Dentro de nuestra serie de reportajes abordando los diferentes sistemas que componen un automóvil, ya hemos visto algunas cosas sobre su diseño, la suspensión y sus tipos, el sistema eléctrico (parte I y parte II), el diferencial, el sistema de iluminación e incluso como se produce un automóvil en serie. En esta ocasión vamos a tratar de manera muy resumida uno de los sistemas fundamentales para la seguridad y control de un vehículo como es el sistema de frenos.
En esta primera parte veremos la historia de los frenos y en qué tipos se dividen. En la siguiente entrega nos centraremos detalladamente en cada componente de un sistema de frenos actual, algunas directrices de diseño y el caso especial del sistema de frenos en coches eléctricos/híbridos.
El sistema de frenos es necesario en cualquier vehículo a motor para reducir su velocidad de manera segura. Su principio de funcionamiento se basa en transformar la energía cinética (movimiento) en energía térmica (calor) mediante el rozamiento de una pieza fija contra otra móvil. Pero antes de meternos en harina, veamos cómo hemos llegado a los sistemas de frenos actuales echando la vista atrás en su historia.
Un poco de historia de los frenos
Para mantener bajo control cualquier cosa que se mueva en tierra básicamente necesitamos de un sistema que controle la dirección (izquierda/derecha) y la velocidad (acelerar/decelerar). Si queremos ser más sofisticados podremos añadir un sistema para controlar también el sentido (adelante/atrás), pero con esos dos que comentábamos es suficiente para empezar.
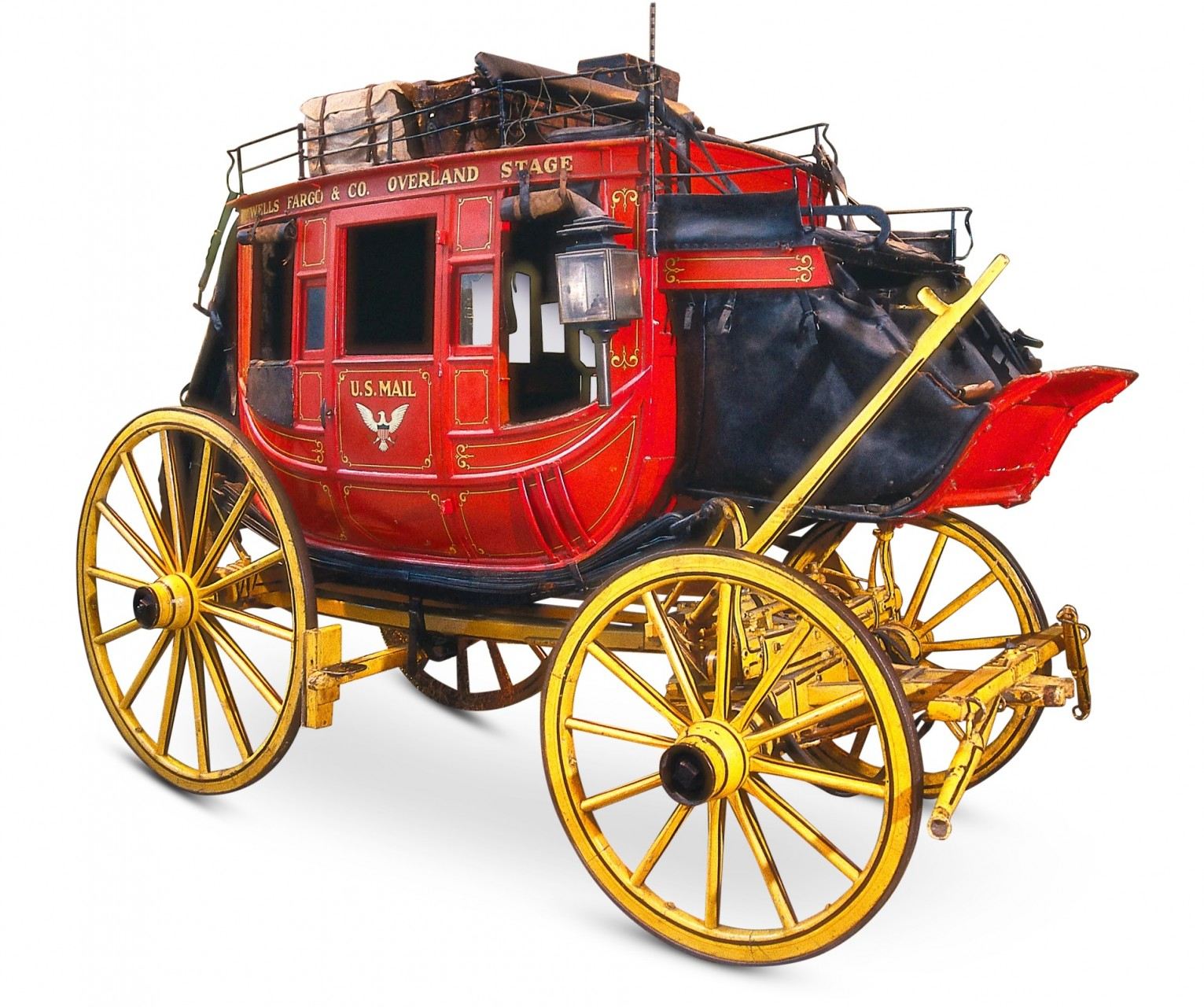
Los frenos más rudimentarios ya se instalaban en los carruajes. Fijaos en la zapata de madera en la rueda trasera, conectada con la palanca de freno
Pensemos en la era previa a la automoción, donde los carruajes o coches de caballos eran el único medio de transporte disponible. Ya fueran de un solo equino o varios, la dirección se manejaba a través de las bridas que llevaba el cochero entre sus manos. Para girar a la derecha le bastaba con tensar la brida derecha, y para girar a la izquierda, lo mismo con la otra brida. En los modelos con un solo eje, el propio caballo hacía de pivote para la dirección, mientras en los de dos ejes, el delantero pivotaba bajo los pies del cochero junto al caballo o caballos.
