Hace ya siete entregas vimos cómo entraban bobinas de metal a nuestra planta y después de varios procesos de conformado y ensamblado se convierten en un chasis. Ese chasis se protege y pinta. Después se le añaden todos los componentes necesarios para convertirlo en un automóvil en varias etapas siendo la más importante el “matrimonio” que es donde se unen chasis y grupo propulsor en uno.
En la entrega anterior dejamos a nuestro automóvil totalmente construido a falta de un sólo paso: el acabado.
Antes de ver este último proceso, comentaremos tres puntos que hemos visto de pasada en el resto de artículos: fabricación de plásticos, el control de calidad y la evolución de los medios en los trabajos.
Elaboración de plásticos
Hemos hablado mucho de metales a la hora de fabricar un automóvil, sin embargo, el plástico es cada vez más común en la elaboración de un automóvil. Con los plásticos pasa como con los metales, al principio nos parecen todos iguales, pero a poco que investiguemos nos damos cuenta de que no es así.
Repasemos algunos de ellos. Tenemos plásticos para tapar componentes dentro del vano del motor y deben soportar bastante temperatura. Los exteriores no tienen por qué soportar tanta temperatura, pero sí deben resistir los rayos ultravioleta. El material del salpicadero debe ser blando para que los pasajeros no se hieran en caso de colisión.
Recordad que la mayoría de los componentes de un vehículo deben ser reciclables, tanto metales como plásticos. Para reciclar plásticos se trituran y se les añade tinte negro, aunque casi siempre se llega a ese tono por la mezcla de colores. Podríamos decir que todos los plásticos negros proceden de material recuperado. El resultado no es estético pero sí es práctico por lo que se suele utilizar en piezas no expuestas.
En el caso concreto de BMW presume con su i3 de que recicla plásticos de las playas para sus paneles plásticos y utiliza ropa reciclada para fabricar paneles fonoabsorbentes, paneles interiores y asientos. También nos informa de que utiliza fibra de ceiba (Ceiba pentandra) para la cubierta de los asientos y fibra de kenaf (Hibiscus cannabinus) en el interior de las puertas y guarnecidos.
La manera de fabricar cualquier plástico es la siguiente: la materia prima viene en forma de gránulos, como hemos visto en la imagen anterior. Estos gránulos se inyectan con un husillo en espiral que va calentándolo. Este plástico fundido llega al interior de un molde caliente, después de un tiempo ese molde se enfría con agua para ayudar a que se endurezca la masa. Pasado un tiempo el molde se abre y se extrae la pieza. En el proceso de inyección se puede añadir fibra para reforzarlo si su aplicación lo requiere, esta fibra puede ser hasta fibra de carbono. También se puede inyectar una capa de pintura o brillo para hacerlo más atractivo. Por último, también se pueden insertar tuercas roscadas o tornillos, de esta manera la pieza fabricada puede ser atornillada firmemente.
La extracción de la pieza puede ser por expulsión y gravedad si es pequeña. En caso de que sea grande o delicada, se suele utilizar un robot, pues el molde alcanza temperaturas de 150º y la presión de cierre del molde suele estar entre 100 y 200 toneladas. En la imagen anterior podemos ver una composición de la secuencia de la extracción de un salpicadero de Fiat Panda. El robot utilizado es un Comau, de fabricación italiana.
Control de calidad
Cuando hablábamos de las piezas conformadas decíamos que se medían para hacer el control de calidad, pero ¿cómo se hace? Es muy fácil medir la longitud de una pieza recta, pero un automóvil rara vez utiliza piezas totalmente rectas. Lo usual es que sean curvadas, tridimensionales y con varias superficies. Para saber cómo se miden, debemos regresar a la etapa de diseño y desarrollo.
Cuando un modelo se lanza a producción se debe comprobar que lo fabricado coincide con el modelo diseñado en cuanto a forma. Otra cosa que se debe vigilar es que sea simétrico y que las piezas encajen correctamente, esto es, la parte derecha debe ser idéntica a la izquierda y la separación entre paneles debe ser la adecuada. Cuando estas separaciones son mínimas e iguales, da la impresión de que el automóvil es un bloque robusto y lo hace más atractivo.
