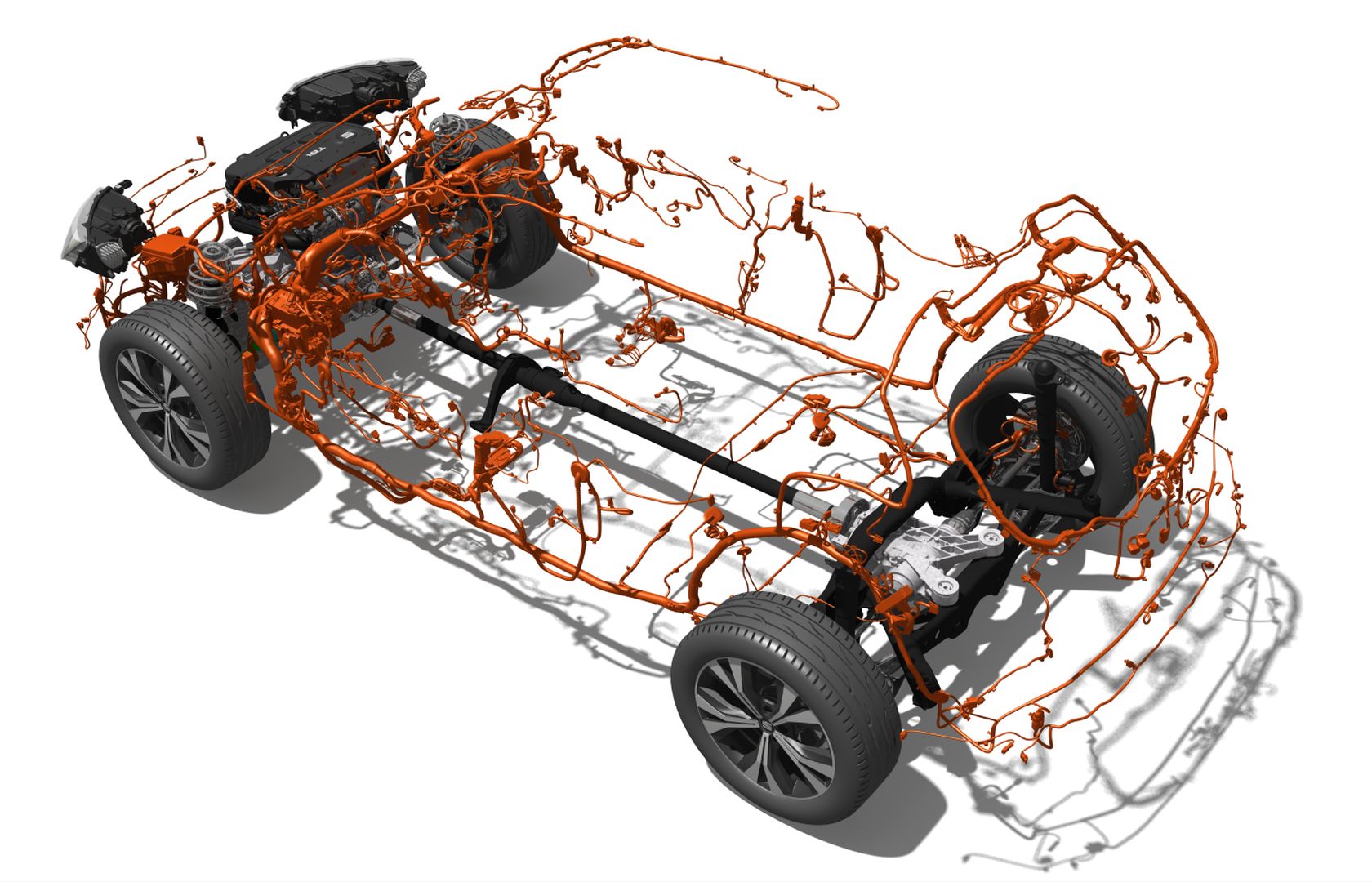
Como ejemplo de electrificación tomamos el Ateca. Este SUV C tiene un total de 1.350 cables que van de un grosor de 1 mm hasta más de un centímetro, sumando un total de 42 kilos de cobre; puestos en línea sumarían 2,2 km. Estos cables se unen a conectores y se agrupan en más de 30 mazos. La parte del tablero frontal es donde más se concentran. No sólo tenemos que pensar en estos cables, también debemos tener en cuenta que entre centralitas y sensores tiene más de 100 dispositivos. Como podéis pensar, cuando se diseña el sistema eléctrico de un automóvil, además de que funcione correctamente, debe ser diseñado para que su montaje sea lo más fácil posible.
Hay dos problemas principales en la instalación del sistema eléctrico que hacen más práctica a la persona que a un sistema por robot. Por un lado hay muchísimas opciones, en el caso del Ateca son unas 12.000 posibilidades de cableado, según las opciones que seleccionemos en su compra. Deberíamos programar todas las opciones en nuestro posible robot. Por otro lado, los mazos de cables son un objeto quasi vivo, cuando cuelgan no tienen una posición concreta, se puede balancear y el conector no está siempre con la misma orientación
Los cables se agrupan en conectores polarizados que solo encajan de una forma para reducir los riesgos de un montaje incorrecto
Para que un robot pudiera coger esos cables necesitaríamos una cámara de visión artificial o colocarlos siempre igual sobre un soporte, otra complicación añadida. También ocurriría como hemos comentado antes: tendríamos que diseñar una pinza capaz de asir perfectamente todos esos conectores. Queda claro que la mayor parte de los cables serán colocados a mano. En artículos sucesivos veréis que el Ateca no es una excepción, los coches actuales están muy conectados y en casi todos los pasos hay cables que conectar.