En cuanto al control de velocidad, se hacía también a través de las bridas de los caballos, agitándolas para acelerar o tirando para frenar. Seguramente os preguntaréis qué tiene todo esto que ver con el reportaje de hoy. Pues bien, en estos carruajes es donde nos encontramos los primeros frenos de la historia.
En principio se trataba de un freno de estacionamiento o de emergencia y no se usaba durante la marcha, a no ser que los caballos se desbocasen. Se trataba de una palanca que movía el cochero a voluntad, que hacía presionar una zapata contra las ruedas traseras del carruaje. Recordemos que estas ruedas eran de madera, con radios también de madera, cubiertas con un aro metálico en su parte exterior. Esta zapata podía ser de madera o incluso piedra en los más rudimentarios.
Es muy difícil datar el empleo de los primeros frenos en los carruajes, pero según algunos estudiosos del tema, podría decirse que debió ser en algún momento entre el s. XVIII y s. XIX. Aquí es donde comienza la historia de los frenos.
Los que amamos el automóvil le debemos mucho a Bertha Benz –Bertha Ringer de soltera-, por su atrevimiento a probar el primer automóvil de la historia, que diseñó su marido, Karl Friedrich Benz
Como todos sabemos, el primer automóvil de la historia fue el Benz Patent-Motorwagen de 1885. Con una apariencia muy similar a un carruaje de caballos, pero cambiando los equinos por un motor monocilíndrico de 954 cm3 y 0,7 caballos de vapor. El motor llevaba una polea contrarrotante que era paralela al suelo, siendo aquí donde se realizaba el frenado. Mediante una palanca el conductor movía una zapata que, por rozamiento con esta polea, hacía decelerar al automóvil. Fue Bertha Benz, en el primer viaje de la historia del automóvil en agosto de 1888, la que perfeccionó el freno añadiendo una capa de cuero a la zapata.
Más tarde, un tal Herbert Frood inventó el primer material de forro para frenos en 1897, fundando la Ferodo Company en el mismo año -ahora ya sabemos de donde viene llamar “ferodo” al material de las pastillas de freno-. Dos años más tarde, en 1899, Gottlieb Daimler teorizaba sobre el uso de algo parecido a un freno de tambor accionado por un cable hasta que, en 1901, Wilhelm Maybach diseñó el primer freno de tambor interno.
Al año siguiente, en 1902, Louis Renault, aprovechando las innovaciones anteriores de Frood, Daimler y Maybach, desarrolló de manera práctica el freno de tambor mecánico con revestimiento de asbesto (amianto), que se accionaba mediante cable de acero. Sería el nacimiento del primer freno de tambor para automóvil.
No sería hasta 1950 cuando se desarrolló el freno de tambor con ajuste de desgaste automático, que evitaba los reajustes manuales cada cierto número de kilómetros. Los automóviles ganaban potencia y velocidad, y los frenos de tambor ya no eran suficientes. Se calentaban en exceso y su potencia de frenado disminuía alarmantemente.
Aunque el invento de los frenos de disco data de 1902 y se atribuye a Lanchester, no sería hasta 1953 cuando se aplicarían con éxito por primera vez a un automóvil. Esto fue en un Jaguar C-Type, que compitió en Le Mans ese año, haciéndose con la primera, segunda y cuarta plaza. Pero no sería hasta el 5 de octubre de 1955, con la llegada del Citroën DS, cuando los frenos de disco se montasen en un coche de serie.
Un sistema de ayuda a la frenada se desarrollaba junto a los frenos de disco: el ABS. El Anti-lock Braking System o Anti Skid fue una patente de Karl Wessel de 1928, tratándose de un sistema mecánico muy rudimentario. En 1936 Robert Bosch patentaba otro sistema similar, aunque ninguno sería construido o aplicado entonces.