Para comprobar que esto es así se construye una estructura en aluminio en el que se acoplan todas las piezas. Si las piezas no casan correctamente se corrigen los moldes si es necesario. Las piezas se pueden medir tanto por toque con un palpador con punta de rubí o con visión artificial.
Basándose en las medidas obtenidas se crea un molde macizo sobre el que se colocarán las piezas a chequear. De esta manera se comprueba si las piezas que se están fabricando entran en medidas o no. En la primera imagen vemos un grupo de especialistas que comprueba un techo practicable en un molde de un Chrysler 300.
Otra manera de comprobar las medidas es por visión artificial, como vemos en la siguiente imagen en la que un robot porta una cámara para comprobar si el chasis de un Mini es correcto.
Las mediciones se hacen con piezas seleccionadas de manera aleatoria, cada cierto número que se producen. De esta manera nos aseguramos de que todas las piezas se están fabricando dentro de tolerancias. En caso de un resultado negativo, se busca el motivo que produce esa desviación y se corrige.
¿Por qué siempre hay una persona al frente de un control de calidad? Si sólo hubiera que medir en una cota, como en el corte de tubos de nuestro primer artículo, no sería necesario un técnico cualificado, sólo necesitaríamos una plantilla para comprobar que la medida es correcta. Generar un sistema automático de control con un problema tan concreto como el anterior es sencillo, pero un automóvil es mucho más complejo.
Imaginemos el diseño de un sistema para comprobar que la puerta de la guantera encaja con seguridad. Podríamos medir por visión artificial que está perfectamente centrada, pero ningún sistema nos podrá decir que el clac al cerrar es el correcto. Un sistema se puede preparar para que responda a un número finito de comprobaciones, puede ser muy alto, pero es finito. Una persona puede ver errores aunque no estén detallados.
Medios en el trabajo
Como en todos los aspectos de la producción, los medios en el trabajo han evolucionado y no sólo por la automatización y de la aparición de robots. Las protecciones de los operarios han cambiado muchísimo.
Sobre estas líneas vemos un montaje de cómo se pintaba a mano en los años 50 y en la actualidad. El trabajo es más o menos el mismo, pero en la foto más vieja no existen los equipos de protección individual (EPI). Sabéis por los cursillos de prevención en el trabajo que se debe utilizar los EPI si no se pueden aislar los procesos o máquinas peligrosas. La otra parte de la foto es un operario que pinta el techo de una unidad conmemorativa de Mini, por lo que se pinta a mano, no en serie.
Otro de los puntos que han mejorado con el paso de los tiempos ha sido el de manipulación de cargas pesadas. Los manipuladores ingrávidos se utilizan para que el operario no tenga que manejar cargas pesadas, sólo dirigirlas.
Lo mismo ha ocurrido con la soldadura. Ahora son los robots los que mueven las pinzas y se tragan tanto las chispas como los vapores generados. Todavía se suele soldar a mano en la fabricación de los automóviles, pero con otros equipos de soldadura y de protección, de manera que el equipo sea más liviano y los trabajadores no corran peligro.
La definición más corta de ergonomía es que el puesto de trabajo se adapte a la persona y no la persona al puesto de trabajo. En estos artículos hemos visto varias formas de facilitar el trabajo a los técnicos, el más espectacular es el exoesqueleto de torso, que ayuda a los brazos en posiciones altas. Este sistema ya se empieza a introducir en plantas de BMW, Ford, Mercedes-Benz y de VAG, lo que hace pensar que se normalizará con el tiempo.
También hay otros sistemas de exoesqueleto que hace las veces de silla portátil sin necesidad de llevarla a cuestas. La solución más compleja no tiene por qué ser la mejor, simplemente añadiendo una silla móvil, ya sea con un brazo giratorio o en un carril, hace el trabajo mucho más fácil para los instaladores.
Ahora sí, volvemos a la línea de producción, que nuestro automóvil está esperándonos en el último puesto.
Acabado
Ya tenemos nuestro automóvil totalmente montado y sólo nos queda un paso ¿cuál será si está todo montado? En todos estos artículos hemos visto que después de cada proceso hay un control de calidad. Cuando acaba el montaje, hay un control de calidad final que es exhaustivo y en varias materias.