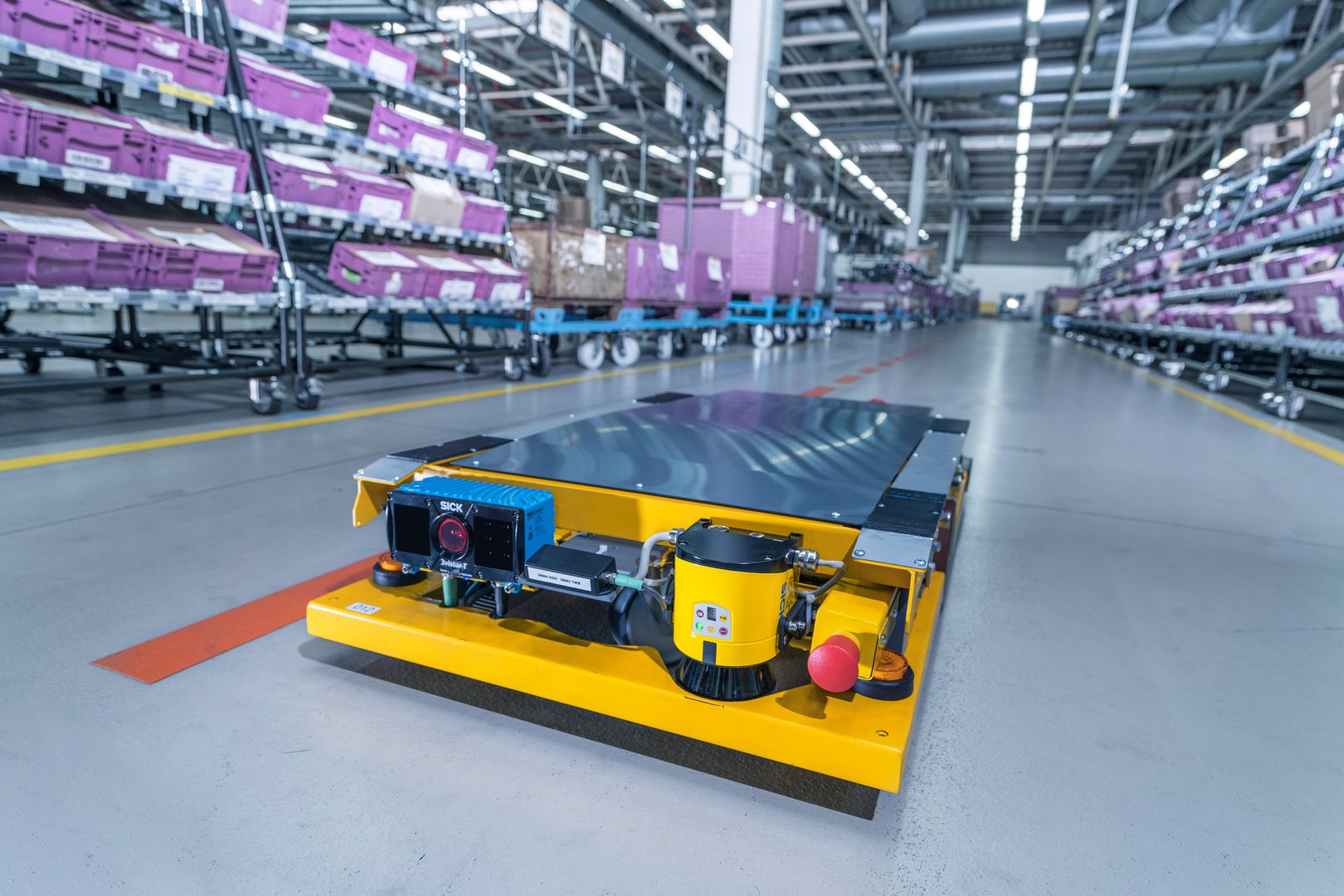
Vehículo auto guiado
También conocido por sus siglas en inglés AGV (Automatic guided vehicle). Son carros sin conductor que se mueven libremente por la planta. Si bien la carrocería completa se suele mover por la cadena de la línea de producción, las piezas pequeñas se suelen llevar en este tipo de carros.
Estos carros eran llevados a mano primero, hoy en día se utilizan los AGV de manera que se mueven libremente sin tener un carril físico. Digo físico porque los AGV más básicos se guían mediante balizas en el suelo, por ejemplo imanes, de esta manera continúan el camino indicado. Los hay más sofisticados con balizas visuales o láser, incluso se les llega a considerar robots de transporte. Como elementos de seguridad suelen tener fotocélulas de proximidad y sensores de presión, de esta manera se detienen si encuentran algún obstáculo en su camino. El ser su trayectoria fija y la velocidad reducida, son mucho más sencillos que los automóviles autónomos.
Son muy prácticos porque están conectados al sistema central, que es el que controla que cada carro esté en el sitio adecuado en el momento preciso. En este mismo artículo hemos visto un ejemplo en el montaje de la suspensión trasera de un BMW serie 5. Parece que el operario está trabajando sobre una plataforma cuando realmente es un carro autoguiado; al fondo de la imagen podemos ver otros carros parados en fila.
En el próximo artículo volveremos a la línea producción, para ver cómo los operarios, con ayuda de robots, tanto clásicos como colaborativos y AGV, montan las piezas de nuestro coche, que lo tenemos un poco olvidado.
J.J. López
Portador del contagioso virus de los coches desde los once años. Ingeniero en informática, programador de robots y visión artificial que lo piensa todo en coches. Amante del arte, técnica y tecnología en movimiento, esto es, apasionado incondicional del automóvil.COMENTARIOS