Fue en los primeros años de 1950 cuando Dunlop Maxaret incorporó un sistema mecánico antibloqueo a los aviones de la época, como el Avro Vulcan, de Havilland Comet 2C o Fokker F27. No sería hasta 1960 cuando el Concorde emplearía el primer sistema ABS completamente electrónico. Desde entonces solamente se aplicaría en aviación, hasta 1978, cuando se ofrecería el ABS de cuatro canales por primera vez como opción en un coche de serie, el Mercedes-Benz Clase S (W116).
El Concorde fue un avión innovador en todos los sentidos, trasladando parte de su tecnología al mundo del automóvil
A partir de este momento los frenos de disco y el ABS se irían imponiendo poco a poco en todos los vehículos de serie, por todas las ventajas que aportan en la seguridad, suavidad de funcionamiento y disipación de calor, aunque aún hoy en día se siguen empleando tambores en el eje trasero en vehículos de corte económico y poco potentes, debido a su bajo coste. Por suerte, el ABS es obligatorio en la Unión Europea desde 2003.
Solo nos queda una innovación más: los frenos de disco de carbono. Su primera utilización fue en el Concorde en 1976, empleándose por primera vez en un automóvil en el año 1979, en el Brabham BT49 de Fórmula 1, siendo enteramente de carbono. No fue hasta el año 2000 cuando se emplearon discos carbonocerámicos en un coche de serie, siendo el Mercedes-Benz CL 55 AMG F1 Limited Edition el primero en utilizarlos. Luego llegaría el Porsche GT2 (996) en 2001, equipando también este tipo de frenos.
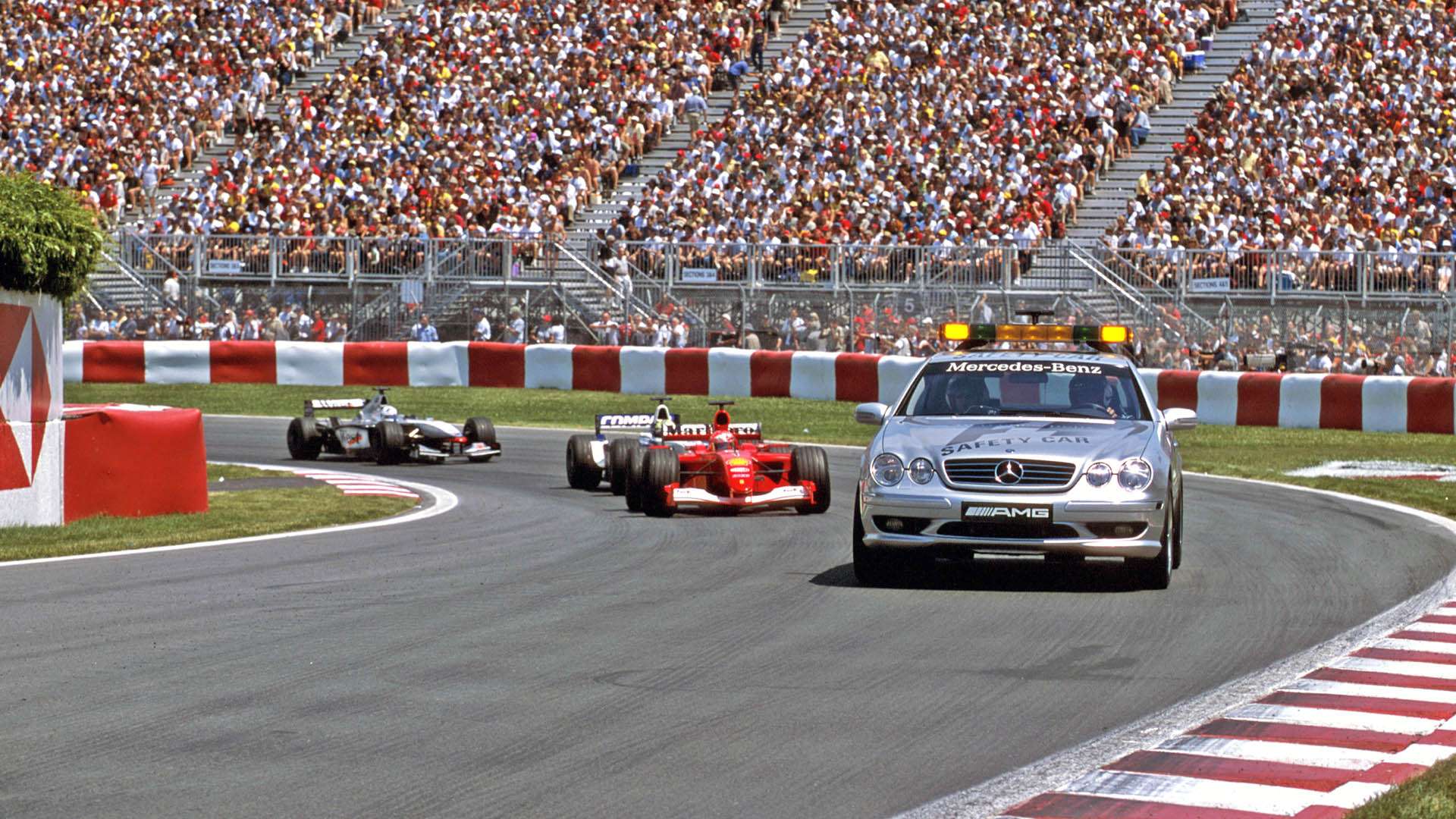
Sistema básico de frenos
Conceptualmente un sistema básico de frenos se compone de un sistema de control, un sistema de envío de fuerza de frenado, uno o varios rotores y uno o varios estátores.