En las imágenes anteriores podemos ver la línea de acabado de dos series muy diferentes del Mini. Las comprobaciones básicas son exteriores: pintura, puertas, y capós. A lo hora de comprobar los componentes más complejos, en el Austin prácticamente con que arranque el motor, frene y encienda las luces podríamos decir que ya está todo bien. En la versión BMW tenemos muchas más comprobaciones, además de lo anterior tenemos las centralitas del motor, servodirección, ABS, control de tracción, climatización, ordenador de a bordo, …. Por otro lado, todos los accionamientos: mandos de puertas, de elevalunas, de retrovisores y sigue la lista.
A medida que subimos en la categoría premium el automóvil tiene más componentes y más equipamiento que hay que revisar. Este es el caso del BMW 330, que aquí vemos en un control de tracción, muy importante para un coche de sus prestaciones.
Además del control de tracción debemos comprobar que los frenos funcionan a la perfección, al igual que la dirección. La llegada de las nuevas centralitas hace que muchos de las pruebas se puedan hacer más fácilmente.
En la siguiente imagen del chequeo del Audi Q2, esta prueba nos dice que este vehículo es un 4×4 pues tiene rodillos en ambos trenes. Cualquier problema encontrado hará que se lleve la unidad al puesto correspondiente para revisar cuál es el problema.
La prueba que siempre se hace a todos los modelos, independientemente de su tipo de motor, de si es generalista o premium es la inspección visual de la pintura y de todos los componentes a mano. No debe haber ninguna irregularidad en su superficie, en caso de encontrar alguna imperfección se llevará a pulir.
Siguiendo con las pruebas, cualquier puerta debe abrir y cerrar correctamente (incluyendo la de la guantera), deben funcionar las luces, los elevalunas y cualquier dispositivo que os imaginéis.
Realmente conectamos las centralitas al ordenador evaluador y éste nos va diciendo qué debemos hacer: pisar el freno, acelerar, encender tal dispositivo, … Todos estos valores se quedan grabados en el sistema y la unidad la damos por buena si responde positivamente a todas las pruebas.
Fin de línea
Cuando la unidad se acepta como correcta se saca de la línea de producción. Por fin nuestro bebé se ha hecho adulto, ¡se mueve! Sólo queda llevarlo a expediciones para que nos lo envíen a casa.
Sobre estas líneas algunos de los modelos que han sido protagonistas de esta serie de artículos, una vez han sido terminados.
Hemos visto turismos, todoterrenos, monovolúmenes, SUVs, deportivos, pick-ups e industriales. Sus motores han sido eléctricos, de pila de hidrógeno y, por supuesto, de combustión interna.
Hemos visto plantas de vehículos en EE. UU., México, Canadá, China y Japón. Dentro de Europa hemos visto plantas en España, Francia, Italia, Reino Unido, Rusia y Alemania, además de otros países.
Todos los automóviles que hemos visto han sido creados con la unión de piezas procedentes de grandes rollos de metal. Con esas piezas se crea el chasis, que luego es protegido y pintado. Las puertas son separadas para montarse por separado.
A este chasis se le añaden componentes eléctricos, guarnecidos, salpicadero, asientos y puertas. El propulsor, suspensiones y transmisiones se unen todos juntos al chasis en un proceso llamado matrimonio. Después de completar este proceso se añaden el resto de los accesorios.