El sistema de control puede ser una palanca, como hemos visto antes en los carruajes, o un pedal de freno, como en los coches actuales. El conductor, regulando la fuerza que aplica, consigue regular la deceleración del vehículo.
El sistema de envío de la fuerza de frenado transmite la fuerza aplicada en el sistema de control por el conductor al estátor. Este sistema puede ser mecánico, empleando varillas o cable de acero; hidráulico, donde un fluido transmite la fuerza; o neumático, donde la fuerza se transmite mediante aire comprimido. También puede ser eléctrico, como el freno regenerativo de los vehículos eléctricos o los frenos electromagnéticos de vehículos pesados.
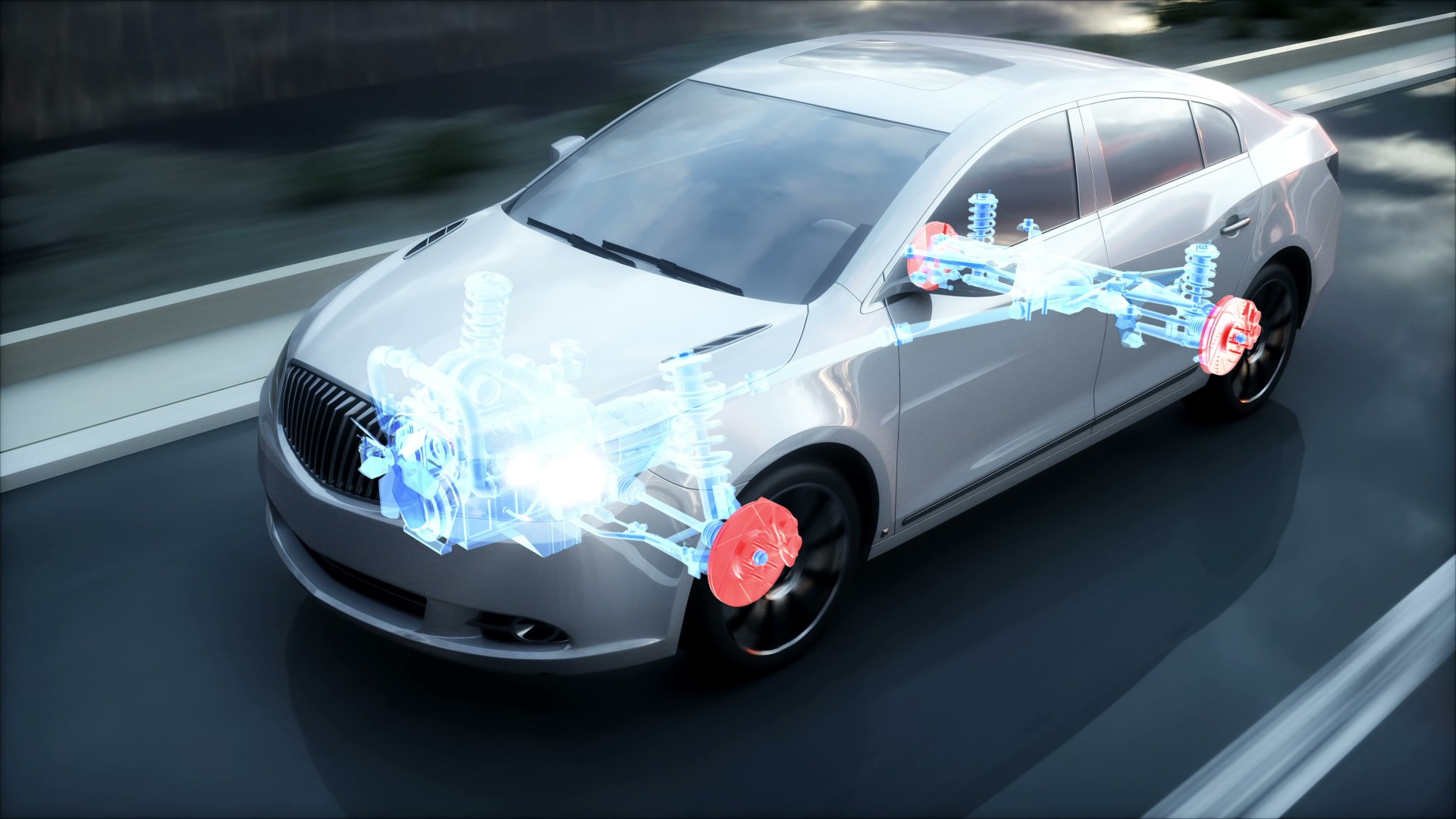
El rotor puede ser desde la rueda del carruaje, la rueda de una bicicleta, el tambor o el disco de freno, mientras el estátor puede ser la zapata de un carruaje o bicicleta, las zapatas interiores de los frenos de tambor o las pinzas de freno y sus pastillas en los de disco. En un freno electromagnético, el rotor serán dos discos metálicos, mientras el estátor serán varios bobinados de cobre.
El funcionamiento del sistema de frenado es muy sencillo. Al aplicar una fuerza en el sistema de control, esta fuerza se transmite al estátor a través del sistema de envío de fuerza de frenado, que presionará al rotor creando calor por rozamiento y disipándolo en el ambiente. De esta manera se reduce la velocidad, al cambiar la energía cinética (movimiento) en térmica (calor).
No os preocupéis si no se entiende algún concepto, porque los explicaremos más adelante. Esto es solo la composición básica de cualquier sistema de frenado para situarnos en contexto. Luego veremos en profundidad los componentes de un sistema de frenos actual para llegar a comprenderlo en profundidad.
Tipos de sistemas de frenado
Tras este breve repaso histórico por la historia de los frenos en el automóvil y conocer cómo es un sistema básico de frenado, llega la hora de clasificarlos para ir comprendiendo mejor su funcionamiento. Básicamente podemos dividirlos en dos categorías básicas: por el tipo de circuito que se emplea para transmitir la fuerza del pie hasta los frenos, o por el tipo de rotor empleado.
No vamos a incluir aquí el freno motor, que, aunque disminuye ciertamente la velocidad a costa del trabajo del motor, no es un sistema como tal, salvo en algunos camiones diésel americanos. Si habéis viajado por allí, os habréis dado cuenta que cuando frenan se escucha un petardeo enorme. Esto se debe al “Jacobs brake” o “Jake brake”, que no es más que un subsistema que, cuando está conectado, abre la válvula de escape para liberar los gases en el cilindro después de la compresión, de manera que se reduce la velocidad al no devolver energía al cigüeñal.
Debido al exceso de decibelios de este tipo de freno motor, hay señales específicas en América que regulan la utilización de este tipo de freno para los camiones, no permitiéndolo dentro de la ciudad o a determinadas horas de la noche.
A) Por el tipo de sistema de envío de la fuerza de frenado
A-1. Mecánico
En este caso lo que se encuentra entre el conductor y el conjunto rotor/estator es un sistema mecánico. En la antigüedad, como hemos visto, era una palanca con varillas, y posteriormente, con la aparición de los automóviles, se comenzó a aplicar un cable de acero. Bien mediante una palanca o mediante un pedal, el conductor trasmitía la fuerza de frenado al tipo de frenos que equipase el automóvil, típicamente junto a este sistema, frenos de tambor, que veremos más adelante.
A-2. Hidráulico
Este sistema se comenzó a emplear en 1921 en el Duesenberg Modelo A, aunque no fue hasta 1939 cuando Ford lo incorporaba en sus vehículos de serie, popularizándolo entre los vehículos más modestos. Aún en esta época se empleaban frenos de tambor, y no sería hasta la llegada del Citroën DS en 1955, cuando se combinaría el sistema hidráulico con los frenos de disco.
Este sistema hidráulico se combinaba con el servofreno, que no es más que un amplificador de la fuerza que ejercemos sobre él aprovechando el vacío de la admisión. Por primera vez fue montado en un Pierce-Arrow de 1928, y desde entonces se popularizó, formando parte del sistema de frenos de cualquier automóvil con mecanismo hidráulico.
En este sistema el pedal mueve un cilindro que a su vez empuja un fluido incompresible -o sea, que no se comprime-, enviando la fuerza a los cilindros esclavos en el caso de los tambores o a las pinzas, en el caso de los frenos de disco.
El sistema hidráulico aprovecha la Ley de Pascal para transmitir la fuerza de frenado, donde una pequeña fuerza, pero de gran recorrido en el pedal, es transformada en una gran fuerza de menor recorrido en el tambor o en la pinza de freno. De esta manera se transmite la fuerza del conductor para decelerar el vehículo.