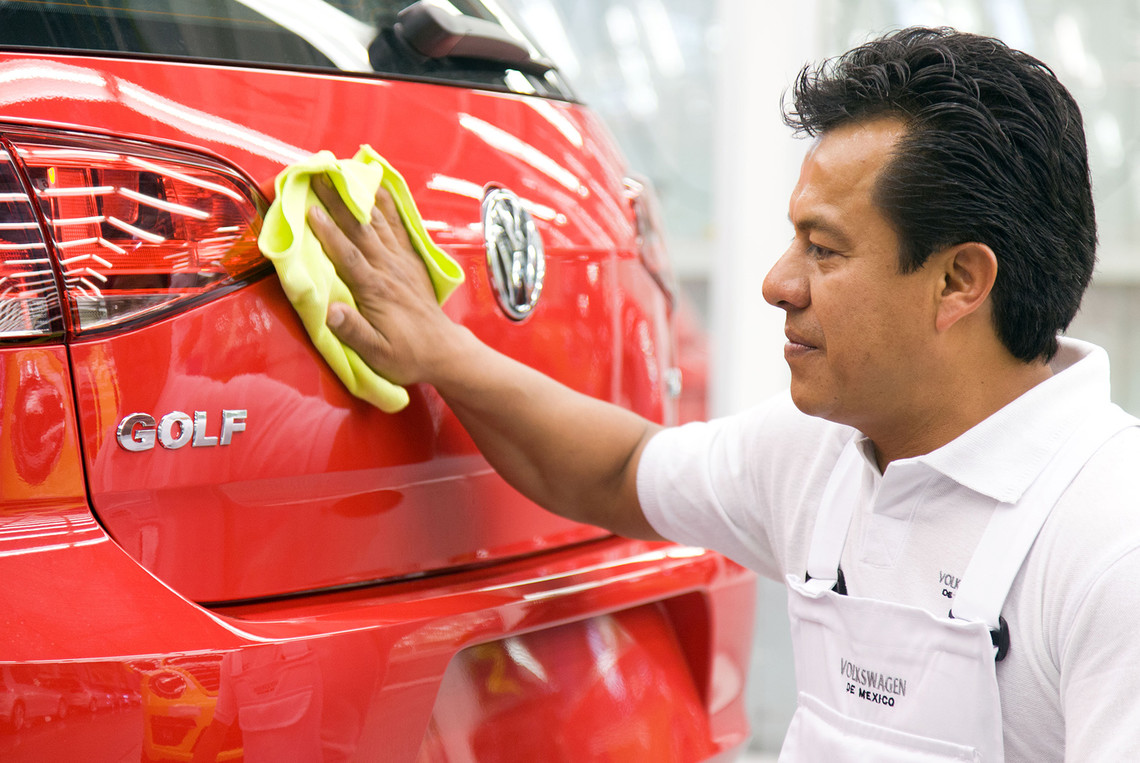
Hay que revisar todos los procesos después de su realización y al final de la línea hay que revisarlo todo. Hay que comprobar lo que es técnico como el frenado, el encendido de las luces y la convergencia de las ruedas. También hay que comprobar lo que no es técnico, como el aspecto de la pintura o el ruido al cerrar las puertas.
Para comprender mejor estos procesos hemos visto numerosos modelos de automóviles, tanto actuales como de hace unos años o incluso clásicos. De esta manera hemos podido comparar la evolución tanto de técnicas como de procesos y de materiales.
No sólo hemos visto la evolución de los automóviles y su fabricación, también hemos visto la evolución en el trabajo de los operarios. El trabajo en la línea de producción ha pasado de ser todo manual para tener cada vez más ayuda. Parte de esa ayuda viene de unos brazos automatizados, llamados robots, que nos ayudan a mover las piezas pesadas y a realizar los procesos más nocivos.
En la actualidad se han creado robots colaborativos para poder trabajar sin barreras cerca del operario. Y otra modificación que hemos visto son los exoesqueletos para ayudar a las tareas pesadas de los operarios. Estos dispositivos ya funcionan en las plantas de BMW, Ford, Mercedes-Benz y también están en prueba en plantas del grupo VAG.
Después de tantas mejoras en robótica y visión artificial hemos visto que la mano de obra sigue siendo necesaria e indispensable en muchísimos procesos.
Algunos de los modelos que hemos visto tienen más características RACER que otros, pero el espíritu se lo pone el conductor. ¿Con qué modelo os quedáis después de haber visto cómo se fabrica un automóvil en serie?
J.J. López
Portador del contagioso virus de los coches desde los once años. Ingeniero en informática, programador de robots y visión artificial que lo piensa todo en coches. Amante del arte, técnica y tecnología en movimiento, esto es, apasionado incondicional del automóvil.Gran serie de artículos. Muy interesantes.
Muchas gracias y a seguir haciendo el gran trabajo que hacéis.