Al comienzo de los tiempos, cuando aún no existía el ABS, constaba de un circuito único para las cuatro ruedas, con válvulas proporcionales para repartir adecuadamente la potencia de frenado entre el eje delantero y trasero y entre la parte derecha e izquierda. El problema de este diseño es que, si fallaba el circuito, te quedabas sin frenos.
Posteriormente se incorporó un circuito más, haciéndolo redundante para evitar fallos catastróficos. La rueda delantera derecha y la trasera izquierda se situaban en un circuito, y las otras dos ruedas en el otro, se llamada circuito cruzado o en “X”. De este modo si fallaba uno de ellos, disponíamos de freno tanto delante como detrás.
Si hay un sistema que nunca debería fallar en un automóvil, este es el de frenado
Con la llegada del ABS todo esto cambió, pues a partir de este momento cada rueda tenía su circuito independiente, aumentando por tanto la resistencia a fallos en uno de los circuitos. La redundancia que sí se mantuvo es el doble circuito que comunica el cilindro maestro con la unidad de ABS. Luego lo veremos con mayor profundidad.
A-3. Neumático
Este sistema no se suele emplear en coches, aunque sí en camiones, autobuses, trenes o transporte pesado. Data de 1860 y fue desarrollado por George Westinghouse para los trenes. Se trata de un circuito de aire a presión con acumuladores. Cuando el conductor frena, la presión de aire en el circuito principal disminuye, abriendo las válvulas de los acumuladores que presionan los pistones de las pinzas o tambores para frenar. De este modo si se daña el circuito y tiene fugas, se aplicarían los frenos por seguridad.
Un compresor se encarga de que siempre haya aire suficiente en los acumuladores para conseguir la presión necesaria en el circuito de frenado. Es por esto que se escuchan esos silbidos tan característicos en los camiones o autobuses cuando frenan: se trata de una válvula de escape que libera el aire del circuito con exceso de presión.
A-4. Eléctrico/Electrónico
En este caso el circuito para aplicar fuerza de frenado es eléctrico, y puede haber dos casos: cuando se emplea un freno electromagnético o retardador, o cuando estamos ante un vehículo híbrido/eléctrico con freno regenerativo. En ambos casos será una corriente eléctrica la que transmita la fuerza de frenado, en forma de corriente para el freno electromagnético o en forma de señal electrónica y corriente de carga hacia la batería, en el caso de los híbridos/eléctricos.
También podemos considerar dentro de este sistema los frenos By-Wire, en donde una señal eléctrica emitida por la centralita indica a la bomba/bombas de freno la presión de frenado que debe aplicar en cada rueda. No hay una conexión mecánica.
B) Por tipo de conjunto rotor/estátor
B-1. De tambor
El freno de tambor como ya hemos visto se monta en los automóviles desde principios del s. XX y en la actualidad se sigue empleando en el eje trasero de vehículos de bajo coste y baja potencia, pues las necesidades de frenado en la parte de atrás no son tan exigentes y cumplen adecuadamente.
En este caso, el rotor es el tambor, esa parte metálica que envuelve el mecanismo y gira solidariamente a la rueda. Su cara interna es la que hará rozamiento con las zapatas interiores. El mecanismo puede ser mecánico, a través de cable; hidráulico, a través de un cilindro esclavo montado en el interior del tambor; o ambos, combinando el freno de estacionamiento con el freno de servicio.
En ambos casos se empujará la parte superior de las zapatas hacia el exterior, para que su fricción con el tambor detenga el movimiento. En la parte inferior hay un muelle y un regulador automático, que irán acercando progresivamente el pivote inferior de las zapatas hacia el tambor, para que siempre entre en contacto toda la superficie, tanto si son nuevas como si están al final de su vida.
La ventaja de este tipo de freno es que la superficie de fricción es grande y su potencia de frenado también lo es, aunque decrece rápidamente debido a su gran desventaja: la refrigeración, o más bien la ausencia de ella. Al estar confinados sus componentes dentro del tambor, el calor no se disipa de manera rápida, por lo que este tipo de frenos se sobrecalientan con facilidad, disminuyendo el rozamiento con la temperatura y, por tanto, decreciendo su potencia de frenado.
Otra de sus ventajas es su bajo coste de producción, por eso se siguen empleando en la actualidad en vehículos de coste contenido del segmento A y B, pues las necesidades de frenado del tren posterior no son tan exigentes y cumple adecuadamente si no se le exige mucho.
B-2. De disco
Como ya habréis adivinado, este sistema emplea discos de freno como rotor y pinza con pastillas de freno como estátor. Por primera vez se montó en un vehículo de serie en el Citroën DS de 1955 y desde entonces ha predominado como elección principal, al menos en el tren delantero, que a fin de cuentas es el que más potencia de frenado requiere, independientemente de si es el eje tractor o no.
Su funcionamiento es sencillo: el disco gira solidario a la rueda y es la pinza la que mediante un pistón hidráulico presiona las pastillas para que realicen la fricción contra él. De este modo se reduce la velocidad de giro de la rueda, que, a su vez, frena el vehículo.
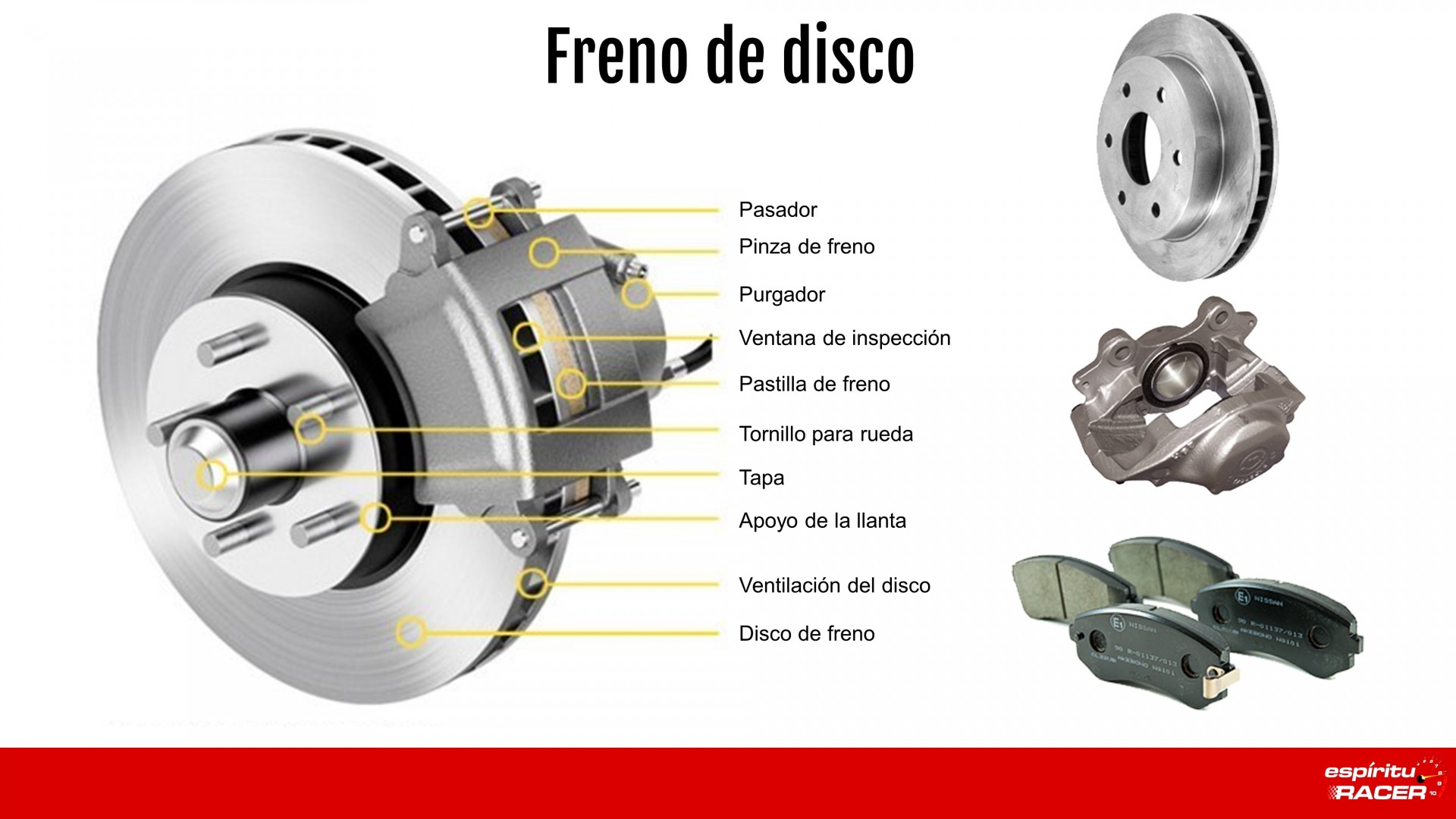
La ventaja del freno de disco frente al tambor es que se encuentra en contacto con el aire, por lo que la transferencia de calor al mismo es mayor. Recordemos que al final lo que queremos es convertir la energía cinética en calor para frenar el vehículo, y los discos de freno realizan este trabajo de manera más eficiente, transfiriendo más rápidamente ese calor al aire.
Aparte de la eficacia, su frenada resulta más suave y dosificable que un freno de tambor, algo más tosco y rudimentario en su tacto. Existe una aplicación muy específica de los frenos de disco y es en aviación. En este caso el mecanismo es intercalar discos móviles (fijados a la rueda mediante unos salientes) con discos fijos, de manera que cuando los pistones presionan para ejercer la acción de frenado, toda la superficie de todos los discos se emplea en esta acción. Podéis verlo en la foto de arriba de los frenos del Concorde, donde se aprecian cinco discos móviles y seis discos fijos.
Existen diversos tipos de discos de freno según si son ventilados o no, con diferentes superficies y materiales, al igual que existen dos tipos de pinzas, fijas y flotantes. En el siguiente apartado contaremos en detalle cada uno de ellos.
B-3. Electromagnético
En este tipo podrían entrar dos subtipos: los frenos regenerativos de un coche híbrido/eléctrico y el freno electromagnético empleado en camiones y autobuses, también conocido como retardador.
Respecto a los híbridos/eléctricos no existe un freno como tal, sino que es un motor eléctrico trabajando como generador, debido a la reciprocidad/dualidad que tienen este tipo de motores. Al frenar, el motor eléctrico generará una corriente para cargar las baterías, proporcional al recorrido del pedal del freno. Lo veremos más en detalle al final. En este caso no se genera calor, sino energía eléctrica, mientras esta pueda ser acumulada.
En vehículos híbridos y eléctricos la frenada eléctrica bien utilizada hace que el sistema de frenado convencional tenga una vida útil mucho más larga y se evita la emisión de partículas de material de fricción
Entrando en el freno electromagnético como tal, consta como todos los frenos, de un rotor, que suelen ser discos metálicos, y un estátor, que son un cierto número de bobinados o inductores de cobre.
Su principio de funcionamiento es sencillo. Un disco que gira dentro de un campo magnético recibirá unas corrientes eléctricas inducidas denominadas corrientes de Foucault. A mayor campo magnético, mayores corrientes.
Por tanto, si aplicamos corriente eléctrica al estátor, cada bobinado generará un campo magnético, proporcional a la corriente que pasa por sus hilos. Esto creará un campo magnético perpendicular a su abertura que atravesará el disco metálico, y que intentará frenarlo, oponiéndose a su giro. Para simplificar, es como un disco de freno con pinzas virtuales.
Estos discos normalmente giran solidarios a los palieres de transmisión y están ventilados, pues se calientan gracias a las corrientes de Foucault. No logran una gran potencia de frenado como para detener completamente el vehículo, pero sí reducen la velocidad de manera constante, segura y muy suave. Se suelen emplear en descensos de puertos largos o pendientes descendentes pronunciadas, como complemento a los frenos de disco.
Tiene la ventaja que sus piezas no están sujetas a desgaste, y que pueden aguantar un trabajo prolongado, por lo que no están sujetos al tan temido fading. Se suelen accionar mediante una palanca situada a la derecha de la piña del volante, que tendrá diferentes posiciones -normalmente cuatro- según queramos aplicar más o menos retención. A más retención, mayor consumo eléctrico.
Para que nos hagamos una idea de los valores, un freno electromagnético pequeño puede pesar unos 70 kg y consumir unos 1,2 kW de potencia eléctrica para producir unos 50 CV de frenado. Los más grandes pueden llegar a 500 kg de peso, con un consumo de unos 4 kW de energía eléctrica y los 600 CV de potencia de frenado. Como es natural, a mayor freno eléctrico, mayor alternador será necesario. En la foto superior podemos ver un ejemplo de freno electromagnético de la empresa Frenos Iruña.
https://www.youtube.com/watch?v=RrNhJ2nXN40
B-4. Hidrodinámico
Este sistema se emplea en transporte pesado, igual que el ejemplo anterior. Se trata de algo muy parecido al convertidor de par de una caja de cambios automática. Se conecta a la salida de la caja de cambios, y consta de una parte fija y una parte móvil, ambas con álabes en su interior. Cuando el conductor pisa el freno o acciona la palanca de control junto al volante, el retardador entra en funcionamiento. Se bombea aceite al interior, siendo movido por el rotor.
El propio rozamiento del aceite con los álabes del rotor contra el estátor, genera un par de frenado, calentando el fluido y convirtiendo la energía cinética en calor. Este sistema cuenta con un intercambiador de calor, para mantener el fluido dentro de sus temperaturas de trabajo, no requiriendo energía como el freno eléctrico, y aliviando a los discos de freno de la mayor parte de la carga de trabajo. Según algunos fabricantes, puede realizar el 90 % de las tareas de frenado de un vehículo pesado.
Hasta aquí la primera parte del sistema de frenos, donde hemos visto su origen, su clasificación por el sistema de envío de la fuerza de frenado y por el tipo de conjunto rotor/estátor. En el siguiente capítulo contaremos al detalle de qué se compone un sistema de frenos actual y algunas directrices sobre su diseño.
Pablo Mayo
Ingeniero de profesión, la mayor pasión de mi vida son los coches desde que era un chaval. El olor a aceite, gasolina, neumático...hace que todos mis sentidos despierten. Ahora embarcado en esta nueva aventura, espero que llegue a buen puerto con vuestra ayuda. Gracias por estar ahí.COMENTARIOS